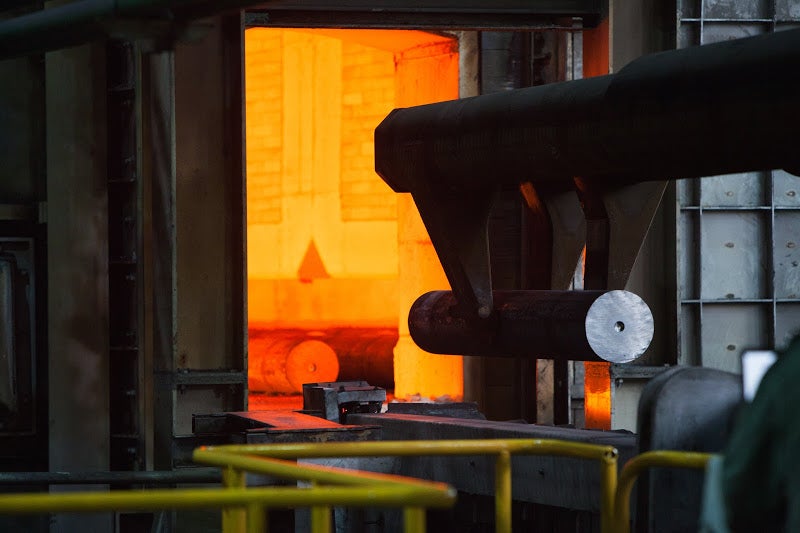
A new ring heating furnace has been commissioned at Interpipe Niko Tube. The equipment, manufactured by Germany based LoiThermprocess Company, serves to heat steel billets before rolling. The significant advantages of the new furnace include high production capacity, energy efficiency, and a reduction in metal consumption. The ring furnace is unique in Ukraine, and has received $20m in investment.
Production capacity of the new furnace will be 325,000t of billets a year, exceeding the rates of the old furnace by 50%. Additionally, the new equipment has reduced electric power consumption by one third, and reduces the consumption of natural gas for the heating of 1t of billets by 20%. The new furnace also reduces scale formation during the billet heating process by 1.5%, ensuring a reduction in the metal discharge coefficient.
All 159mm to 325mm pipe products made at the No 2 tube-rolling shop will go through the new ring furnace. Casing and line pipes produced at the shop are marketed in 20 countries around the world, including Austria, Italy, Spain, Saudi Arabia and the US.
Interpipe Niko Tube supervisory board chairman Vladimir Gornstein said: "Over the last several years, Interpipe Niko Tube has been the centre of large-scale transformations. We have invested $60m into the modernisation of our production facilities, and we have also invested money into our people, in new working clothes, personal service rooms, catering, and the training centre. The most important thing we have managed to achieve is the change in attitude of people towards their work. Our priority now is to offer a top quality competitive product to the market."
Interpipe continues to modernise its production facilities and enhance energy efficiency and labour productivity at its enterprises through its investment programme, despite the current economic climate.