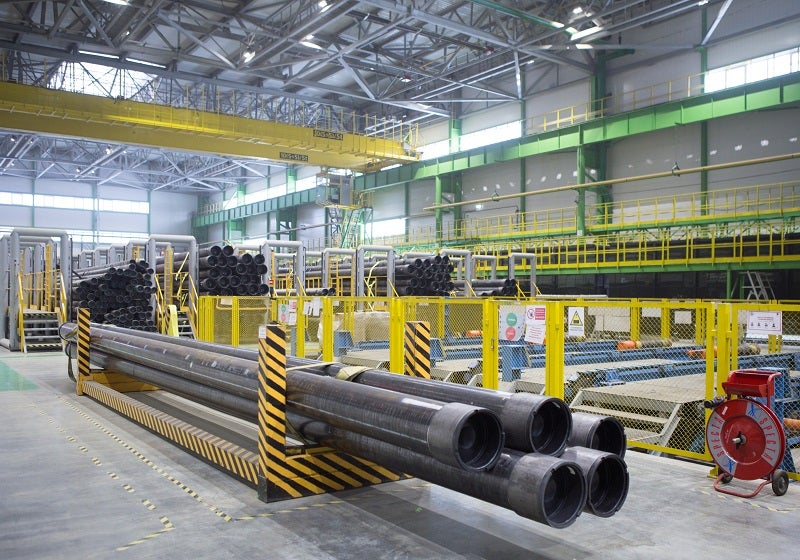
AO OMK continues pursuing its expansion programme for the small and medium-sized pipe business launched in 2016. It includes upgrades, renovations and revamps of the existing facilities and construction of new ones.
The expansion program applies to all the existing OMK facilities that manufacture electrically welded OCTG tubulars and includes improving the product offering as well as the quality of the oil and gas production pipe and commissioning facilities to make product the Company has never made before, such as oil production tubing and well workover pipes.
ERW Shop 5 Upgrades
Upgrades to ERW Shop 5 became an important project. When the shop was commissioned in 1986, it enabled Vyksa Steel Works (AO VSW) to become the only manufacturer of electrically welded casing in Russia. At this time, the mill equipment is capable of making pipe with OD between 139.7 and 244.5 mm, wall gage of up to 10.7 mm, and grades of up to J55.
Upgrades to ERW Shop 5 by replacing the 140-245 mill will help expand the product line and make pipe ranging from 114.3 to 244.5 mm with wall gages of between 4.0 and 15.9 mm and grades of up to N80 per API 5CT and up to X80 per API Spec 5L.
This project to replace the mill is remarkable insofar as the existing welding mill continues running (making the same amounts of product) while the new state-of-the-art mill is being installed alongside it.
Upgrading the threading line is a priority objective. At the present time, activities to replace the pipe and coupling threading machines, the buck-on and the tightening equipment are proceeding apace. Construction and installation work at additional inspection stations as well as protective coating equipment installation are ongoing.
The facility is developing skills for new threaded connections designed for inclined and horizontal wells:
· VMZ-1: a highly leak-proof threaded connection designed to reinforce vertical and inclined wells with an inclination rate not exceeding 3.9° per 10 m.
· VMZ-4: a gas-tight threaded connection with a lean-back support surface designed to reinforce inclined and horizontal wells with an inclination rate not exceeding 13.1° per 10 m.
· VECTOR: a threaded connection to join large-diameter casing (508 and 530 mm) designed for conductor strings with lengths of up to 200 m.
· A threaded joint designed to assemble pipes into risers when drilling with a jack-up rig, stationary off-shore rigs, conductor support systems.
All the threaded connections were developed in a collaborative effort by ANO TsNIS Truby-Neft (Samara) and AO VSW with the exception of the VMZ-4 connection which is a proprietary AO VSW technology.
The functionality of the new equipment has been improved enabling pipe thread to be cut in more than a single pass which helps manufacture a more sophisticated product as well as cut thread on pipes with a wall gage of between 6.5 and 7 mm.
The new mill’s welding stand will undergo some development testing to acquire capability for new products from promising steel grades. The design provides for capability to move the ID scarfer, the welding, and the seam guide stands.
Equipment upgrades in ERW Shop 5 will help broaden the product offering and provide a way of using the most advanced designs in the manufacture of electrically welded pipes. An automated production system will help monitor all the steps in the pipe manufacturing sequence and make product of enhanced quality.
Wider Casing Product Offering
Last year, the facility completed building a pipe finishing center designed to process improved-quality casing with ODs ranging from 139.7 to 426 mm and wall gages ranging from 6.2 to 14 mm for the oil and gas industry, including pipe of grades K55 through P110 designed for well construction with coupled connections of any type, including premium and semi-premium connections for complex drilling. The finishing centre’s design capacity is 100,000 tons of product per year.
At this time, the centre is working hard to set up production and is expected to ramp up to design capacity in the second quarter of 2019.
Low-Temperature Pipe
Production companies are becoming ever more active in the Extreme North every coming year. Complex oil and gas production environments cause pipe customers to impose additional requirements on the drilling of exploration and production wells; therefore, there is increased demand every year for low-temperature casing.
AO VSW has developed a unique chemistry for low-temperature casing with ODs ranging from 146 to 245 mm of Grade E (N80Q) (usable down to -60°C). For casing of ODs ranging from 146 to 245 mm, low-temperature properties are evidenced through KCV-60 and KCU-60 while for ODs randing from 324 to 426 mm, KCV-40 and KCU-60 are applicable.
530-mm Casing with Weld-On VECTOR Threaded Connection
Specialists with the AO VSW (an AO OMK subsidiary) Engineering and Technology Center developed 530-mm casing with a VECTOR threaded weld-on connection.
This product is assembled from components manufactured at AO OMK facilities. An original design of the threaded connection ledge created additional advantages for the customer that are required when building casing strings.
In December 2017, casing with the VECTOR threaded connection successfully completed test bench testing in a specialized lab at the OOO NIIneftetruby in Samara.
Thermal Casing
At this time, AO Trubodetal (an AO OMK Group company) has acquired the capability to manufacture thermally insulated pipe (thermal casing) that is used to protect wellheads in permafrost from thawing out. They are designed as two steel pipes of different diameters placed one inside the other and the annular space filled with an insulating compound (polyurethane or polystyrene foam). This thermally insulated casing is available in three sizes (inner/outer diameter):
· 324 / 530 mm
· 426 / 630 mm
· 530 / 820 mm
AO Trubodetal has obtained a patent for a utility model in the thermal insulation field and has already delivered the first batch of thermal casing to OOO Gazpromneft-Yamal.
This product has a lot of potential for the Extreme North and areas of permafrost (the Yamal Peninsula, North-Eastern Siberia, and the Far East).
Breaking into New Oil and Gas Markets
Vyksa Steel Works is gearing up to launch a new product: oil prodution tubing of ODs ranging from 60 to 114 mm and wall gages of between 3.0 and 12.7 mm from in-house hot-rolled coil. AO VSW has already
built ERW Shop 1 to manufacture longitudinally electrically welded tubing. The design capacity of ERW Shop 1 (with the already up and running finishing center to thread casing of ODs between 140 and 426 mm) will be 165,000 tons of tubing a year. All pipe will be manufactured to GOST 31446-2017 or API 5CT with product spec level PSL-1 using standard in-house couplings with triangular or trapezoidal thread forms (NU, NKTM, NKM). Pipe manufactured to API 5CT PSL-2 will be available upon customer request. Launch of the tubing facility will help the Company break into a new previously unserviced segment of the oil and gas market.
Once the Oil and Gas Line Pipe Business Unit expansion program at Vyksa Steel Works is complete, OMK will be able to offer oil and gas companies casing, tubing, and line pipe with improved properties and meet their most stringent quality requirements.