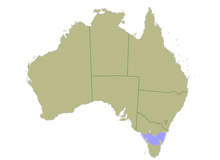
ExxonMobil Australia’s Altona refinery is situated 13km west of Melbourne, Australia. The refinery processes about 13 million litres of crude oil every day. Its major products are petrol, diesel, jet fuel and LPG. Other products include fuel oil and petrochemical feedstock
Production of the refinery is valued at $3bn per year. Nearly half of its production is petrol, diesel makes up 30% and jet fuel and other products form the remaining production. The quantity of each product produced depends on the type of feedstock being used.
Construction and infrastructure
Construction of the refinery started in October 1946 and it began processing crude oil in 1954. Since then ExxonMobil has made a number of improvements. In 1967 it enabled the refinery to process crude oil from the Bass Strait. Between 1996 and 1998 a fluidised catalytic cracker was installed at the refinery, which enabled it to process different types of crude oil.
In 2004 ExxonMobil upgraded the refinery to meet new national fuel standards. The upgrade allowed the refinery to produce diesel containing sulphur content of 50 parts per million (ppm) and petrol at 1% benzene. Since then sulphur in diesel has been further reduced to 10ppm.
The products produced by the refinery are blended and stored in about 80 storage tanks. From here, around 90% of products are transported by pipeline to ExxonMobil Australia’s Yarraville Terminal. The products are then distributed by road and rail. The LPG produced by the refinery is supplied to the Qenos plant, which is located at the Altona chemical complex and the LyondellBasell chemical plant in Geelong.
Processing
The first step of the refining process includes feeding crude oil into a distillation tower. The crude oil is then heated to the point of vaporisation. Compounds contained in the crude oil rise in the vapour and separate.
Depending on the weight of the molecules each compound rises to different heights in the distillation tower. For example, heavier molecules rise only up to a certain height but lighter molecules rise to a greater height. These compounds are then cooled to liquid form and collected onto collection trays at different heights.
Catalytic cracking is then used to further break down heavier compounds into lighter and more useful molecules. The cracking process is carried out at a high temperature using an alumina silicate-based catalyst. This takes the form of a fine powder.
Several other processes such as catalytic reforming, alkali treating, hydrotreating, alkylation and benzene saturation are used to refine the compounds produced in the cracking process. Some of these processes use heat and pressure to refine the compounds. Processes such as alkylation convert light gases into heavier and more valuable liquid fuels.
The processing units of the refinery are linked to each another through long pipes and regulated by valves. A central process control system monitors and regulates the functioning of all units.
ExxonMobil improves the refining process at the plant through its research and development. The compounds produced at various stages are analysed to enhance product quality. This step is also being used to meet new fuel specifications from the market and to improve environmental performance.
Connection
A significant proportion of the crude oil processed by the Altona refinery comes from the Bass Strait through a pipeline. An increasing amount is imported. This crude oil is supplied via tankers to the Point Gellibrand dock in Williamstown, Victoria, a few kilometres from the refinery.