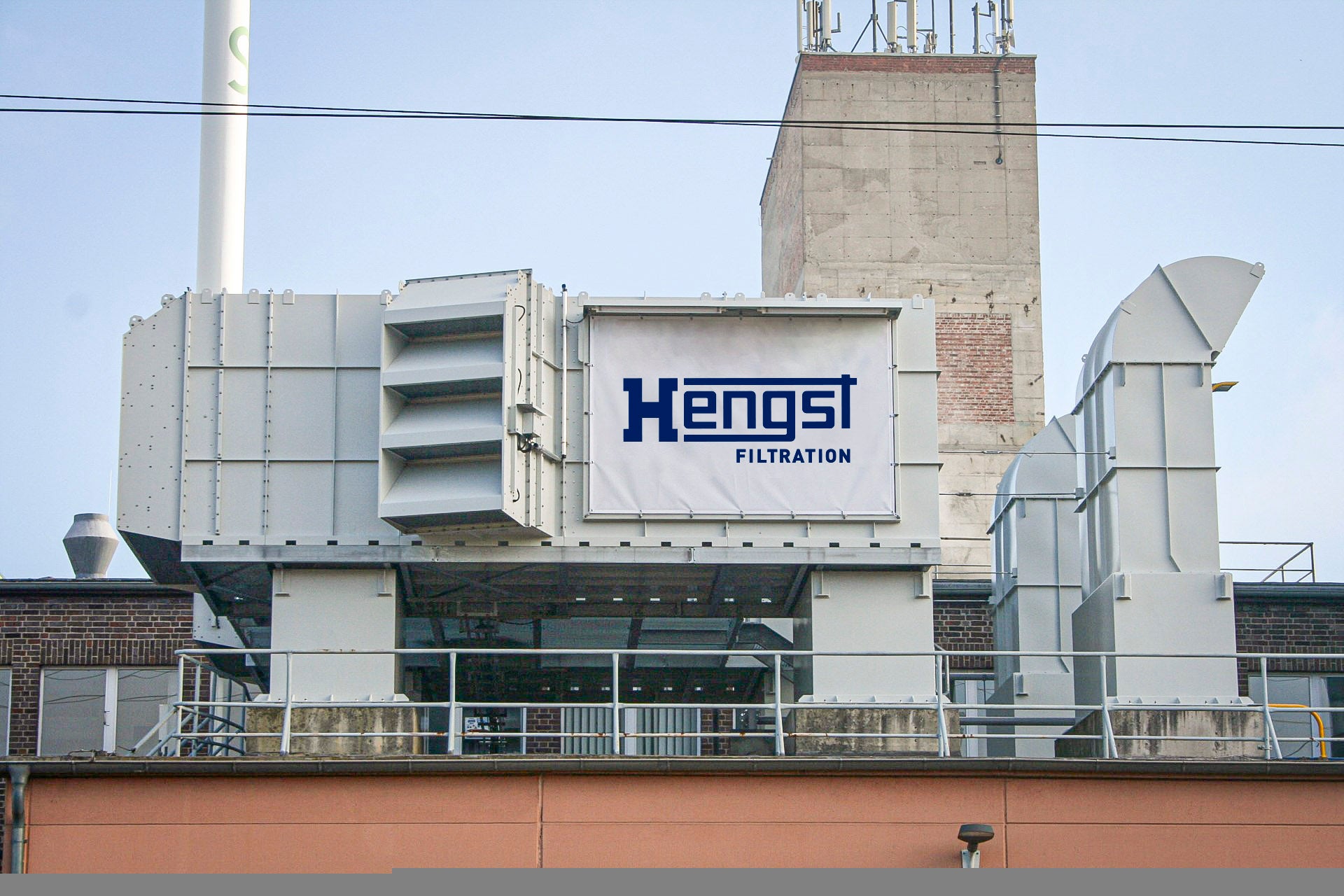
Particle contamination can create a range of issues for gas turbines. Larger particles can erode the blades, while a gradual build-up of the smallest particles will affect their delicate aerodynamism. Not to forget salt particles that will produce aggressive corrosion.
These negative effects can only partially be avoided by compressor cleaning, which itself creates significant downtimes and maintenance costs. What is required is an efficient, robust air filtration system that is set up to the specific environment and with minimum maintenance.
A new solution to old challenges
At a gas turbine power station in Germany, the pulse filtration air intake system was over three decades old and not functioning as effectively as necessary, leaving operators to tackle frequent unplanned shutdowns.
Because regular downtime of this kind needed to be avoided at all costs, the company opted to install a new, state-of-the-art Hengst Filtration MultiMaster Vario static filter system, complete with a three-stage filter setup.
This system not only protected the turbine blades but also helped the power station cut operational costs. The first stage consisted of bag filters type 4006 (ePM10 75%); the second stage of compact filters MultiPlus 8509 (ePM1 80%); and the third of compact filters MultiPlus 8511 (E11).
Installing the system came with its own set of unique challenges. This power station’s old filter house’s foundations rested on fixed concrete shafts, which had a dual function as a system to release exhaust air. Dismantling these shafts, therefore, was not possible, and Hengst Filtration experts had their work cut out for them when installing all three filter stages in the minimal space between the first and second shaft.
To find out more about how Hengst provided effective air filtration within a tight schedule despite on-site obstacles, download the paper below.