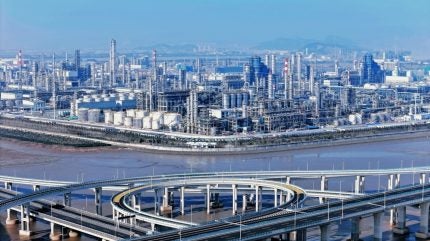
Sinopec has announced the mechanical completion of the second-phase expansion at its Zhenhai Refinery in Zhejiang, China.
The project has upgraded the refinery’s capacity to 40 million tonnes per year, making it the largest petrochemical industrial base in China.
The Zhenhai Refinery boasts an ethylene production capacity of 2.2 million tonnes per year.
Situated in the Yangtze River Delta, the Zhenhai Ningbo Petrochemical Industrial Base is crucial to Sinopec’s value chain, serving a major downstream product consumption hub.
With a total investment of 41.6bn yuan ($5.69bn), the expansion project includes 18 production units such as atmospheric distillation, catalytic cracking, polypropylene, and propane dehydrogenation units.
This enhancement is set to support the development of high-end polyolefins, advanced materials, and specialty chemicals.
The facility is expected to contribute approximately eight million tonnes of petrochemical products annually.
This boost in production capacity is anticipated to enhance supply chains for industries including automotive, home appliances, and textiles within the region.
The company noted that the project also made significant strides in technological innovation and sustainability.
Notable achievements include the localisation of ten core technologies, such as the world’s highest-load vertical labyrinth compressor, and the extensive use of smart technologies that enabled the simultaneous delivery of both digital and physical factories.
The integration of a localised industrial operating system and a self-developed industrial internet platform improved decision-making and management.
Energy efficiency was also a key focus, with comprehensive energy-saving measures resulting in an 11.7% reduction in overall energy consumption.
Throughout the construction, safety and quality were prioritised, leading to the achievement of over 90 million consecutive safe man-hours and a 100% quality pass rate for all units, setting a new industry standard.