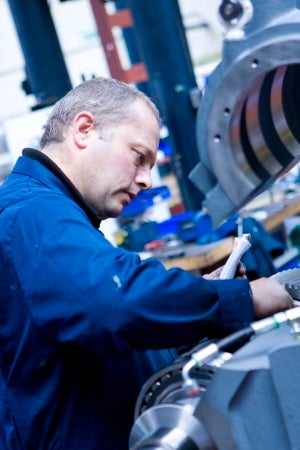
With any capital investment, it is important to ensure that new equipment provides continued, reliable operation on a day-to-day basis, as well as achieving the shortest return on investment (ROI). For those applications operating high-pressure pumps, condition monitoring of the pump and energy efficient operation are key aspects to any design.
RMI Pressure Systems has been a leading manufacturer of high-pressure, high-flow pumping systems for many years, delivering bespoke solutions to the coal, steel and oil & gas industries. A major part of its reputation is based on the reliability of its products, a key feature in applications where lost production costs can rise to stratospheric proportions.
A vital aspect to a pump’s performance is the lubrication system and so maintaining a careful watch on this provides the necessary insight to the overall pump condition. Health monitoring systems are designed around the client’s specific requirements and can be integrated into the main pump control system, if required.
Depending on the application, a range of parameters can be monitored, including the lubrication oil level, temperature and pressure, oil filter pressures and water feed pressure. These can be used to detect a drop in lubrication oil performance or an issue with the water supply to the main pump. The alarm signals generated will be able to initiate a range of actions, from a visual warning to complete pump shutdown.
By working with the client, RMI is also able to design a complete high-pressure pumping system specifically suited to the application. The designers are able to minimise the total number of pumps and associated control gear, while still meeting the required design scope, which ensures that the final costs of the installation are optimised and the ROI period is kept to a minimum.
Many high-pressure pump applications require both pressure and flow to fluctuate depending on the process. Some designs operate a bypass system where the system pressure actually increases due to the reduced flow and this can lead to increased wear in the pump as well as the pipework.
The range of Trimax industrial pumps, designed by RMI, are carefully tailored to each application. In the case of descaling plants, the pumps can be equipped with the Stored Energy Offloading System, which gives the stop-go capability required for this industry, while also reducing energy consumption.
The unloading system is a soft action solenoid control system which allows the pump to run without generating further pressure. The pump continues to idle in a pressurised standby condition so that it can quickly and efficiently return to the pressure and flow settings dictated by the grade of steel, which is passing through the descaling plant. This innovative design ensures that the energy savings are significant, with previously installed examples delivering a ROI of less than two years.
In those applications which require specialist, high-pressure pumps, there is no substitute for bespoke, precision engineering and design, which can deliver a tailored product with reliability and energy-efficiency built in. RMI has been delivering innovative and proven performance to a range of industries, each with its own exacting standards.