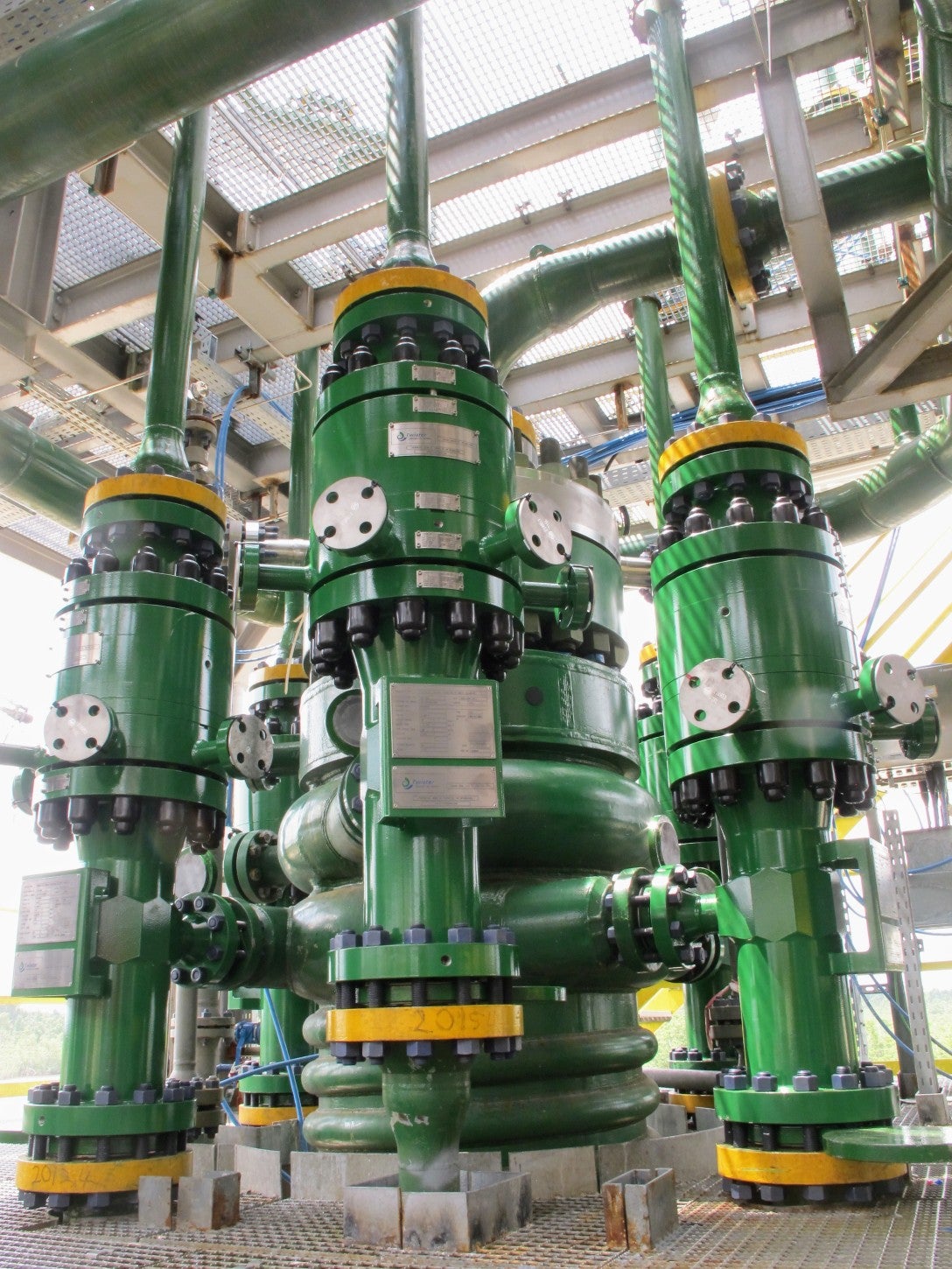
TwistR Energy BV delivers gas processing solutions for dehydration and hydrocarbon-dew pointing of natural gas flows of 20 MMscfd and (far) higher.
Specialised Twister™ technology, a combination of supersonic velocity and extreme vortex, is used:
- supersonic velocity: providing -50°C cooling along with condensing hydrocarbons and water – all in one device
- vortex causing centrifugal forces of 500,000 g to swirl the condensate out of the gas stream.
Combining supersonic speed and swirl eliminates the need for the usual chemicals to be applied to dehydration. This results in a substantial reduction in equipment, but more importantly, it completely obviates the need for operators to handle chemicals or solvents: no regeneration, logistics, storage, piping, seal leakages, repairs, or quality control laboratories. Moreover, there are no BTX emissions, thus improving the operation’s ESG index.
Hydrate Separators for the offshore industry
Smart engineering prevents the formation of hydrates, allowing for deep cooling without the need for hydrate inhibition. Our proprietary Hydrate Separator (HS) handles any hydrates formed in the liquids downstream. As previously stated, there are no chemicals.
There are currently 22 Twister Supersonic Separators (TSS) in operation globally. They have accumulated more than 3 million hours of reliable and safe operation, operating continuously for more than 20 years in onshore and offshore (sour) gas environments with virtually zero maintenance requirements.
All TSS have a proven, unmatched availability of >99% because they operate without moving parts. Twister is completely static: only the gas moves
Many years of R&D combined with rigorous field testing have resulted in very accurate Computational Fluid Dynamics models, which allow the TwistR Energy engineers to predict the behaviour of gas on a virtual molecular level.
Natural gas behaviour simulation
The same CFD technology used to design the ultimate Formula 1 car was also used to calculate and predict the behaviour of natural gas in the Twister units. We have expertise in multi-component non-equilibrium simulation of natural gas behaviour to design all Twister equipment (TSS and HS) for any natural gas of any composition, at any pressure, and any temperature. The value is clear: the pre-designed geometry defines the plant’s performance. Performance is no longer dependent on the quality of chemicals or the competence of operators during work shifts.
This will avoid unexpected penalties for off-spec deliveries and fluctuations in the balance sheet.
Due to the absence of chemicals, a regeneration unit is completely unnecessary. This reduces the facility’s footprint significantly; for example, the required surface of an offshore platform can be reduced by 20%-40%, or likewise, an eight-leg platform can be decreased to a six or even a four-leg platform. Similarly, onshore plants have a 40%-50% reduction in civil works, reducing the development by 30% of the total cost.
Twister as an FID-enabler
Because Twister is based on isentropic expansion, it can expand the gas deeper to achieve a far lower temperature per unit pressure drop than conventional Joule-Thompson valves—which operate with isenthalpic expansion—and comes close to the temperatures that a Turbo-Expander achieves. Depending on the gas composition, a Turbo-Expander may have a higher number of barrels per day, but per year, Twister surpasses the Turbo-Expander due to its higher availability.
From conceptual design to FEED and Detailed Design, TwistR Energy assists the selected (EPC) contractors and key equipment suppliers in completing their engineering exercise so that the envisaged values are realized. TwistR Energy also assists with (pre)-commissioning and start-up. The Twister Module Control System is integrated into the overall plant Control & Safety System, thus reducing commissioning time and smoother operations with minimum interferences or process upsets. TwistR Energy has demonstrated a substantial reduction in start-up costs and post-commissioning tweaking.
Optimised digital transformation for gas operations
TwistR Energy offers the full range of required support services to make a gas business more profitable by increasing revenues and lowering costs and risks. The Twister technology simplifies the plant, leading to multiple operational optimisations, one of which is that the plant can be fully digitised. This facilitates fully unmanned operations in harsh, remote areas, digital twins, real-time data analysis and the application of all of today’s available plant optimisation technologies from anywhere and at any time.
Twister allows the gas plant to be a fully digital entity in the data architecture rather than a semi-automated, manually operated ‘challenge’. The TSS reduces not only the number of operational staff required on site but also in the back office.
Twister is synonymous with increased availability, highest revenue, and lowest cost.
We are proud to have converted many sceptical operators and engineers into outright enthusiastic supporters.
No Chemicals
There are no chemicals to dehydrate sweet or sour gas, so there is no need for expensive additives, regeneration, storage or logistics, thus reducing equipment significantly and contributing positively to ESG.
High Availability
Unmatched system availability and reliability, and no more unplanned outages. More than 99% availability ensures higher production than conventional technologies. Twister has proven that power plants become very reliable when their gas turbines can run smoothly, receiving a continuous supply of on-spec gas.
Deeper Cooling, more Condensate
Supersonic velocity achieves more efficient cooling, resulting in more condensate production. Twister’s isentropic expansion and cooling is the most efficient pressure conversion to cooling.
Minimum Operator Intervention
Designed for minimal operator intervention and combined with digitization, Twister enables unmanned and remote plant operation. Low maintenance requirements, simplified safety systems, and chemical-free operation ensure lower operating costs than conventional technologies, making Twister an economically more efficient solution.