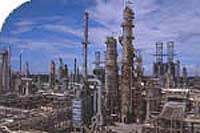
In 1997, Conoco and Pennzoil Products Company began full-scale operations of a new, $500m hydrocracker at its Lake Charles, Louisiana, complex. The refining process technology produces high-quality base oils that in turn allow the production of improved motor oils, transmission fluids and other industrial lubricants.
The Lake Charles Refinery located in Westlake, Louisiana is Conoco’s largest refinery, with a capacity of 248,000bpd. The refinery processes heavy, high-sulphur crude and low-sulphur crude and produces a full range of fuel products.
The initial project commenced back in 1994 and involved the construction of a lube oil hydrocracker facility, which was situated adjacent to the existing Westlake refinery. Later the hydrocracker owned by Excel Paralubes underwent a capacity expansion program, and in 1995-1996 the Conoco Refinery expanded to provide additional feedstock for lubricant production.
POTENTIAL DISASTER
A fire in early 2006 in the isomerisation unit of the Paralubes Excel plant also damaged the hydrocracker. The plant was shut down and this threw the lubricants market into confusion as Westlake is the US’s second-largest producer of base oils for the blending and production of lubricant products. The facility was back online by April 2006 and back in full production.
CONSTRUCTION OF WESTLAKE HYDROCRACKER FACILITY
The construction project was a 50-50 joint venture project between Conoco and Pennzoil Products Company (in 2003-2004 Pennzoil sold its share to Flint Hills Resources). The partners together constructed a lube oil hydrocracker facility requiring an investment in the region of $500m, which was raised on a project-financing basis.
The facility, which was given the joint venture name of Excel Paralubes, is able to produce currently more than 21,900bdp of high-quality base oils. Base oils are the main ingredients in finished lubricants. Site preparation work began in June 1994 and construction was completed within 33 months. Conoco acted as construction manager and operator of the lubricating base oil plant with support positions staffed by both partners.
PROCESS
At the lubricant production facility the main units are a 32,000bpd UOP hydrocracker and a 20,000bpd Isodewaxing unit. Vacuum Gas Oil (VGO) from the Conoco refinery is relayed to a vacuum distillation tower, where 15,000bpd of lighter distillates are removed and returned to the refinery.
The hydrocracker, operating at a pressure of 3,000psi and a temperature of over 1,000°F then ‘cracks’ the waxy gas oil and removes the unwanted sulphur and nitrogen impurities. The resulting effluent flows to the process dewaxer, which improves the viscosity of the base oil preventing the formation of gels, even at lower temperatures.
The dewaxed stream is hydrogenated to remove aromatics and also to stabilise the product. In the dewaxing section, a saturated-gas plant removes propane, butane, and naphtha from the reaction products.
The lubricant production plant has two sulphur-recovery units, each with a capacity of 90t/day working without oxygen enrichment, and 180t/day working with oxygen enrichment. A 2.5-million-barrel tank farm at the facility stores the feedstocks for the lubes plant and also the resulting products.
CONOCO REFINERY EXPANSION
Separately in 1995, Conoco committed an additional $250m to increase the existing refinery’s processing capacity and gasoline production capability. This brought the total project cost to approximately $750m and created approximately 2,500 jobs at peak construction and about 200 permanent jobs after completion in 1997.
The expansion involved an increase in the Vacuum Gas Oil (VGO) output. The project included an additional 40,000bpd atmospheric distillation capacity, 60,000bpd vacuum distillation capacity and 34,000bpd catalytic reforming capacity. In addition to this hydrogen produced from a new UOP Platform at the refinery is used in the lube oil hydrocracker.
CAPACITY UPGRADE
The upgrade in 1999 created a significant increase in group II base oil capacity, which was generated by a robust quality system that promotes continuous improvement of both product quality and production capability.
The facility was also QS 9000 certified within its first year of operation under the standard formulated by Chrysler, Ford and General Motors. The QS 9000 certification process incorporates ISO 9000 standards with additional elements to ensure continuous improvement.
Group II base oils, typically produced by severe hydrogen processing, contain greater than 90% saturated molecules and less than 0.03% sulphur. Traditional solvent refined base oils, classed as group I, generally contain less than 90% saturated molecules and more than 0.03% sulphur. The expansion programme included harnessing new technology, quality systems and process configuration as well as optimising process catalysts, which ultimately enabled the additional growth in plant capacity.
PETROZUATA TURNAROUND
This seven-week plant turnaround involved nearly 75% of the facility’s rated capacity, and involved tying-in the Petrozuata Syncrude project that had been underway in the refinery since August 1999.
The project enabled the refinery to process lower cost Venezuelan heavy oil from Petroleos de Venezuela SA The $163m project increased the refinery’s crude oil processing capacity and the production of refined products.
During the turnaround / tie-in activity, 15 of the refinery’s major process units were taken out of operation for various lengths of time. To complete the work, an additional 2,800 contract workers were added to the normal 750-person employees and 300 contractors.
Conoco budgeted $30m for both the turnaround and the Petrozuata tie-ins, with a major portion of the budget spent on labour and local purchases.
A 40-storey-tall crane provided by Deep South Crane & Rigging Company of Baton Rouge, was needed to complete two major ‘lifts’ during the turnaround. The two lifts involved removing a 20-year-old vacuum tower and installing a new one weighing 330t. S&B Engineers & Constructors of Houston was the main contractor.
CHANGES IN VENEZUELA
Due to a change in the political climate in Venezuela relating to foreign oil companies Conoco is about to withdraw from the country. In June 2007 Conoco and the Venezuelan government were unable to reach agreement and therefore Petróleos de Venezuela SA (PDVSA) will now directly assume the activities associated with Conoco’s interests in the Petrozuata and Hamaca heavy-oil ventures and the offshore Conoco development project.
This probably means a reduction in the amount of syncrude sourced from Venezuela being processed for lubricant production at the Westlake facility.