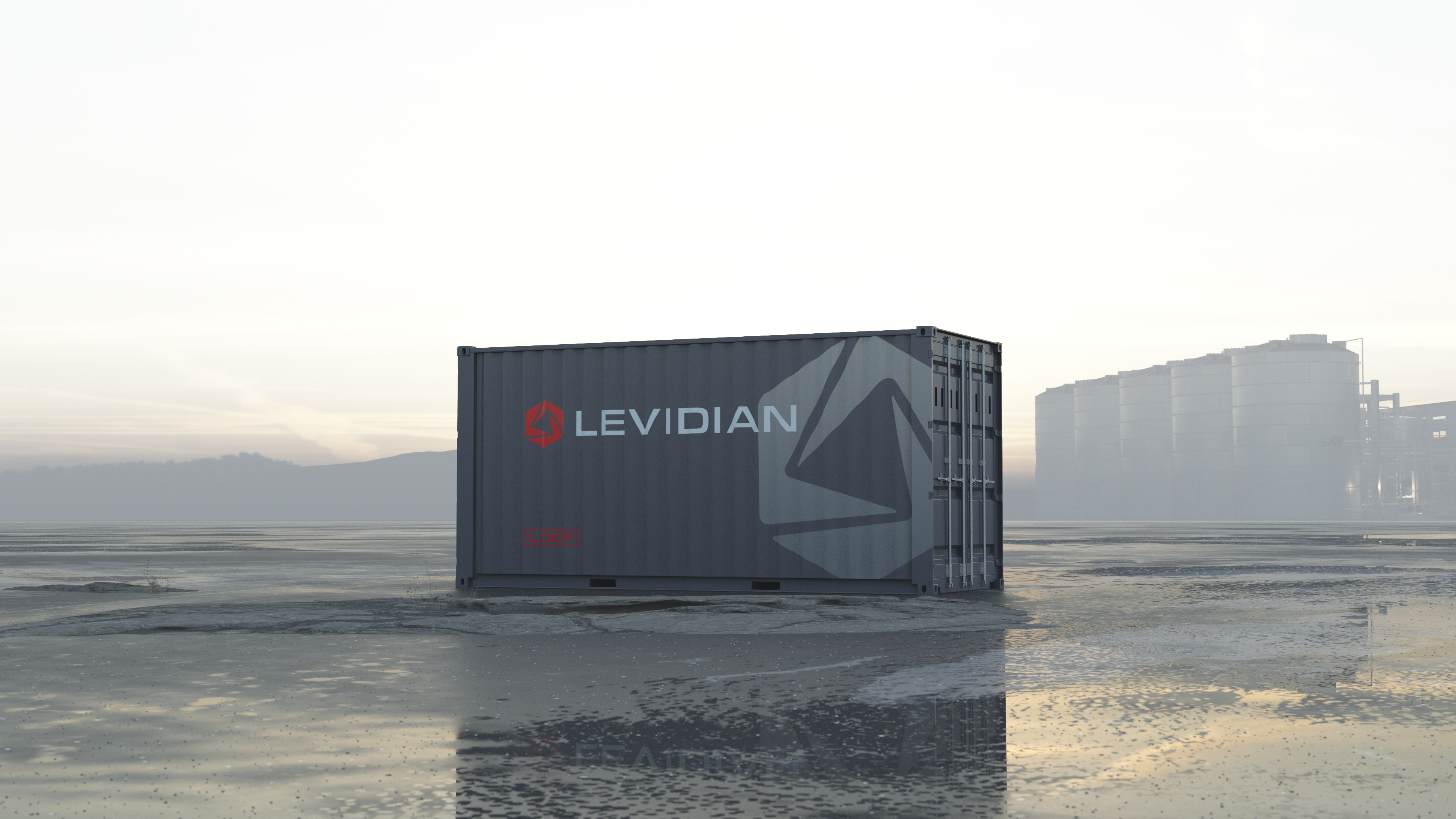
For its weight, graphene is the strongest material ever created, and making it only requires a pencil and some sticky tape. Although researchers have known of the material for decades, the material only started gathering serious attention in the early 2000s. This was when materials future Nobel prize-winners Andre Geim and Konstantin Novoselov discovered they could repeatedly use adhesive tape to isolate extremely thin layers of graphene, down to one atom thick.
Graphene has high conductivity for heat and electricity, low reactivity, and can self-repair when exposed to carbon. It is transparent, but airtight, and has the highest tensile strength of any material ever tested. All these qualities give graphene massive potential, but in 2022, most of the potential remains unrealised.
How well do you really know your competitors?
Access the most comprehensive Company Profiles on the market, powered by GlobalData. Save hours of research. Gain competitive edge.
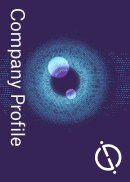
Thank you!
Your download email will arrive shortly
Not ready to buy yet? Download a free sample
We are confident about the unique quality of our Company Profiles. However, we want you to make the most beneficial decision for your business, so we offer a free sample that you can download by submitting the below form
By GlobalDataThe graphene market remains relatively small, valued by various analysts as between $90m and $130m in 2021. Among its many potential uses, energy sector researchers have made promising tests on graphene supercapacitors, perovskite solar cells, and anti-corrosion barriers, among other applications. Decarbonisation investment fuels some of this research, although much larger sums go toward hydrogen generation and carbon capture, utilisation, and storage (CCUS) facilities.
British startup company Levidian hopes to take a slice of all three of these markets. The company has patented a system for manufacturing graphene and hydrogen from natural gas, which it calls Loop. Rather than sticky tape, the system uses super-hot plasma to remove up to 40% of carbon from methane inputs. The system then outputs graphene and a hydrogen/gas blend, which can decarbonise gas networks without pipe replacement.
This year, the company will start a pilot project with the UK’s National Grid. Here, engineers will use manufactured graphene to internally line gas pipes, reinforcing them with a corrosion-resistant coating. Soon, the UAE’s Zero Carbon Ventures will begin deployment of the 500 Loop systems it purchased in May. These, Levidian says, will reduce natural gas emissions by 500,000 tonnes of CO₂-equivalent over the deal’s 10-year course.
We spoke to Levidian CEO John Hartley about where the Loop system fits into the carbon cycle, and how it feels to lie at the centre of three up-and-coming markets.
Matt Farmer (MF): The CCUS, graphene, and hydrogen markets are all expanding, but do you believe they are simultaneously growing enough to support the Loop system?
John Hartley (JH): We’ve seen huge amount of public and private investment channelled into these sectors, which we expect will continue. The global challenge of decarbonising while continuing to support global growth is an existential one – if anything we anticipate increasing focus on these markets over time.

We already have greater demand for Loop systems than our current production capacity after introducing the technology into a relatively small number of sectors. This is a strong indicator of the future opportunity for the system.
There are of course hurdles for these markets to cross. In hydrogen, we need to push for the refocusing of categorisation on carbon footprint rather than production methodology. We have seen some early steps in this direction from the UK Government and continue to support further development of these standards. There are also challenges around how we deploy hydrogen: Loop’s unique ability to deploy at point-of-use for industrial customers means this is less of a challenge for us.
Graphene has, historically, been a solution looking for a problem. As a result, it hasn’t seen the massive uptake that was predicted back when it was discovered. For us, decarbonisation is that problem. With that in mind, we expect to see increasing interest for applications where we can improve product performance and longevity, for example.
Graphene also suffers from a lack of standardisation. We’re working with industry and government to push for better definition, to enable graphene to commercialise.
MF: As you said, the Loop system can act as an end-use system with usable byproducts, but it can also be more of a midstream value-adding process. Which of these do you think will be more prevalent?
JH: Neither! We expect many users to apply Loop as an end-use system. For industrial applications, the ability to decarbonise on-site without significant changes to infrastructure is an important opportunity. The added benefit of creating graphene, a high-value product, is significant. Customers can use this on site – it has several applications, including in concrete and tyre production – or capture for resale.
There is also opportunity for Loop in midstream applications. This could be increasing the hydrogen concentration in the grid, as our National Grid trial will explore. It could also be at sites producing biogas or biomethane, as part of the transition towards hydrogen production.
Finally, we have applications at wellhead sites. Utilising flare gas to produce graphene and hydrogen can generate new value streams.
It’s worth clarifying that the 40% carbon removal statistic is based on a single pass through the Loop system. In applications where the hydrogen is separated, we can then remove all of the carbon by recirculating the exhaust gas back through Loop.
Do you expect to see the system deployed more frequently at methane sources, such as in natural gas processing, or at graphene-consuming manufacturing facilities?
JH: Our early deployments will be primarily at methane sources, including our first customer, Zero Carbon Ventures, who will deploy more than 500 Loops to landfill and glare sites in the UAE. We expect to be making more announcements along this line soon.
As other customers develop their graphene applications, we expect that there will be an increasing number of Loop deployments on sites where graphene is also utilised. Our trial with National Grid is also exploring the application of graphene in pipeline coatings, so this is one example of a multi-purpose application. We have a number of additional opportunities in development currently, that would include the on-site use of graphene.
What do you expect to learn from the National Grid trial?
JH: The National Grid partnership will help us understand how we use graphene to improve existing gas infrastructure. The trial will test performance of graphene-lined pipes and trial different concentrations of graphene. We can’t share any results yet, but schemes like these could increase the UK’s ability to transport clean hydrogen in future by allowing existing infrastructure to be repurposed without the need for decades-long disruption from major infrastructure redevelopments.
The project will also specifically explore utilising Loop to add hydrogen to the grid – again, another important step towards decarbonising the UK’s energy quickly.
Can the Loop system be adapted for different hydrogen/natural gas ratios?
JH: In terms of the output gas mix, yes. Loop produces a hydrogen/methane mix by default. With the addition of hydrogen separation, we can produce pure hydrogen suitable for use in applications like fuel cells. In terms of the balance between hydrogen and graphene, we are currently doing a number of development trials to explore how we can optimise Loop to deliver the maximum volume of hydrogen for those customers where this is desirable.
Do you expect the methane/plasma method to become the leading way of producing graphene?
JH: Loop’s efficient methane/plasma technology and our future network of Loops will shift production away from more environmentally damaging production methods. Levidian will be producing high-quality, scalable graphene globally. As we grow, we expect the need to produce graphene through those more damaging methods will decrease.