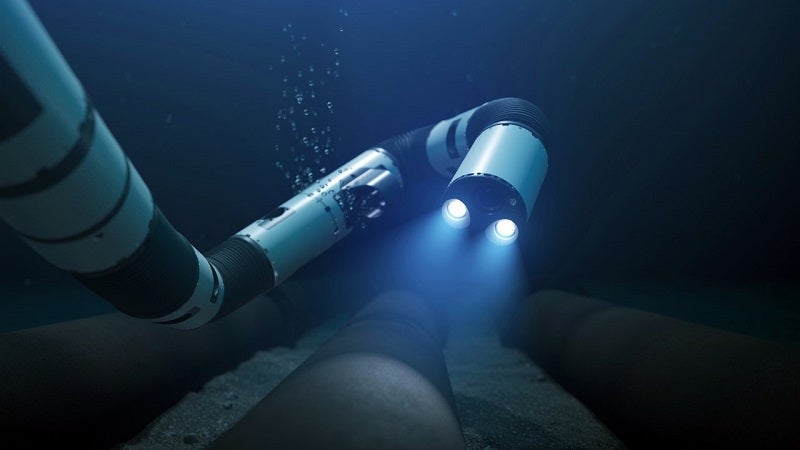
Robotics in the Oil and Gas Industry
The offshore industry is constantly looking to new technological innovations, and demand for robots in oil and gas is growing as the technology becomes more refined. Umar Ali explores five applications of robotics in the offshore oil and gas industry.
ANYmal
Described as the “world’s first autonomous offshore robot”, ANYbotics’ ANYmal robotic platform is a quadrupedal robot designed to operate autonomously in challenging terrain.
The robot is capable of inspecting offshore sites, and is equipped with visual and thermal cameras, microphones and gas detection sensors that allow it to generate a 3D map of its surroundings to carry out inspections and operations more efficiently. ANYmal can use this map to learn more about and better autonomously navigate the space it operates in, and can also be remotely operated from an onshore control site to provide its human operators with real-time data.
In a statement, ANYbotics said: “A crucial task for energy providers is the reliable and safe operation of their plants, especially when producing energy offshore.
“Autonomous mobile robots are able to offer comprehensive support through regular and automated inspection of machinery and infrastructure.”
ANYmal was first deployed on a North Sea platform in September 2018, performing 16 inspection points and carrying out a number of tasks, including reading sensory equipment and detecting leaks.
ARGONAUT
Developed as part of the Total-funded ARGOS Challenge to develop “the first autonomous surface robot for the oil and gas industry”, the ARGONAUT is another robot designed with routine inspections and autonomous tasks in mind.
The ARGONAUT was designed in the same contest that resulted in the creation of ANYmal and contains many similar sensors, but unlike the legged design of its competitor the ARGONAUT is a tracked robot and works in a pair, with two ARGONAUT units working shifts and returning to a docking station when they run low on power.
Total E&P UK head of technology & innovation Dave Mackinnon said: “We are on the cusp of delivering technology that will improve safety, reduce costs and even prolong the life of North Sea operations.
“Robots represent an exciting new paradigm for the oil and gas offshore industry and Total is proud to be part of it.”
The ARGONAUT was deployed in April 2018, first working on Total’s onshore Shetland gas plant before being relocated to the offshore Alwyn platform. The company hopes to “obtain a robotics solution on an industrial scale” by 2022.
Eelume
Developed by a spin-off from the Norwegian University of Science and Technology in collaboration with Kongsberg Marine and Equinor, the Eelume robot is designed to “live” permanently underwater and perform subsea inspection, repair and maintenance tasks. Eelume connects to a docking station on the seabed, which makes it easier to deploy than a conventional remote-controlled robot that would need to be sent down from the surface.
Its unique snakelike body affords the robot greater manoeuvrability underwater, allowing it to enter restricted subsea areas that would otherwise be difficult to enter with existing technology. The robot also has a modular design, with a number of tools that can be attached to it to equip it for various jobs.
Kongsberg CEO Arne Kjørsvik said: “The beauty of the technology is its multi-functionality. The Eelume sea snake demonstrates the same capabilities as the cruising marine robots developed by Kongsberg in that it can operate as a slender, torpedo-shaped underwater vehicle that swims in a straight line – effectively a cruising AUV.
“However, its other function is that it has an extremely flexible arm that can go in and under subsea structures to manipulate valves and perform a range of offshore operations inside, say, a subsea template.”
E-ROV
Developed by Oceaneering International in a partnership with Equinor, the Empowered Remotely Operated Vehicle (E-ROV) is a self-contained, battery-operated system designed for subsea operations.
The E-ROV operates remotely via an Ethernet connection, which allows the robot to be operated from a control room anywhere in the world. Equinor has also been developing a 4G network on the Norwegian Continental Shelf, with the E-ROV sending and receiving data via a buoy equipped with a on the surface
This Ethernet connection, as well as the E-ROV’s on-board battery and subsea charging station, mean the robot can operate without the need for a mother ship. This saves money and resources for subsea inspections, and has additional environmental benefits through the reduction of a ship’s carbon footprint and the number of mobilisations needed.
Oceaneering said: “Our self-contained, battery-powered remotely operated vehicle system increases operational efficiency and combines the best of Oceaneering technologies to deliver an industry-leading, resident ROV solution.
“This remotely operated system enables operators to intervene faster, keep production online more effectively, and perform routine tasks with fewer deployments.”
https://www.youtube.com/watch?v=-Fzy-CieWWM
Oseberg H
Operated by Equinor in the North Sea, the Oseberg H oil platform is the world’s first fully automated oil and gas platform. With no living quarters and no facilities the platform is entirely unmanned, only requiring one or two maintenance visits a year.
The platform was developed on the principle of “think big, build small”, being designed as simply as possible. This design ethos means Oseberg H was delivered ahead of schedule at $0.75bn (6.5 billion NOK), more than 20% lower than the cost estimate of the plan for development and operation
Production started on the Oseberg H platform on 14 October 2018. The development is expected to yield 110 million barrels of oil equivalent.
Equinor executive vice president for Technology, Projects and Drilling Anders Opedal said: “With Oseberg H we take a huge technological leap forward. The fully automatic, unmanned and remote-operated platform is digitalisation in practice, and I am proud of Equinor and its partners having chosen this in-house developed solution.”
https://www.youtube.com/watch?v=9yfqvetBYAk