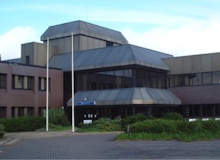
There has been an increase in the number of small-to-medium biofuel plants under construction. This is part of the search for cleaner fuels to run motor transport in the UK (this is part of the UK Government’s renewable transport fuels obligation). One of these was to be the UK’s first bioethanol plant at the British Sugar site at Wissington, near Downham Market in Norfolk, England.
British Sugar, along with several partners including BP and Dupont, has invested £20m into the project, with finance from the European Investment Bank (which is providing £120m for the Wissington and Saltend projects).
The plant broke ground in January 2006, and was completed and in pre-production by July 2007. A new fuel containing up to 10% biobutanol will be available from BP in 2012-13. In 2010, biofuels accounted for 2.7% of global use.
Mid-project conversion
In June 2006, only six months into the British Sugar Biofuel Plant project, the Wissington plant was converted mid-way through construction to allow it to produce the more advanced biofuel, biobutanol. The change was in part due to another larger plant under development at Saltend in Hull (Wissington is being used to develop biobutanol production technology).
British Sugar made it clear that biobutanol production at the Wissington plant will still use the same locally grown sugar beet feedstock as was originally planned for bioethanol production, and that it will be honouring all of the existing supplier contracts to surrounding beet producers.
The biobutanol plant was developed and constructed in a new joint alliance between BP and Dupont’s licensing process technology from Praj Industries of India (using DuPont’s bio-based science and BP’s fuel technology). The process can also be adapted to use other feedstocks such as wheat starch if required.
Renewable transport fuel obligation
The Renewable Transport Fuel Obligation programme, from April 2008, placed an obligation on fuel suppliers to ensure that a certain percentage of their aggregate sales are made up of biofuels or a certain amount of money is paid as an option.
The effect will be that 5% of all UK fuel sold from UK service stations must come from a renewable/sustainable source by April 2013.
The saving in carbon dioxide production can be up to 50%, and this is effectively recycled into the carbon cycle as the producing crop grows again.
Design and feedstock
The British Sugar Biofuel Plant uses sugar beet feedstock, which is plentiful in Norfolk, and the capacity of the plant is 70 million litres (55,000t) of biobutanol a year.
British Sugar and the National Farmers’ Union made an agreement on the contractual arrangements for the plant’s sugar beet supplies. The plant is designed to use sugar beet that would previously have been used to produce non-quota or ‘C’ sugar for export onto the world market.
Contractors
CEL (formerly Courtaulds Engineering) worked with British Sugar on the design and construction of the Wissington biofuel plant. Cowan and Linn, a Scottish Building and Civil Engineering consultancy, was also contracted by British Sugar to take part in the construction of the new plant. Nuttall John Martin of East Anglia was awarded the main contract to construct the biofuel production and storage/outloading facilities, along with the plant and associated works.
The cost of the civil construction package was £3.5m, with a construction period of 43 weeks. The new plant consists of an open steelwork structure with mesh/solid floor supported on a piled reinforced concrete raft, associated tank and fan foundations. Main areas of works included:
- demolition of existing piles and excavation
- construction of four main piled foundations
- plinths and drainage channels
- flooring for the storage tanks
- construction of three-storey steel-framed building
- access road, landscaping and related services.
King’s Lynn Borough Council granted planning permission for the new biofuel plant in December 2005. Praj Industries, an Indian-based company specialising in the processes that convert sugar into biofuels, was also involved in the construction of the new plant