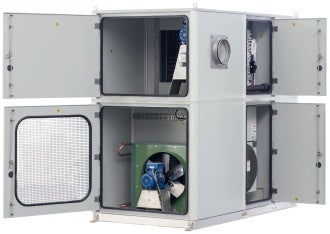
Intertec has developed an innovative all-in-one climate control and personnel safety solution in the form of its new ATEX-compliant HVAC system for walk-in style process analytical instrumentation shelters.
It is customisable and scaleable to suit a broad range of applications, and can be supplied fully integrated within the shelter or as an external standalone unit.
Designed specifically for hazardous area applications up to Zone 1, the system delivers a steady flow of conditioned and filtered clean air to the shelter, maintaining it slightly above atmospheric pressure to prevent the ingress of dust or gas. It is suitable for oil / gas refineries, petrochemical and chemical plants that operate in extremely hot or cold climates, or where atmospheric contaminants pose safety, health or corrosion issues with conventional through-flow air-conditioning systems.
To help ensure measurement accuracy, sensitive equipment such as process analysers and sample conditioning systems needs to be maintained at a constant temperature. The equipment is often located as close to the process as possible. These factors can involve housing operating personnel and equipment in a potentially hazardous area of the plant, demanding that adequate safety precautions are taken.
The prime requirement is that the shelter and any associated equipment such as air-conditioners must be explosion-proof.
Intertec’s new HVAC system is unique in that its entire housing is constructed from the company’s proprietary glass reinforced polyester (GRP) triple-layer composite material. This comprises inner and outer layers of GRP enclosing a thermally insulating core; the wall thickness and core properties can be varied to suit the application and operating environment.
The GRP is the same electrically conductive variant that Intertec uses for its explosion-proof analyser shelters. It fully complies with the anti-static requirements of the DIN/EN/IEC 60079-0 safety standards for equipment intended for use in explosive atmospheres.
As a construction material for equipment shelters, composite GRP has enormous advantages over metal, it is impervious to corrosion from most commonly encountered atmospheric contaminants and is an excellent thermal insulator. It has a similar strength to stainless steel, but is about 75% lighter, making transport, site preparation and installation easier and less expensive.
Intertec’s new HVAC system is that it can be fully integrated within the analyser shelter, or installed as a standalone unit against its external wall. Internal installation saves space and cost, reduces energy consumption by eliminating the thermally inefficient air duct of conventional standalone units, and facilitates configurations that are simply not possible with external systems. The system is fully scaleable.
The first systems that Intertec is building are designed primarily for ventilation and cooling purposes, to maintain analyser shelters located in a relatively warm climate at a constant temperature 24/7, by compensating for differences between daytime and night-time temperatures, and for seasonal variations throughout the year. They provide an 8kW cooling capacity and a 5kW heating capacity, and accommodate an ambient (external) temperature range.
A variety of fully integrated heating options is available, including an explosion-proof electrical heater and a temperature-controlled condensate vapour heat exchanger. Dehumidification is accomplished by refrigeration.
All non-explosion-proof switches and control devices in the HVAC system are contained within flameproof (Ex d) protective housings, and all electrical junction boxes are enhanced safety (Ex e) types. Every internal electrical circuit carries an IP65 protection rating. The unit comprises a powerful hermetically sealed compressor, an air cooled condenser with an axial fan, and a refrigerant collector. The refrigerant is CFC-free non-flammable R134a. The system has a low acoustic noise level and is fitted with an automatic maintenance-free condensate drain as standard.
The air supply for the HVAC system can be derived locally, the input port is fitted with a high-efficiency particulate filter. Alternatively, if the shelter is sited in a hazardous area, the air can be ducted in from a fan and filter unit located outside the immediate area, via a stack. Spent air, together with transported heat from the shelter and waste heat from the compressor unit, is exhausted direct to atmosphere.
The HVAC system is automatic. The flow rate of ventilating air depends on the application. The standards for explosion protection of pressurised process analyser shelters, such as IEC/EN 61285 and NFPA 496, mandate various air exchange rates to ensure adequate dilution of explosive or poisonous gas leaking from equipment inside the shelter, ranging from 5 to 12 complete air exchanges per hour.
The system’s main axial fan is monitored by a differential pressure switch, to ensure that the air inside the shelter is constantly maintained at a slightly higher pressure than atmospheric, automatically compensating for any sudden increase in air leakage when the entry door is opened. Any over-pressure conditions are adjusted by a poppet valve. The air temperature inside the shelter is controlled by a capillary tube room thermostat with its remote sensing bulb located in the system’s air output duct for accuracy.