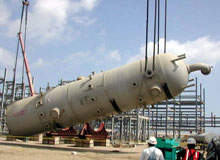
The Spanish Egyptian Gas Company (SEGAS) liquefied natural gas (LNG) complex in Damietta, Egypt, is situated on the Mediterranean Coast 60km west of Port Said. The complex came on-stream during the final quarter of 2004 and exports LNG to the Spanish market via a receiving terminal at Sagunto in Spain. The majority of the gas exported is used to supply the new ‘cleaner’ gas-fired power stations in Spain. This LNG project was the first facility of its type in Egypt and is one of the world’s largest capacity single train facilities.
Construction of the facility began in September 2001. The operating company, SEGAS, is controlled by Union Fenosa Gas in conjunction with ENI of Italy (80%) and two state-owned Egyptian companies, Egyptian Natural Gas Holding Company (EGAS, 10%) and Egyptian General Petroleum Corporation (EGPC, 10%). Union Fenosa Gas is owned in a 50/50 partnership by Union Fenosa of Spain and Eni of Italy.
The complex will initially produce 5.5 million t/yr (7.5 billion m³ per year) of LNG by air-cooled refrigeration and fractionation. The complex requires 270 personnel and production is around 600t/hr (24°C ambient air temperature). The estimated investment for the construction of the original facility was $1.3 billion.
Second Train
In 2005, not long after the first LNG train opened, SEGAS began considering plans for a second train with a 5.55 million t/yr capacity at the Damietta complex – after securing a joint off-take and feedstock agreement for Train 1 with Union Fenosa. With the first phase (first train) of the project approaching completion and commissioning in 2004, SEGAS started to raise investment capital for a second train. SEGAS asked four banks to arrange a $600 million, five-year corporate loan for the project.
In June 2006, Eni signed a new exploration agreement with Egypt for the El-Bougaz block in the Mediterranean and also outlined an agreement for the expansion of the Damietta LNG plant. It is thought that this will induce future gas exploration and development in Egypt (especially in the Nile Delta deepwater fields).
The second train will have a capacity of 7.6 billion m² (5.55 million t/yr) of gas per year for 20 years, which will just about double the capacity of the current plant. Eni believes that Damietta has the potential to become the Mediterranean basin’s gas hub, allowing the diversification of gas supply sources. The expansion will be undertaken by a partnership formed by Eni, Union Fenosa, SEGAS (Spanish Egyptian Gas Co.), BP, Egas and Egyptian General Petroleum Corp.
In June 2007, it was reported that the LNG expansion had been delayed because of ‘complications over securing committed gas supplies’. The additional train would allow economies of scale to be gained. However there must be sufficient supplies to make it a commercial prospect (a further 735 million ft³ is needed per day). The final investment decision for the new train is expected to be taken in 2008.
Export Gas Contracts
The liquefaction and export capacity of the facility has already been sold for the next 25 years. EGAS signed a ‘tolling agreement’ with SEGAS in June 2003. Under this agreement, EGAS will guarantee to sell the remaining 2.3 million t/yr of spare capacity not accounted for by the principal off-taker, Union Fenosa. Union Fenosa, the main investor in SEGAS, has already guaranteed to sell 3.2 million t/yr for the next 25 years.
EGAS has secured a five-year agreement with BG Group to supply gas to the Damietta site from the Scarab Saffron Fields in the West Delta Deep Marine (WDDM) concession offshore of the Nile Delta. The five-year contract was arranged between BG Group and EGAS, EGPC and Petronas. Under the terms of the agreement, BG Group will supply 225 million ft³/day for the first four years and then 150 million ft³/day in the final year. In addition, BP Egypt has signed an agreement with EGPC and EGAS to supply up to 310 million ft³/day of natural gas to the plant from 2008.
Contractors
The Halliburton KBR joint venture, Damietta LNG Construction Llc. (DLC), was awarded the contract for front-end engineering and design (FEED) in September 2000, and later the project management and engineering procurement and construction (EPC) contract for the LNG complex. The JV was also involved in the commissioning of the facility.
The JV incorporates companies from Spain, Japan, UK and the USA, including Halliburton KBR, JGC Corporation, MW Kellogg and Tecnicas Reunidas SA. The JV has also employed subcontractors for specific areas of the project including Soluziona (the services arm of Union Fenosa), ENPPI (Egyptian engineers) and Petrojet.
Halliburton KBR, through its London subsidiary, MW Kellogg, engineered the specific LNG train. The design was based on a FEED prepared by the JV team in the Halliburton KBR London office in early 2001.
The grassroots development has included the construction of the LNG liquefaction train, inlet gas reception area (metering and analysis), natural gas liquids removal and fractionation area, a docking jetty for tanker loading and transportation, LNG refrigerated storage and export facilities (tanks and booms), utilities and supporting infrastructure (power, water and roads), gas metering and treatment facilities (acid gas removal and dehydration), refrigerant condensate and LNG storage.
The environmental impact assessment (EIA) work at the start of the project (2001) and in November 2003 (addendum prepared on the changes from the FEED to the actual construction) was prepared by Komex. WS Atkins carried out dispersion modelling studies as part of the EIA. The EIA was prepared for a two-train complex and so a second train was always part of the original plan.
Contractors for Specific Projects
One of the major subcontractors employed was Saipem (EPC) who have installed two 150,000m³ PC LNG storage tanks at the Damietta export terminal. The PC LNG Tank is a storage tank system that integrates a pre-stressed concrete wall with an above-ground dual metal shell structure. The tanks are made up of the conventional low-temperature steel plate (nine percent Ni carbon steel) inner tank and the ordinary steel (carbon steel) outer tank.
Dodsal Pte Ltd was the subcontractor responsible for the construction of the mechanical works of LNG Train 1.
Parker Instrumentation provided the instrumentation manifold, valves and fittings for the project. This included their twin-ferrule A-LOK system along with a full range of tubing, compression fittings, ball and check valves, mono flanges, a range of manifolds and sun protection for the instruments against the harsh environment.
SGS Egypt was awarded the non-destructive testing (NDT) contract for the facility commissioning process of LNG Train 1. This included radiographic testing (x-ray and gamma-ray), ultrasonic testing (thickness, flaw and corrosion testing) and surface crack detection (using magnetic particles, eddy current, and dye penetrates). All of the NDT results have been archived in a specially designed database for full traceability if required.
LNG Receiving Terminal
The LNG is received at a new terminal that was constructed in Sagunto City, 50km north of Valencia. The terminal receives tanker shipments of LNG from the Damietta complex totalling over three million t/yr and then regasifies the LNG and distributes it to gas-fired power stations and the national gas pipeline.
The terminal was developed by three of the largest power companies in Spain: Union Fenosa (five percent)/Union Fenosa Gas (45%), Iberdrola (30%) and Endesa (20%).
The terminal was constructed in three phases and required an estimated investment of €315 million. The construction was carried out by a consortium of five companies that included ACS (Madrid), Nissho Iwai Corporation, Toyo Kanetsu KK and Osaka Gas Engineering Company.
Phase one of the plant has a processing capacity of 750,000Nm³/hr, which will give 6.6 billion m³/yr of outgoing gas. The first LNG carrier unloaded at the terminal in February 2006, allowing the facility to be brought on-stream in the first quarter of 2006.
Following the completion of the first phase of the Sagunto terminal project, there are now plans for further developments, which could include the construction of an additional 150,000m² LNG storage tank and an increase in send-out capacity to 8–9 bcm per year.
The third phase would then include the construction of two further 150,000 m² LNG storage tanks and an increase in send-out capacity to 10.2bcm per year.