
The oil and gas sector is not always thought of as a fast adopter of cutting-edge technology. Yet innovation has been vital to the industry’s success; it has facilitated growth in new, previously inaccessible areas, such as deepwater wells, and shored up the sector’s ability to weather economically challenging times, such as the 2014 oil price plunge, by providing efficiency and cost savings.
The ITF has been facilitating joint industry partnerships to foster innovation for nearly two decades, and although it lost members in the wake of the downturn, its support base remains strong. In 2015, it celebrated 15 years of continued membership with six operator members – Total, Shell, Chevron, BP, BG and ConocoPhillips – and in September, Premier Oil committed to extending its membership for another three years.
How well do you really know your competitors?
Access the most comprehensive Company Profiles on the market, powered by GlobalData. Save hours of research. Gain competitive edge.
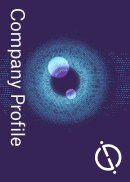
Thank you!
Your download email will arrive shortly
Not ready to buy yet? Download a free sample
We are confident about the unique quality of our Company Profiles. However, we want you to make the most beneficial decision for your business, so we offer a free sample that you can download by submitting the below form
By GlobalDataAs the 2017 open call shows, any company or developer can contribute ideas to help future operators work in more challenging environments, and improve decommissioning.
Heidi Vella (HV): How important is technology innovation to the oil and gas sector, especially over the last decade?
Ben Foreman (BF): It is very important and there are two areas where technology has had a big impact. First, there are technologies called enablers that allow us to do new things, for example, to drill deepwater wells and find new oil and gas reservoirs.
Secondly, there is technology for continuous improvement that allows industry to do things better – such as increase oil recovery rates, lower operational costs, increase safety and reduce environmental impact.
There are two ways the industry achieves the second point. Firstly, it looks at processes which can reduce cost, examining the methodology. Companies look to target this first because it is low cost and low risk as it only involves examining what they are already doing and looking at how they can do it better – but it can only take you so far. The other way is to implement new technologies.
HV: How does ITF get JIP’s off the ground?
BF: All our members have their own R&D teams, but there are many areas where they want to work collaboratively. Typically, our members state what their technology challenges are – for example, subsea tie-backs to produce remote fields from any infrastructure or facility or subsurface and the understanding of rocks and producing reservoirs.
Furthermore, there are two sides to the ITF business – the operators and service companies who tell us what they want us to do, and the other is our network of 2-3000 developers, comprising of single person companies, partnerships, academic bodies, and research institutes.
We outline the challenges and inform the developers who send ‘expressions of interest’ detailing what they are working on. ITF’s role is as a facilitator is to get the two parties together to discuss the cost, timeframe and end goals etc. When ready we launch a JIP but the technology ownership always stays with the developer.
HV: So far, what do you consider to be ITF’s greatest achievements in terms of game-changing technology?
BF: Since its inception there has been around 220 JIPs launched and facilitated. You can argue, for each of these projects, there was a key business case and benefit to the industry.
But there are two standout projects. One is from a Dutch company called Airborne Oil and Gas which made a thermoplastic composite pipe. Airborne came to ITF with an idea, and ITF secured over a million in funding from seven different operators for feasibility and testing.
The strength of the JIP, with so many operators invested, showed there was a market for this project and so the company won venture capital funding. The extra investment expedited product development so the product came to market much quicker and is now a commercial product.
The reason the industry wanted this product is because operators typically use steel and metal for pipelines which can corrode with high costs for repairs, furthermore many processes fluids used in the industry react poorly with steel pipelines. This composite plastic pipeline, however, offers a solution to high corrosion areas.
The second is the ‘Fullwave Gamechanger’ work with Imperial College London. The ‘Fullwave Gamechanger’ seismic technology project has influenced 100 well placement decisions with operators realising $500 million in value from that single project alone.
HV: Are members interested in developing technologies using AI and machine learning?
BF: AI is definitely key. A lot of other industries have been more forward-thinking and quicker to uptake AI.
This year, ITF has done work in data analytics to see how we can use recorded data and analytics to improve production optimisation, facility uptime and prolong life to maximise hydrocarbons recovered. Next year we are going to look at work around machine learning targeted at subsurface machines using software to help interpret hydrocarbons, as well as identify rocks and formations in different areas. There is the ability to integrate many parts of the industry – geology, geophysics, geo-mechanics [and] sedimentology.
HV: Is it inevitable that continued technology development will see a reduction in personnel?
BP: Personally, I don’t think so. I think the introduction of new technology will reduce the number of people we have in dangerous situations, but we still need people to monitor this new technology. Many rigs now are fully connected to onshore, so you have some guys offshore and, in many cases, as many people onshore watching what they are doing.
HV: What other areas of technology development will be important in the future?
BF: It depends on where in the world you operate. In the UK, for example, there are many small fields where there are limited hydrocarbons in the reservoir and it is not commercial to invest in a full set of facilities, so these wells don’t get developed. We want to find solutions to make it possible to develop them.
In the UK, because it is a mature basin, decommissioning is building momentum, whereas in Australia and Africa, technologies for drilling in deeper waters and more remote areas are needed.
We are also focusing heavily on subsea tiebacks, which means being able to do everything on the seabed and then transport the hydrocarbons to a centralised process facility or, in the future, straight back to shore.
We are starting to work on reducing the costs associated with aging infrastructure which is key from a UK perspective due to the tax regime and public money spent on supporting decommissioning. We also liaise with companies in the Gulf of Mexico, Brazil and Australia that have similar issues.
Furthermore, we have also just started work on exploiting low permeability reservoirs to discover how to maximise production from wells that might not typically produce hydrocarbons at a commercial rate. We are looking to find an alternative to high pressure fracturing of rocks and to reduce the dangers associated with it.
When oil prices are depressed we see a reduction in drilling, so the industry looks to produce more from what it has – and that is one of the key drivers moving forward.