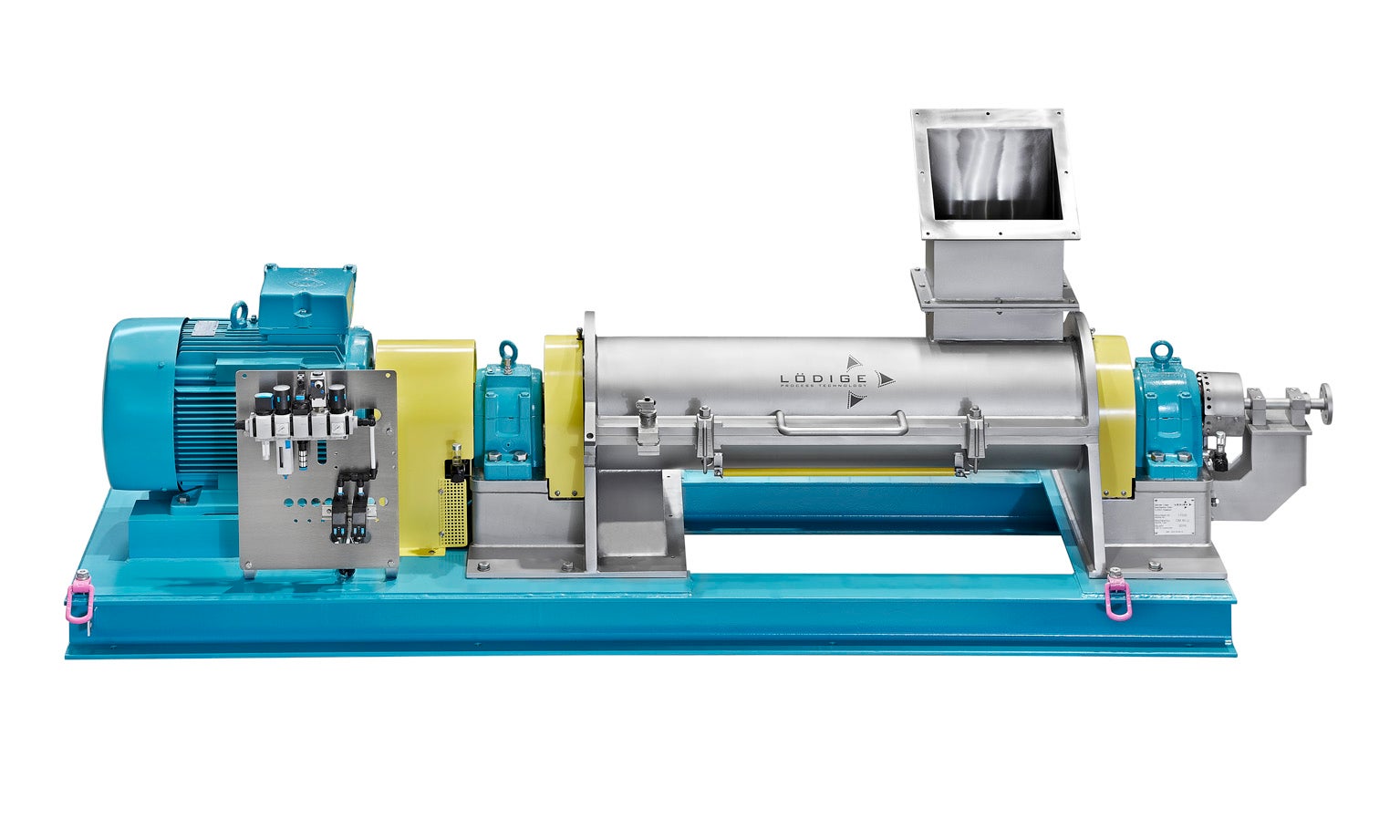
The versatile ring-layer process holds great economic potential for continuous mixing. At the same time, it places particularly high demands on the design and construction of the mixing system. The CoriMix® Ringlayer Mixer from Lödige Process Technology is an example of how high throughput rates can be achieved with a high level of mixing quality and what requirements have to be met.
The ring layer process develops its characteristic strengths wherever excellent distribution of liquids at high to very high throughput rates is required. In terms of cost-effectiveness and versatility, the use of Ringlayer Mixers is also an attractive option in numerous industries.
The basic model of such a machine is similar to that of a conventional continuous mixer with a stationary mixing drum and rotating mixing tool such as those offered by Lödige with the KM series, for example. In contrast to this, however, the mixing shaft of a ring layer system rotates at high circumferential speeds of up to 40 m/s. This accelerates the added product components centrifugally. The result is the formation of a ring layer. Within this concentric layer, there are enormous speed differences between the rapidly rotating mixing tools and the stationary mixing drum wall. This means there is a particularly high level of friction in the profile of the ring layer. The specially shaped tools of the mixing shaft move the product through the mixing chamber throughout the process in a plug flow manner. As this process is extremely quick, the residence times are very short and the residence time spectrum is narrow.
CoriMix® Ringlayer Mixer
As a pioneer of this mixing system, Lödige has bundled its many years of experience in the high-performance CoriMix® (CM) Ringlayer Mixer. Lödige offers it as a laboratory mixer and as a production mixer with a total volume of 5l to 4,000l.
Thanks to the individual, application-specific design of each machine, it is possible to implement a wide range of processes in a cost-effective manner using the CoriMix®. The spectrum ranges from mixing, moistening, compacting and granulating to dispersing, disintegrating, melting and liquefying. The CoriMix® is thus excellently suited for the production of moist mixtures and suspensions or pastes, for coating primary particles and for the production of agglomerates having small particle size and a narrow particle spectrum. The CoriMix® can easily be preceded by a continuous Ploughshare® Mixer type KM to produce a dry mix with many components and the highest level of mixing quality. Likewise, products can be post-treated in a KM to further influence the product properties after liquid addition.
Compact, powerful, durable
The versatile CoriMix® mixer type is thus suitable for numerous industrial applications, for example in the agrochemical industry, building materials industry, fine chemicals, as well as in the food or animal feed sector. A special variant for applications in the pharmaceutical sector meets all the requirements as set by the rules for Good Manufacturing Practices (GMP) applicable here.
Liquid components are fed directly into the product ring layer separately from the dry components to ensure a particularly homogeneous distribution. Liquids can be added in two ways.
With the external feed, the liquid discharge takes place via inlet pipes, which are installed in the drum wall and which project into the product layer. With the internal feed, the liquid is guided by means of a rotary joint through a hollow shaft to specially perforated tools, enabling liquid to be directly added into the product ring layer. With both feeding techniques, moistening of the shaft and the mixer wall is avoided as far as possible and product adhesion is thus prevented.
The residence time in the machine can be specifically controlled via several parameters, namely the filling level, rotation speed, geometry and mixing tool settings, as well as the mixing vessel length and volume throughput affect the product-specific process time. The system also provides the option of dividing the mixing chamber into zones with different shearing intensities. This permits ideal adaptation to varying product properties at all times.
Low space requirements, easy handling and maintenance, good cleaning options and durability were the focus during the development of the CoriMix®. The mixing vessel is divided in the middle along its entire length and can thus be opened. This means that the mixer interior can be conveniently cleaned, easily maintained and, if necessary, simply adapted to new requirements. Optional linings also allow the processing of products that tend to stick or are abrasive. Special composite materials, wear-resistant alloys and armouring provide the necessary wear protection.