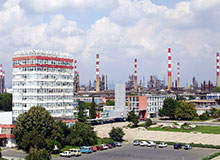
Lukoil Neftochim Burgas’ refinery at Burgas, Bulgaria, first came online in September 1963. It currently has a processing capacity of roughly 9.5 million tonnes of crude oil a year and alone accounts for approximately 7% of the country’s GDP. It produces motor gasoline, low-octane gasoline, diesel fuel, jet fuel, bitumen, vacuum residue, propane-butane, methyl tert-butyl ether (MTBE), process sulphur and polypropylene.
The refinery is undergoing a $1.9bn upgrade, which is aimed at increasing the annual production of Euro-5 diesel oil by 1.2 million tonnes and halting the production of high-sulphur fuel oil.
The front-end engineering design (FEED) studies for the two-phased upgrade were completed in the first quarter of 2010 and official construction works started in May 2012. The project is generating roughly 3,000 construction jobs.
Modernisation of the refinery at Burgas
The primary component of the modernisation project is the construction of the heavy oil (vacuum) residue hydrocracking complex, the largest of its kind in Eastern Europe, which is expected to come online in early 2015.
A new sulphur recovery unit (SRU-4) was commissioned in January 2015 at a cost of $71m, as part of the project. It has now replaced the older Sulphur Gas-2 unit at the refinery.
Financing for the modernisation project
A €420m (approximately $480m) export credit facility, which is 95% covered by SACE and was closed in November 2013, was provided by BNP Paribas (Suisse), ING Bank, Société Générale and UniCredit.
Construction
Phase 1 involves the construction of a 2.5 million tonnes a year heavy oil residue hydrocracker based on Axens H-Oil process, which uses ebullating bed reactors including an amine regeneration unit, a sour water stripper, and hydrogen production units.
Ancillary works under Phase 1 include the construction of a cooling tower, two substation buildings, two control rooms, two operator rooms, installation of precast pipe racks and utilities, and offsites upgrade.
Phase 2 will involve the construction of a vacuum gas oil hydrocracker (VGOHCK) unit, a second hydrogen unit and in-fixed bed reactors, with a feed throughput capacity of 1.8 million tonnes a year.
A new flare built by Balkani LK for the burning of waste gases was commissioned in February 2012 and a new 96ГВ285-19/19С screw compressor designed for compression and utilisation of flare gases was installed in December 2013.
New sulphur recovery unit at the Lukoil Neftochim Burgas refinery
The SRU-4 project involved the construction of two SRU identical trains with a capacity of 150t/d of liquid sulphur each, a common tail gas treatment (TGT) integrating an incinerator, with a capacity of treating 300t/d of tail gases from the two SRU trains, three 110t/d sulphur solidification lines and a solid sulphur storage facility with a capacity of 10,000t.
Contractors involved with the refinery modernisation
The FEED studies for the project were performed by Technip, who is also responsible for the engineering, procurement and construction (EPC) for Phase 1 of the heavy residue hydrocracking complex. Technip has subcontracted Sices Spa Italy and GP Group to carry out the construction and assembly works.
Total’s Antwerp complex comprises a refinery, the Fina Antwerp Olefins plant and a polyethylene plant.
The ancillary facilities are being constructed by Cordeel Bulgaria, while Devnya Cement is supplying approximately 15,000m³ to 20,000m³ of concrete for the project. Flowserve Corporation will supply ebullating pumping systems and barrel pumps for the project. Maire Tecnimont’s KT-Kinetics Technology was the EPC contractor for the SRU-4.
Recent activities at the Burgas refinery
Two desulphurisation units online in 2009, which anuually process 1.6 million tonnes of diesel and 1.1 million tonnes of gasoline while implementing technologies licensed by Axens and Haldor Topsoe respectively. ThyssenKrupp Uhde was the main contractor for the project.
The construction of the refinery’s SAAU, upgrade of the primary oil-refining unit (АD-5), and construction of the vacuum distillation unit (VDM-1) were performed by Globalstroy-Engineering. The refinery’s 100,000t a year sulphuric acid alkylation unit (SAAU) is based on Haldor Topsoe’s proprietary Wetgas Sulphuric Acid (WSA) technology.
Advanced process control (APC) systems for the refinery’s crude distillation (CDU) and fluid catalytic cracking (FCCU) process units were installed by Honeywell in 2011. A photovoltaic power plant and an outdoor switchgear were installed at the refinery by GP Group in 2011.
The automation solutions at the refinery are being modernised by EmersonProcess Management under a multi-year contract received in March 2010.