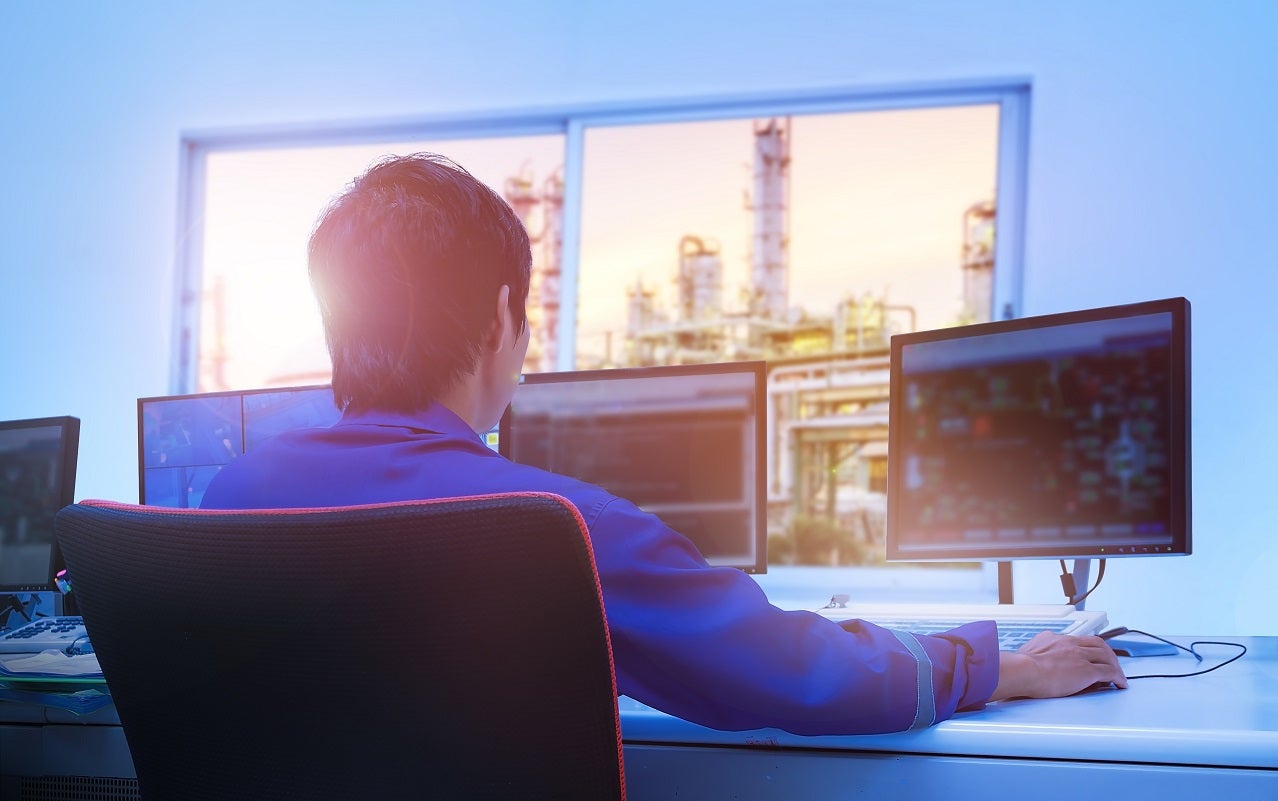
With greenfield investments less likely these days, industry leaders must address current market-driven efficiency, cost control and profitability challenges by bridging the information gaps in brownfield operations.
Here are five key areas companies focus on to achieve operational excellence in brownfield projects:
1) Centralise current asset documentation and data.
Unlike greenfield sites, critical facility information in existing brownfield operations may still be captured on paper, spreadsheets, word processor document and stored across scattered filing cabinets and computer networks. This information should be captured digitally and, more importantly, organized in a centralised environment, to support critical operational processes. This, in turn, will help speed up access to reliable information in executing critical functions like completion of inspections.
2) Connect engineering documents and operations processes with maintenance data.
Siloed information that exists in different formats and on different systems is not only detrimental to the operations of a facility, it can also increase operational risk at hazardous process and manufacturing industry facilities! Companies should ensure that all necessary documents are well integrated with the business processes and systems that support them. Access to the latest information must always be readily available to the right people at the right time and connected in a way, so the required documentation – design basis, inspection records etc. – can be retrieved by searching for what you know – for e.g. Asset Number, Equipment Type or Functional Location
3) Design and implement an effective change management process.
Even at plants that are several decades old, change is a constant. Sustaining Engineering projects in a brownfield facility occur in parallel with other projects concerning the same plant, equipment or process. Therefore, it is not enough to establish a baseline of information. Successful organizations must ensure that they are able to cope with changing information, both managing the change process and ensuring that the most current “as operated” documents and data are always available, with an identification of those that are under change.
4) Include relevant third-party partners in change processes.
Brownfield projects tend to have a large and geographically diverse scope of contractors and suppliers. Therefore, it’s crucial that your processes and systems allow third-party partner organizations to share documents, updates, and participate in review and approval workflows. This can only be achieved efficiently and securely, through centralised ecosystem of connected systems or the “Digital Twin” of your facility.
5) Ensure the same tools and processes are applied for both large-scale capital projects and brownfield projects. This will allow your organization to follow industry best practices and your company’s standardised work processes and operating guidelines and help keep all projects on track.
By encouraging executive teams to adopt a consistent approach that prioritizes these five areas, companies will not only increase efficiency but adapt to today’s pandemic-era changes. More importantly, it will set them ahead of the competition, and poised for action in the next normal.
Download our whitepaper by clicking on our logo above to find out how you can bridge the information gap in brownfield assets and save on OPEX costs.