
While the offshore industry is among the most heavily-regulated and safety-conscious in the world, considering the tragic personal and environmental consequences that can come from operational failure, there is one phenomenon that the sector has so far struggled to tackle: hydrogen embrittlement. This process sees machinery weakened over time as hydrogen enters steel and weakens the material on an atomic level. Embrittlement has already been connected to a number of industrial accidents, such as failures in the testing of the San Francisco-Oakland Bay Bridge’s $6bn eastern section, opened in 2013.
Yet the causes of this phenomenon are not fully understood, despite evidence of its occurrence in industrial processes as early 1875. To tackle this gap in knowledge, British chain manufacturer William Hackett has published a report into hydrogen embrittlement, drawing on its extensive industrial expertise and making a number of policy suggestions for the offshore industry to help avoid damage to its machinery. Among its goals are the implementation of new composition standards for a number of products already used in the offshore industry, and to inspire a cultural shift towards collaboration and cross-company support for ways to treat hydrogen embrittlement. But with the phenomenon still something of a taboo in the sector, it remains to be seen if the industry can collectively tackle this threat.
How well do you really know your competitors?
Access the most comprehensive Company Profiles on the market, powered by GlobalData. Save hours of research. Gain competitive edge.
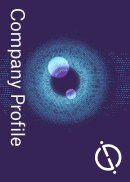
Thank you!
Your download email will arrive shortly
Not ready to buy yet? Download a free sample
We are confident about the unique quality of our Company Profiles. However, we want you to make the most beneficial decision for your business, so we offer a free sample that you can download by submitting the below form
By GlobalDataThreats to offshore operations
The cause of hydrogen embrittlement, as far as it is understood, is tied to the corrosion of machinery by hydrogen produced in industrial environments, corrosion which is “going to be accelerated in any offshore environment”, according to Ben Burgess, director at William Hackett.
“As corrosion takes place, you get a build-up of hydrochloric acid, and then the hydrogen from the corrosion ingresses into the steel structure,” explains Burgess. “As the hydrogen molecules, through the corrosion, migrate into the steel structure, they are drawn to the areas of higher stress, which is typically the ‘crown’. As they congregate in the grain structure of the steel, they create internal pressure, trying to push the steel apart.”
This process of a material being pushed apart from the inside out is what makes hydrogen embrittlement so dangerous as, unlike other weakening of machinery such as cracks or fissures in their surfaces, hydrogen embrittlement is near impossible to observe and to predict. Burgess also noted that as the damage is not caused by conventional stresses in the offshore industry, such as a crane being placed under stress by carrying a heavy load, fractures and breaks can occur when equipment is not under any obvious external pressure, again making it difficult to predict when embrittlement will take place.
Burgess also highlighted the phenomenon of “dynamic load amplification” as another key aspect of the hydrogen embrittlement process. This amplification comes when equipment, such as chains and hoists, is placed in offshore environments, where it has to counteract both the weight of the loads it is carrying and the turbulent forces of the waters below.
“If I’m sat still and I lift my ruler to a certain position, it is the weight of the ruler that I am left holding and that is it,” he explains. “If I’m offshore and I am moving up and down with movement of the sea, the effect of the weight on that ruler changes. Simply put, this is described as ‘dynamic load amplification’; back to the ruler example, at the top of the ruler, the weight is actually lighter but at the bottom of the ruler with dynamic loading, the weight may be double what it is in it in a neutral, onshore state.”
Burgess notes that recent trends in heavy equipment manufacturing have also contributed to the increased threat of hydrogen embrittlement. The steel used in chain manufacturing for instance, has increased from grade four to as high as grade 12, which makes the steel harder and lighter but also makes its grain structure tighter. This means that new steel constructs are safer and more efficient when used onshore, but are at an even greater risk of hydrogen embrittlement if and when they are transplanted to offshore operations.
Mechanical change and operational reform
Among William Hackett’s key recommendations is for industrial products to be designed with the environment they are to be used in in mind. Practically, this means developing hardware for the offshore sector that can deal with the additional stresses generated by dynamic load amplification, and using components with a structure better suited for use in offshore environments. For instance, the company’s report calls for maximum hardness quotas on various types of chains used in the offshore industry and the application of corrosion-resistant finishes to all chain types, to make it more difficult for hydrogen to enter the structures in the first place.
The report also draws a distinction between three types of stresses on machinery that can contribute towards hydrogen embrittlement: the composition of material, which can be controlled, and mechanical stresses and the presence of hydrogen in the atmosphere, factors which cannot be minimised due to the nature of offshore work. Burgess is eager to see progress made on that first point, as this is the only variable that companies can exert meaningful control over.
“What we have from our technical backgrounds and in terms of the products that we manufacture is a detailed understanding of the impact that the environment can have on how a product performs,” he explains. “Any lifting or lashing product is designed to be put under strain. That is what the load is, and you can’t avoid that.
“Operators cannot avoid these mechanical stresses; you are going to have corrosion, and you are going to have dynamic load amplification,” he continues. “But what you can do is design a product that is capable of absorbing those additional stresses.”
Taking responsibility and raising awareness
These dual solutions – managing variables that can be managed and tailoring products to their particular environments – may require additional support and specific activity from the offshore industry, but the sector as a whole has a number of interests in enacting these changes. Whether companies can get ahead of their competitors by embracing mechanical changes or possess a genuine altruistic intent to improve the sector’s safety performance in general, Burgess is optimistic that there will be buy-in from across the sector.
“We believe that by taking an open and consultative approach on the issue and effects of hydrogen embrittlement, as well as the importance of correct material grade selection for use in offshore applications, that our insight and research will be supportive in the decision making of operators globally including the likes of Shell, BP, ConocoPhillips, and Exxon,” says Burgess. “Ultimately, it will be these companies that will be upgrading their product specifications in the way we’re recommending, which will mean that our tier one competitors, who have similar products, will also be able to bid for those opportunities.
“What we are endeavouring to do is limit the confusion of onshore-graded products potentially being selected for offshore operations. Our approach and latest industry findings are providing the necessary guidance on what products should be used for what purpose, so operators have a clear choice between offshore and onshore equipment choices, which in itself will make the industry safer and more efficient.”
William Hackett also aims to draw attention to the threat of hydrogen embrittlement itself. A key contributor to the lack of awareness of the issue is that many operators are, understandably, hesitant to draw attention to accidents and damages at their facilities. This unfortunately means that hydrogen embrittlement remains an under-reported phenomenon compared to, for instance, physical injury, which is a much more obvious danger. Burgess noted that William Hackett has not seen any operational failures associated with hydrogen embrittlement at its operations, so is able to report on the risks without endangering its own reputation, and help break down what could still be a taboo within the offshore industry.
“Historically, the issue of hydrogen embrittlement has not been a topic actively discussed,” he says. “But we are bringing positive change by increasing awareness of this issue, and with the latest hydrogen embrittlement guidance from our industry report, operators will benefit from improved decision making and clarity on correct material grade selection for their offshore projects.”