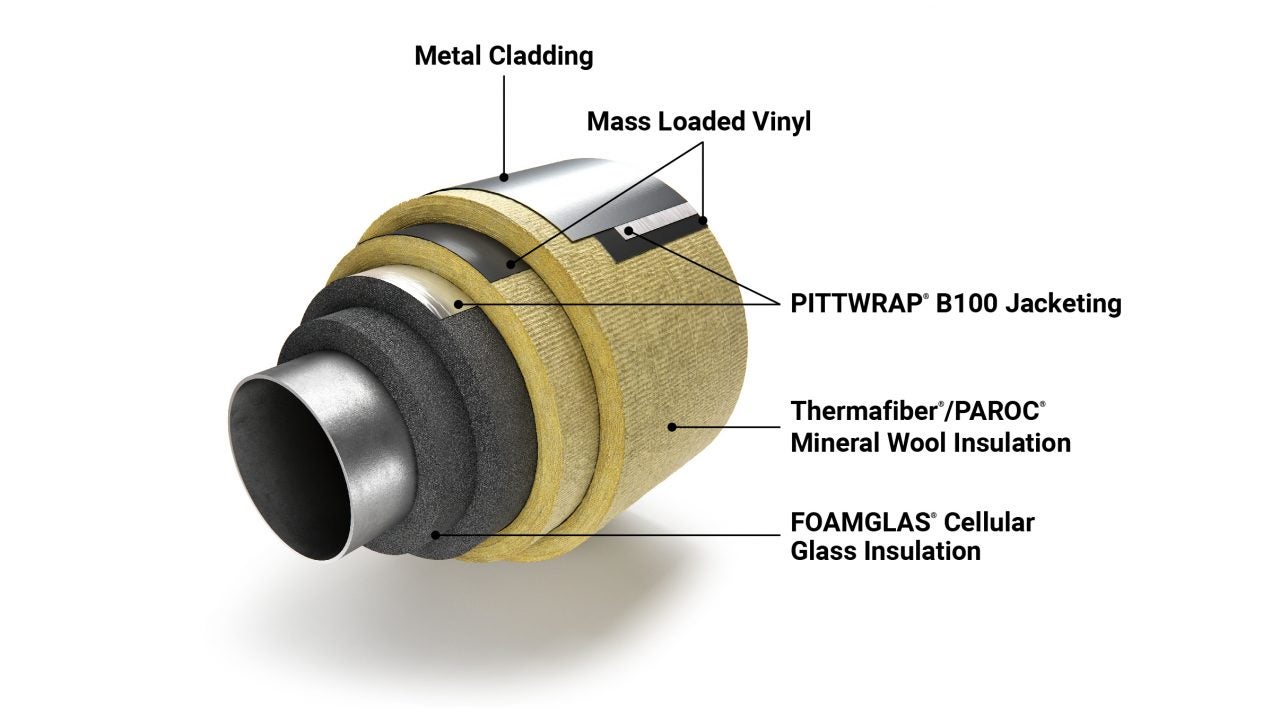
Industrial processes are often noisy as the operations and installations to process and produce (petro)chemicals often include high pressure and high-temperature equipment. This can generate excessive noise, which could be hazardous to workers and the environment.
Owens Corning has multiple acoustic insulation systems available that can help you with the mitigation of excessive noise attenuation from processing piping and equipment.
What is sound and noise pollution?
Sound is a mechanical vibration that manifests as an acoustic wave through a medium and which is perceived by the human ear in the frequency range of 16 Hz to 16,000 Hz. A frequency can be defined as the number of vibrations per second. The pitch rises as frequency increases.
Noise is a sound that is perceived as loud, unwanted or unpleasant and that causes disturbance and at certain levels and durations of exposure it can even have deleterious effects on human health and environmental quality.
Not all sound is considered noise pollution. The World Health Organization (WHO) defines noise above 65 decibels (dB) as noise pollution (WHO – Environmental Noise Guidelines, 2018). To be precise, noise becomes harmful when it exceeds 75 decibels (dB) and is painful above 120 dB. Exposure to noise pollution can negatively impact health and behaviour for both humans and wildlife present in the environment.
Why should you care about industrial acoustics?
Industrial processes are often very noisy as the operations and equipment to process and produce (petro)chemicals often include high pressure and high-temperature pumps, compressors, blowers, agitators and coolers. This is often increased when gases and fluids operate under high pressure or velocity. These excessive noise levels are a risk to employee their health as noise-induced hearing loss is one of the most common occupational injuries in (petro)chemical processing environments. Oftentimes these have limited barriers in place to restrict equipment noise from carrying beyond the confines of the installations.
More stringent health, safety and environmental regulations have led to an increase in importance when considering noise control around industrial processes. The aim of these regulations is to ensure that workers’ hearing is protected by preventing exposure to high levels of noise, which could cause long-term hearing damage. (work environments often easily go over the 85 dB limit requiring workers to wear hearing protection) From a zoning point of view, these regulations have been put in place to keep industrial facilities’ property sound levels below the required noise levels.
A preferred way of improving noise protection is adding sound control to the piping and equipment during installation to keep the sound levels below the required limit when the equipment is operating again. Not installing the correct acoustic protection can potentially result in expensive remedial costs and\or prohibit the use of certain equipment because of a non-compliance with HSE regulations.
Insertion loss and the ISO 15665 test method
Much like sound transmission loss, insertion loss measures the amount of sound and insulation blocks as it travels through the insulation system. Insertion loss is the difference in sound power between an uninsulated pipe and an insulated pipe.
The test method used to test insertion loss is ISO 15665:2003 Acoustics – Acoustic insulation for pipes, valves and flanges.
The ISO 15665 standard was designed to enable engineers to specify the correct insulation type and thickness to achieve a specific noise level reduction. The standard is classified in three classes of acoustic insulation that are denoted A, B and C, in terms of requirements for minimum insertion loss. An addition to this requirement is system “D” created by one of the world’s largest oil and natural gas producers.
Acoustical solutions for cold & cryogenic applications
Noise mitigation starts with the right choice of equipment, material and well-planned layout. Using a proper acoustic insulation system to limit the emitted sound levels at the operating equipment and connecting pipework has shown to be one of the most effective methods to protect the workforce against excessive noise attenuation from process lines.
Excessive noise is often generated at LNG facilities by equipment that is being used during liquefication, regasification or even just during loading/unloading. Acoustical insulation systems are therefore often specified for the reduction of noise. For LNG or ethylene projects, insertion loss per class C and class D are typically needed.
Owens Corning has developed a new acoustic insulation system for cryogenic applications that benefits from the cryogenic properties of cellular glass insulation in combination with the acoustic properties of mineral wool.
The system is constructed of a traditional FOAMGLAS® insulation system designed for cryogenic thermal insulation performance and then overfit with a mineral wool system designed and tested for class C or D compliance.
By designing and testing for ISO 15665 compliance of the composite cellular glass + mineral wool system, class C or D can be achieved using less additional material which can help to reduce system weight, necessary labour, and installed costs.
Potential savings and other benefits
- Lower material cost
By using a combined FOAMGLAS® cellular glass insulation system in combination with mineral wool, you will be able to reduce the material thickness of the top layer needed to achieve class compliance.
- Lower labor cost
Because the top layer can be reduced in thickness you can also reduce the cladding thickness and reduce the mass layer making the total system easier to handle and to install. This will in turn lead to quicker installations and thus eventually lower labor costs.
- Less weight on pipe
By being able to use a lower mineral wool density in combination with reduced cladding thickness and a reduction in the mass layer, the total weight on the pipe will be lower.