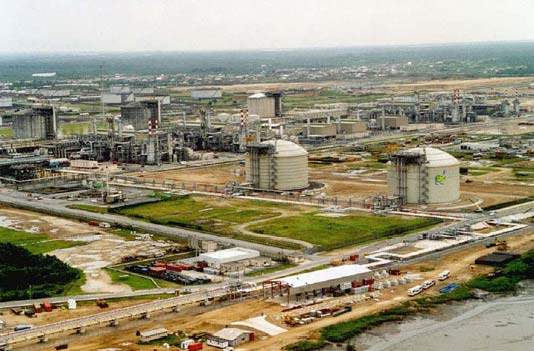
The Qatargas I LNG plant is located in Ras Laffan Industrial City, Qatar, and has been operational since December 1996. It is owned and operated by Qatar Liquefied Gas Company (Qatargas), a special-purpose vehicle established to build, own and operate the LNG plant. The plant uses natural gas from the giant North Field reservoir as feedstock and exports the processed LNG product to Japan, Spain, Europe, Korea and the US.
Qatargas was formed in 1984 and is owned by Qatar General Petroleum (QGPC 65%), ExxonMobil (10%), Total (10%), Mitsui (7.5%) and Marubeni (7.5%).
The estimated cost of the Qatargas 1 development project was $2.3bn.
The LNG project was announced in 1981 and broke ground in 1994. It was commissioned in 1997 with an initial capacity of 6mtpa, which was subsequently increased to the current capacity of 10mtpa through a debottlenecking project completed in 2005. In order to maintain the current production level, Qatargas initiated the Plateau Maintenance Project (PMP) in 2010.
The PMP project will facilitate increased feed gas rates from offshore wells and enlarge the onshore LNG plant capabilities. It involves the construction of new acid gas removal and sulphur recovery units near the existing units. In addition, continuous emission monitoring solution (CEMS) units will be installed on top of the gas and sulphur recovery incinerator exhaust stacks to reduce the sulphur level in the feed gas. The project is scheduled for completion in 2013.
Offshore details
The North Field was discovered in 1971. The offshore production and separation and treatment facilities are situated 80km from the mainland. There are three platforms and 22 production wells.
Each production train is 300m long. The sulphur recovery rate is 120t per day x two trains.
Infrastructure
Qatargas I LNG plant includes all attendant infrastructure including LNG storage tanks, loading jetties and three liquefaction process trains (designated trains 1, 2 and 3) of 3.2mtpa capacity each.
The Pre-front end engineering and design (FEED) activities for the project were completed in 2002 and FEED started in June 2003. At the production end of the project, where the gas wells are drilled, data and appraisal wells commenced in May 2004.
Qatar Gas II construction
Engineering work started with the verification of the front-end engineering design package provided by the owner, which required the complete redesign of the acid gas removal unit, the sulphur recovery unit, associated utilities and a plot plan.
Construction of the project started in 1994 with the site preparation and infrastructure development, such as a 35km access road and camp facilities.
The construction phase of the LNG process trains, jetty loading areas and storage tanks required 66.5 million labour man-hours, a concrete pour of 182,600m³, 9,300t of steel, 28,000t of pipeline and installed equipment weighing 32,000t.
Plant handover (PHO) of the first train was achieved in September 1996, 39 months from the contract award, and PHO of the second train occurred three months later, both ahead of the contractual schedule. The third train was awarded in July 1995, and PHO was achieved in March 1998, eight months ahead of schedule.
Debottlenecking programme
In December 2001, Qatargas carried out a debottlenecking programme of the three LNG process trains.
The work involved replacing or upgrading some of the key process equipment, such as compressors and turbines to expand the capacity of each of the three LNG trains from 2mtpa to 3.2mtpa. The engineering upgrades were executed during four one-month shutdowns, scheduled between 2002 and 2005. Two of the three original trains were successfully debottlenecked by 2003, and the third train was completed in 2005.
LNG shipping
The first LNG carrier departed from Ras Laffan port in December 1996, delivering the initial shipment to the Kawagoe Terminal in Japan to Chubu Electric Power for the world’s largest LNG-fed power plant (4,700MW).
The existing fleet comprises 12 purpose-built ships of 135,000m3 capacity each; ten of these vessels transport LNG to Japan and two to Spain.
Qatar Gas II project contractors
Chiyoda Corporation of Japan was the engineering, procurement and construction (EPC) contractor of the original plant.
Qatargas established a plant project task force team to manage and supervise the EPC contractor.
The debottleneck project was carried out by the Technip and Chiyoda joint venture (TCJV) under a €100m EPC contract. The joint venture is also the EPC contractor for the current PMP project. Other PMP project suppliers include ABB for 16 CEMS units and Struthers Wells for a thermal reactor furnace, waste heat boiler and steam drum.