Predictive maintenance tools evaluate the condition of operational equipment. They predict its maintenance requirements in order to achieve optimum performance and prevent malfunction. It uses automated condition monitoring and advanced data analytics to gather vital equipment statistics. These include vibration, temperature, sound, and electric current. It then compares them with historical records of similar equipment to detect signs of deterioration.
Listed below are the leading upstream companies that are adopting predictive maintenance technologies in the oil and gas industry, as identified by GlobalData.
How well do you really know your competitors?
Access the most comprehensive Company Profiles on the market, powered by GlobalData. Save hours of research. Gain competitive edge.
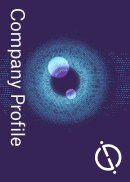
Thank you!
Your download email will arrive shortly
Not ready to buy yet? Download a free sample
We are confident about the unique quality of our Company Profiles. However, we want you to make the most beneficial decision for your business, so we offer a free sample that you can download by submitting the below form
By GlobalDataRoyal Dutch Shell
Shell has been a leading player in the development of innovative technologies to maximise production and minimise risks. The company is at the forefront in adopting predictive maintenance technologies. These enhance equipment reliability and extend the overall operational life of its assets. Shell’s use of AI and machine learning in predictive maintenance is helping the company in lowering operational expenses while also helping in lowering environmental risks arising due to equipment breakdown.
ExxonMobil
ExxonMobil has a diverse portfolio of upstream, midstream, and downstream assets. Its large customer base makes it imperative for the company to use predictive maintenance to ensure smooth operations at all plants. Exxon has installed sensors at several facilities to capture data regarding equipment condition. It then analyses it for optimal performance and detecting potential failures.
The company is gradually transitioning its approach towards data management. Moving from storing data on premises to storing data over the cloud. This will enable them to enhance data analytics capabilities and obtain real-time insights on equipment condition. Exxon recently entered into a collaboration with Microsoft to use Microsoft Azure cloud computing platform and its data analytics tools to deploy predictive maintenance technologies at Exxon’s Permian shale assets.
BP
BP is a leading adopter of digital technologies across its global oil and gas operations. The company has vast experience in collaborating with technology companies. These are for developing and deploying digital technologies to maximise productivity. BP has deployed predictive maintenance technologies at its upstream operations around the world, garnering higher equipment uptime along the way.
Chevron
Chevron relies on digital technologies to optimise drilling and completion operations. Also to improve oil recovery, and increase plant reliability in downstream facilities. The company uses latest technologies to assess the performance of its equipment. It runs diagnostics on them to identify faults that could lead to a breakdown. Chevron’s long-standing relationship with Emerson and Microsoft enables the company to capture sensor data on the cloud. They can then perform advanced analytics to predict maintenance requirements. Chevron has adopted the cloud-based data analytics approach for predictive equipment failure in its refinery operations.
Rosneft
In the last few years, Rosneft has dedicated its resources to modernising its infrastructure with the use of latest technologies. This is to overcome the downward production trajectory from maturing oilfields in Russia. The company’s foray into less-explored and unchartered territories in the Arctic and the Far East regions has added a financial risk besides presenting with technical challenges. In the midst of increasing project complexities, Rosneft is investing in predictive maintenance and other digital technologies to boost growth and sustainability.
Since 2013, Rosneft is collaborating with GE to develop and implement IoT solutions for Rosneft’s LNG liquefaction units, and refineries and petrochemical plants. The two companies are also involved in the development of artificial lift technologies and technologies for undertaking offshore and subsea E&P operations.
Equinor
In the last few years, Equinor is giving greater impetus for digitalisation of its upstream operations. This is to lower operational costs and reduce carbon footprint. In 2018, Equinor established an integrated operations support centre at its facility in Bergen, Norway. This provides remote monitoring and diagnostics capabilities for the company’s oil and gas assets in the continental shelf.
The company also opened a similar support centre in the US, focusing on its operations in North America. These onshore support centres are expected to further enhance the capabilities of Equinor’s existing condition monitoring centres with improved collaboration to the speed-up decision-making process.
Repsol
Repsol is rapidly embracing digital transformation to enhance productivity, particularly in areas related to equipment health and undertaking maintenance activities. The company has witnessed around 15% decline in corrective maintenance activities, giving a considerable fillip to overall operations. Repsol is also harnessing the capabilities of machine learning and artificial intelligence to perfect its predictive maintenance solutions. The company estimates to achieve around $200m in annual savings in operational expenses. Adopting analytics for improving predictive maintenance and logistics optimisations by 2020 will help.
Total France AI-driven predictive maintenance has become a mainstay of Total’s global operations. The company is using this expertise to deploy predictive maintenance and other digital technologies on the cloud. Total has entered a collaboration with Google Cloud to develop and deploy AI-driven solutions for the analysis of geophysical data, besides delivering equipment monitoring capabilities.
ConocoPhillips
ConocoPhillips has extensively deployed predictive maintenance technologies across its assets. This helps to optimize maintenance operations and reduce breakdowns and costs. The company makes use of state-of-the-art technologies, including drones and data analytics to inspect equipment and infrastructure and schedule maintenance activities. ConocoPhillips has also begun transforming maintenance programmes in its downstream business unit before the unit was spun-off as a separate company
This is an edited extract from the Predictive Maintenance in Oil & Gas report produced by GlobalData Thematic Research.
Related Company Profiles
Emerson AS
Equinor BV
Repsol SA
Exxon Mobil Corp
ConocoPhillips