
Scotland looks set to be at the centre of the coming seismic shift in connected technologies, with a commitment from the Scottish Government to a national rollout of a long-range, low power Internet of Things (IoT) network using low-power wide-area network (LPWAN) technology. The Scottish Innovation Centre for Sensor and Imaging Systems, CENSIS, has been at the forefront of the development of these networks and has already established several across the country, providing node-gateway range of up to three miles in urban areas and ten miles in rural locations.
The Industrial Internet of Things is going to be a real focus for oil and gas in the years ahead. Analysis from Accenture in 2016 suggested that 44% of companies in the sector are already investing in the technology and a further 36% will invest in IoT over the next three to five years. That places it behind only mobile devices in the immediate term and just behind Big Data and analytics in terms of future priorities – crucially, both of these relate back to IoT.
The technology is already manifesting itself in a number of ways. We’re seeing the fastest growth in areas such as robotics and autonomous vehicles, moves towards unmanned platforms, and innovations for the subsea factory. New areas are emerging all the time, including wearable technologies and the evolution of the “digital worker”.
Oil and gas is primed for the next industrial revolution – the industry could realise significant cost savings and other benefits from adopting IoT technologies. Asset downtime could be reduced with faster and better decisions using comprehensive condition monitoring and predictive analytics, while logistics and transport processes could be made more efficient with automated loading and asset tracking and monitoring. Challenging reservoirs, such as high-pressure high-temperature, will require significantly more monitoring through their entire lifecycle, as demanded by standards and environmental legislation.
Could other sectors show the way?
Transplanting IoT technology used in other sectors may be one route to rapid gains for oil and gas. For example, BMW has implemented a customised production line at one of its German factories that makes cars to individual specifications.
In a traditional setting, this is resource intensive, requiring an operator to change their tool settings as cars move through the plant. BMW has automated this through the creation of a 3D ‘work zone’, using ultra-wide band radio frequency tags on the car and tool to define dynamic zones in space. As soon as the worker steps in to a designated zone, the tool automatically adjusts to the required settings to work on the car passing down the line.
How well do you really know your competitors?
Access the most comprehensive Company Profiles on the market, powered by GlobalData. Save hours of research. Gain competitive edge.
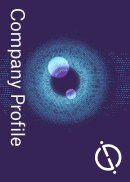
Thank you!
Your download email will arrive shortly
Not ready to buy yet? Download a free sample
We are confident about the unique quality of our Company Profiles. However, we want you to make the most beneficial decision for your business, so we offer a free sample that you can download by submitting the below form
By GlobalDataThis type of technology, which is well suited to use around metals structures, could be used in an oil and gas environment, where dynamic localisation of people and tools in 3D space needs to be mapped to centimetre accuracy.
In the oil and gas sector, companies like TechnipFMC are using IoT sensor devices to automate manual processes associated with monitoring and tracking assets over their lifecycle, including before deployment. For example, during transportation and storage, providing feedback on whether a crucial part may have been dropped or exposed to extremes in temperature.
There are a variety of other initiatives underway. At the University of Strathclyde’s Advanced Forming Research Centre, for instance, CENSIS has worked with a Livingston-based SME, Sensor-Works, on the development of an IoT-enabled condition monitoring device on machinery. It’s a technology applicable to oil and gas, allowing it to move towards preventative maintenance by measuring, analysing and trending vibrational signatures.
The effects of the IoT are going to be total and pervasive – it will have a significant positive impact on the entire oil and gas supply chain. The industry is in a prime position to make the most of the next industrial revolution. With the right support and investment, this could be a real turning point for the UK oil and gas sector and for the UK Continental Shelf – one it needs to grasp with both hands.