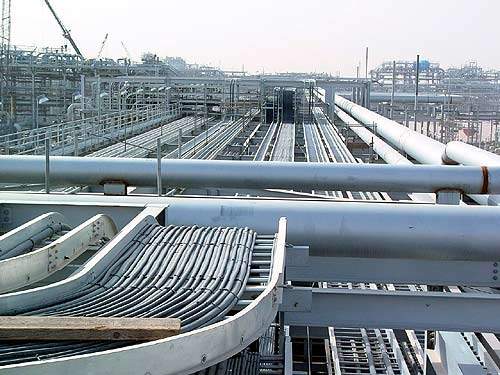
The Haradh Natural Gas and Oil Development lies 280km southwest of operator Saudi Aramco’s headquarters in Dhahran, Saudi Arabia. The work, which began in December 2000, consists of a gas plant capable of delivering 1.5 billion cubic feet a day of sales gas to Saudi Arabia’s Master Gas System and a gas oil separation plant (GOSP) capable of stabilising 300,000 barrels per day (bpd) of Arabian Light crude oil.
The GOSP associated with the Haradh – also known as GOSP2 – also includes a 130 million cubic feet associated gas-gathering facility. In addition to the sales gas, the Haradh Gas Plant is capable of delivering 170,000bpd of condensate to Saudi Aramco’s Abqaiq processing facility and can produce 90t of sulphur a day for export.
The gas plant came onstream in 2003. It has a design processing capacity up to 1.6 billion standard cubic feet per day of gas. The plant processes non-associated gas from the wells in the South Ghawar area.
The Haradh Natural Gas and Oil Development Project is the third mega-project completed by Saudi Aramco, which is the supplier for a quarter of the country’s total gas consumption.
Transmission to Haradh gas plant
About 87 wells feed the Haradh plant. The wells are connected to the plant via manifolds at Haradh, Wagr and Tinat. Sweet and sour gas from the wells is transported through the Haradh manifold, located 12km from plant.
The Waqr and Tinat manifolds are located 50km and 44km, respectively, from the plant. They carry sweet gas.
The gas is carried to the plant by five 20in and 30in gas transmission lines that total 130km and by associated headers, trunk lines and flow lines, powered by 13.8kV power lines and substations. The dry gas is carried from the plant via a 250-mi pipeline to the existing Riyadh line.
Gas oil separation plant (GOSP)
The plant consists of four gas trains to process the gas – two for the sweet low sulphur Unayzah gas and two for the sour Khuff gas. The Unayzah gas comes from the Haradh, Ghazal, Wudayhi, Waqr and Tinat gas fields, whereas the Khuff gas comes only from the Haradh field. In addition, there are two condensate stabilisers and two sour water strippers to perform gas dehydration, dew point control and sales gas compression.
In total, the facilities can process 1.6 billion cubic feet a day of a combined raw feed of sweet and sour. Up to 90t of sulphur per operating day will be processed and degassed and transported by truck to Berri Gas Plant. Once unloaded, it is pumped to Jubail Industrial Complex to a sulphur pelletising plant for export.
The main plant is made up of 100,000m³ of concrete, 22,000t of structural steel, 410,000 welded joints, 4,000km of cabling, 540km of plant piping, 1,400 items of engineered equipment and 750km of line piping, ranging from 18in to 56in in diameter.
Downstream of the plant, there is a condensate pipeline from Haradh to Abqaiq, 18in and 24in, 230km in length.
The Master Gas Grid includes five downstream 42in to 56in gas pipelines, 394km in length.
The three oil separation plants have been developed with a production capacity of 300,000bpd each. The project’s first increment, GOSP-1 started production in March 1996 and the second, GOSP-2 began production in April 2003. The GOSP-3 started production in January 2006.
Gas oil plant facilities
For the construction of the facilities, the companies used 32,000m² of office and workshop space, a residence camp for 1,000 men and supporting facilities and a Boeing 737-qualified airstrip, 8,000ft in length with day and night operations. Support systems included 2,500 telephone exchange lines and video conferencing, data networks for 470 users, ground-to-air radio, 306km of fibre-optics and five communications towers.
The total cost for Haradh is $2bn. Over a quarter of this ($681m) was spent within Saudi Arabia, including engineering ($25m), construction by Saudi contractors ($340m) and locally manufactured materials ($316m). At the height of operations, 10,600 men of 36 different nationalities were at work on the project.
Haradh contractors
The major contractors for the Haradh development include JGC (Japan) for gas processing facilities; Technip (Italy) for utilities and offsites; Saudi Constructioneers Establishment (Riyadh) for industrial support facilities; General Dynamics (Virginia, USA) for all permanent communications; Technip Saudi Arabia (Al-Khobar) for downstream gas and condensate pipelines; Suedrohrbau Saudi Arabia (Al-Khobar) for gas gathering manifolds and transmission pipelines; National Contracting Company for Hawiyah BSP
and Haradh Substation work; Middle East Engineering Development Company (MEEDCo) for overhead transmission lines; J&P Saudi Arabia (Riyadh) for Haradh Camp construction; and Al-Khodari (Saudi Arabia) for site preparation.