Predictive maintenance has been widely deployed in the oil and gas industry over the last 20 years. Volatile oil price environment is resulting in the increased adoption of predictive maintenance technologies as these help companies cut operational expenditure by optimising maintenance scheduling and driving productivity.
Listed below are the key trends of predictive maintenance in the oil and gas industry, as identified by GlobalData.
How well do you really know your competitors?
Access the most comprehensive Company Profiles on the market, powered by GlobalData. Save hours of research. Gain competitive edge.
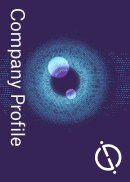
Thank you!
Your download email will arrive shortly
Not ready to buy yet? Download a free sample
We are confident about the unique quality of our Company Profiles. However, we want you to make the most beneficial decision for your business, so we offer a free sample that you can download by submitting the below form
By GlobalDataCost pressure
The oil and gas industry is just recovering from a major downturn that caused significant operating losses for the stakeholders. This lead to indefinite delays in planned projects bankruptcies and job losses. One of the important lessons derived from this downturn was that companies who excelled in managing operational expenditures had better chances of survival.
Traditionally, maintenance has been a recurring activity for the oil and gas industry aiding in asset productivity and profitability. However, periodic inspection and maintenance of assets are very costly. Additionally it still may not be fool-proof in avoiding unplanned equipment breakdowns. Adoption of predictive maintenance can help in early detection of faults in equipment, thus minimising unplanned downtimes. It can also reduce the need to carry out scheduled maintenance activities periodically, thereby lowering the associated operational expenses.
Oil and gas companies were familiar with condition monitoring and predictive maintenance even before the slump, deploying them in many of their projects. However, the deployments were more in the case of new projects or as a part of asset modernisation exercises. The oil price slump prompted companies to consider adopting predictive maintenance to improve operational efficiency and reduce equipment downtime.
Streamlining maintenance activities
Maintenance approaches in the oil and gas industry have transitioned from reactive to preventative and are now edging towards a proactive approach. The preventive maintenance approach that required inspection and maintenance at regular intervals was effective. However, it failed to completely eliminate machinery breakdown . Additionally, this approach required inspecting all equipment periodically, leading to redundancies in this approach. Also, it is very time consuming to determine the exact interval for conducting maintenance activities.
Predictive maintenance technologies help in adopting a proactive approach. They do this by identifying equipment that requires maintenance or servicing. It can also accurately diagnose the exact nature of a problem and suggest a possible solution to it. It thus enables maintenance personnel to selectively plan and undertake repairs. This reduces the overall effort required in conducting maintenance procedures. Predictive maintenance also contributes towards efficient management of machinery essentials, such as fluids, components, and other accessories.
Ageing infrastructure
Equipment and infrastructure presently in use for oil and gas operations was constructed several decades ago. It was based on designs, materials, and technologies available at that particular time. In some instances, these ageing assets have surpassed their predetermined life expectancy envisioned during the design phase. Such ageing equipment is bound to fail and therefore requires constant inspection and monitoring. Installing sensors on ageing equipment can also avert potential accidents and minimise risks to the workforce and the environment.
However, implementing predictive maintenance in older equipment requires incorporating sensors and cabling to capture data. In contrast, most new equipment come pre-equipped with sensors. These monitor telemetry and other vital statistics that can be directly fed to a predictive analytics system.
Shortage of skilled workforce
Some predictive maintenance technologies have been in existence for a while, and oil and gas companies have implemented them in a variety of environments. However, in the last few years, there has been a rise in adoption of predictive maintenance technologies within the industry to ensure all the field equipment are functioning at their optimum levels.
However, the availability of a trained workforce necessary for analysing sensor data may prove to be inadequate, considering the growing demand for predictive maintenance services worldwide. Evaluating data generated from vibration sensors, thermographic equipment, and other devices requires in-depth domain knowledge and expertise, which requires years of training and field experience.
This is an edited extract from the Predictive Maintenance in Oil & Gas report produced by GlobalData Thematic Research.