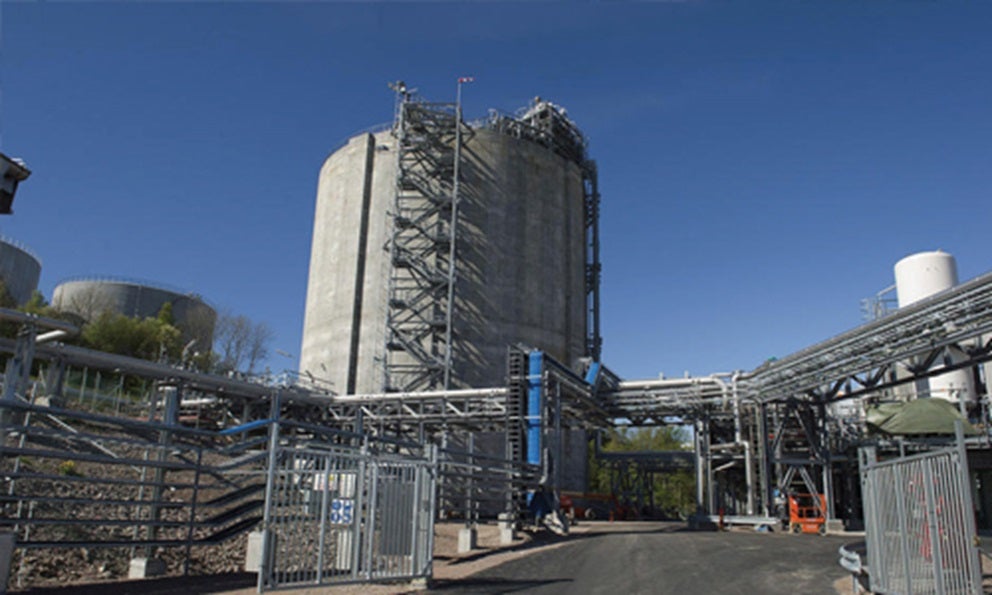
Skangas AS, owned by Finnish company Gasum and Norwegian Lyse, builds and operates medium-sized, low-carbon emission energy plants. One of their plants is the Lysekil LNG receiving terminal. The construction of this terminal helped make natural gas available for land-based industries and the marine market in South-West Sweden.
The Owner and EPCM contractor’s “AGA” major mission was to construct a safe and environmentally sound terminal to protect all personnel and equipment involved in day-to-day operations.
A logical choice for the plant’s insulation material for cryogenic and above ambient hot piping applications was FOAMGLAS® insulation. Its moisture is impermeable making it an ideal choice for cryogenic applications. It helps ensure constant thermal efficiency and helps limit corrosion under insulation. In addition, FOAMGLAS® insulation is a non-combustible and non-absorbent material that does not produce toxic emissions in a fire, making it an excellent choice for passive fire protection.
All piping and equipment with operating temperatures down to -162°C (-260°F) were insulated with FOAMGLAS® insulation. Cryogenic classes were installed in two-layer systems. The first layer was applied “dry” with an inside anti-abrasive coating. The second layer’s joints were staggered and sealed with PITTSEAL® 444N. This second layer was factory coated with an Alu-butyl foil as a final vapour barrier. This helps protect the system in challenging process temperatures.
The whole system, including insulation material, serves as a vapour barrier and helps reduce the risk of failures, such as ice formation over time. The larger dimensions and parts for the vessels were partly factory assembled to help reduce on-site installation time. All process pipes and equipment were covered with stainless steel cladding. The total length of piping that was insulated was approximately 6,000 meters (6,561 yards).
The LNG storage tank consists of a 45m (147ft) high cold box and an inner steel tank measuring 38m (124ft) in height and 35m (114ft) in diameter and has an LNG volume of 30,000 m3 (1,060,000 ft³).
The tank sits on multiple layers of FOAMGLAS High Load Bearing (HLB) 800 and HLB 1600 insulation with respective compressive strengths of 80t/m² (116psi) and 160t/m² (232psi). PITTCOURSE™ 100 bitumen sheets were installed between each layer of FOAMGLAS® insulation as a compression inter-levelling system.
A final layer of sand was applied to compensate for irregularities in the base surface and to absorb possible creeping of the steel tank base.