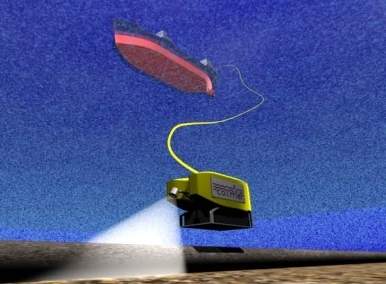
Co.L.Mar’s DNV GL–certified Acoustic Leak Detector® (ALD) is an innovative solution designed to accurately and efficiently detect leaks in a wide variety of marine environments.
The technology was first introduced and patented in 1998, and since that date the equipment has been subject to continuous development up to the current performances.
Thanks to the experiences made on the field in these years, we have optimised our service and collected data and knowledge from the most different leak situations: buried pipe, gas leak, oil leak, deep water, pipe in pipe, flanges, wellhead etc.
We have added functions, new developed sensors and inspection techniques with the scope of supplying the most efficient service in any subsea scenario.
Up to January 2018, ALD has detected 54 leaks on subsea installation with a rate of success of 100%.
Principles of operation
A pipeline leakage consists in the transition of a fluid from the inside pressure to the lower external pressure.
This creates an acoustic signal due to the turbulence and to the sudden expansion of the fluid mass.
ALD is capable to extract this leakage signal from the ambient noise, reaching and extremely high sensitivity.
The system
ALD technology is covered by an international patent. The system is mainly composed by a set of underwater sensor units, a transmission line, and a surface receiving and processing station.
The acoustic signal acquired, pre-processed and digitalised by the underwater sensor is then processed by the ALD receiver and by the ALD software.
Data is processed and displayed in real-time by our proprietary ALD software. The sophistication of the processing algorithms is one of the keys to reach a very-high sensitivity.
The system is fully digital and a series of optional sensors can be added: hydrocarbon, methane, crude oil, fluorescine detector.
For each inspection, the ALD configuration and survey technique will be selected on the base of client requirements.
ALD operational modes
On the base of the characteristics of each project (depth, pipeline length, differential pressure) and the availability of means in site (ROV, DP vessel), one or more of the survey techniques can be selected:
- ROV installation: the sensor is installed on the vehicle and connected to the receiver through the ROV umbilical. Compatible with any ROV, depth up to 3,500m
- Towfish: the sensor is a towed body. The transmission line is the towing line. Requirements: small vessel (no DP required), max depth 250m. Survey speed up to 6k
- Vertical deployment: the sensor is fixed to a clump weight, lowered above the pipeline while the S/V moves along. Requirements: DP vessel. Depth up to 200m
- Diver: the sensor is handheld by the diver and connected to the surface through a dedicated umbilical. Ideal for flanges, valves and skids
- Pole-mounted: for very shallow water, the sensor is pole mounted and driven along the pipeline track
- AUV installation: automatic monitoring and inspection of subsea installations. Can be integrated into any AUV
Please download the ALD product brochure below for more information.