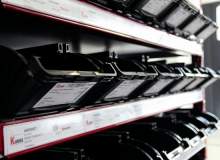
The highly flexible Kanban systems offered by Würth Industrie Service under the CPS®KANBAN service brand help to make warehouse and production effective and transparent. These Kanban systems are used predominantly by major industrial customers in the manufacture of their installations and products.
The most suitable solution for automatic replenishment is implemented, tailored to the particular item and to the individual work situation and requirements. Maximum availability of the right item in the right quantity in the right place at the right time in the production facility itself is always paramount.
The principle of the Kanban system, which originated in Japan, is simple. It is a rolling two-bin system that, in contrast to traditional supply methodologies, provides C-Parts ‘just-in-time’ directly at the point of use. The system demonstrates great potential for adjustment if requirements change, maximum delivery and supply security at reduced inventory levels and minimal capital commitment.
The flow of materials in Kanban systems from Würth Industrie Service is managed via two bins, each of which has a barcoded Kanban label, RFID tag or iBin® module, which specifies the customer, storage location, item, bin, batch and quantity in more detail.
Each bin movement is captured and documented, so that Würth Industrie Service can give information about the status of the Kanban system at any time. This is enabled by Kanban management software developed in-house and the specialised European Kanban logistics centre in Bad Mergentheim, as well as the barcoded labels, RFID tags or iBin® modules.
The data is used to schedule all C-Parts close to the point of use, to optimise stock levels and warehouse technology regularly and to update statistical data. As a customer, you can also find all of the data using the CPS®ONLINE information platform.