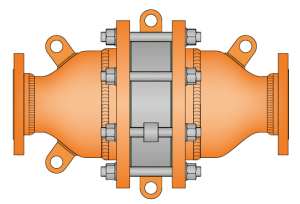
Over the past 18 months, Elmac has invested heavily in new product development and, as a result, successfully developed the enhanced flow (E-Flow™) flame arrester element technology, which is now used in the company’s EVA, EVB, EHB and ESA series of end-of-line arresters.
The development of the E-Flow element technology was achieved by drawing on the benefits of computational fluid dynamics (CFD) to model the behaviour of a system in order to investigate the flow behaviour, including the study of flow patterns and the prediction of pressure drop. This information was then used to optimise designs for the end-of-line flame arresters whilst avoiding the need for costly plant trials.
The next logical step was to take the lessons learned from the development of the end-of-line arresters and transfer the technology to in-line deflagration flame arresters. This has successfully been achieved in Elmac’s new LCA and LEA series of flame arresters.
These new products are suitable for use with gases in explosion groups IIA1 and IIA and have model variants that include:
- Operating pressures up to 1.5bar
- Operating temperatures up to 160°C
- Short-time endurance burn capability of ten minutes
- High flow, low pressure drop characteristics
- Size range of 15mm to 300mm nominal bore
- Concentric or eccentric reducers
- Material options to satisfy NORSOK requirements
In-line deflagration flame arresters are designed to prevent the propagation of pipeline explosions in their initial stages when flame velocities and associated pressures are at their lowest. As such, these units are used in venting applications and where the proximity of the flame arrester to an ignition source is relatively close.
One common application of in-line deflagration arresters is flares. The flame arresters are installed in the gas feed lines to the flare to protect the rest of the plant from potential flashback. The use of a flame arrester in this application is essential as there is always a significant risk of flash back when operating within the explosive limits of a fuel gas.
The new LCA and LEA flame arrester ranges minimise the impact of using a flame arrester on the process, meaning higher flow rates are achievable with smaller flame arresters. Not to mention the fact that E-Flow in-line arresters are smaller, lighter and easier to maintain with significantly reduced fouling in the element.
Elmac Technologies operations director Peter Evans said: "It has been a very exciting couple of years here for the new product development team. With the resources we have committed to implementing new methods of product design, and with the dedication and expertise of our technical team, to have produced six new arrester series in such a short space of time is most rewarding.
"We are continuing our drive to improve existing product ranges and to further develop and exploit our E-Flow technology. The next challenge for us is to utilise E-Flow in unstable detonation arresters and we are already in the post-prototype testing phase of that product development."
Elmac can assist clients by specifying appropriate products for proposed new installations and plant retrofits. In addition, Elmac is able to provide advice on the positioning of these products in an installation and to evaluate the suitability of flame arresters already fitted.
All of Elmac’s products are manufactured in the UK, and supplied in accordance with the latest internationally recognised standards, giving its customers the peace of mind that comes from knowing you are not compromising on safety.