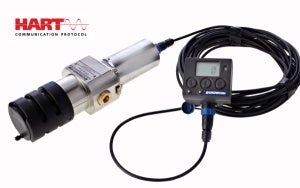
Easy and reliable connection and communication is vital when using a gas detector, which is why Crowcon has introduced the HART communication protocol for its IRmax infrared (IR) hydrocarbon detector.
The HART (highway addressable remote transducer) communication protocol is the global standard for sending and receiving digital information across analog wires between smart devices and control or monitoring systems. More specifically, it is a bi-directional communication protocol that provides data access between intelligent field instruments like gas detectors and host systems. A host can be any software application, from a technician’s hand-held device or laptop to a plant’s process control, asset management or safety system using any control platform.
The HART communication protocol is available with the IRmax in two formats:
1. Local hand-held communicator connection. In this format, HART communicators are used on industrial sites for maintaining and calibrating a host of instruments. The key benefit is that site maintenance staff can use a common communicator to maintain all of their safety and process instruments. The user simply needs to upload and install the DD (device description) file to their communicator to access a wide range of IRmax functions and displays, alarm thresholds and diagnostic information.
2. HART over a 4-20mA signal line. In this format, the safety function is performed by the 4-20mA signal (connected to a conventional controller or PLC/DCS). A HART device can then also be connected in parallel with the signal connections to read the detector’s status information.
Featuring dual-wavelength IR sensor technology in a rugged 316 stainless-steel package, the ultra-compact IRmax is designed to detect methane gas and other potentially explosive hydrocarbons in the harshest conditions.
As the IRmax contains no components for artificially heating optical surfaces, power consumption is dramatically reduced. It requires less than 1W of power, typically 75%-90% lower than conventional IR gas detectors. A gas detection system using IRmax detectors therefore requires smaller (and lower cost) power supplies and battery back-up systems. Longer cables can also be used and more detectors can be powered on addressable networks.
Unlike conventional IR gas detectors, the IRmax does not utilise heaters to prevent condensation on windows and mirrors. Instead, its optical components are treated with a highly durable hydrophobic coating called STAY-CLIR that completely prevents signal faults due to condensation.