
Decommissioning can be an extremely unattractive prospect to offshore operators and platform holders. The process can be extremely risky, especially in terms of cost, and yet in most countries is legislated as a necessity once operations cease at a facility.
It makes sense then, that companies would want to stave off decommissioning as long as possible by extending the life of their sites, upping operational and cost efficiency, and increasing the worth of the site to get as much as possible out of their investment before they have to up-shop and arrange for dismantlement of their platform and pipeline.
A number of innovations have cropped up in the field of life extension, with technologies able to broadly be placed into the categories of digitalised techniques and software, and more physical solutions that aim to deploy corporeal assets to increase efficiency levels.
A 3D model for the future
Increasingly, the use of digital technologies such as 2D and 3D modelling is improving the efficiency of offshore installations. If operational costs are reduced, the potential value of a field increases, allowing operators to combat fluctuating oil prices and avoid early decommissioning by being able to afford to continue into the later stages of well operation, when profits start to decrease.
Russian design firm LCC Volgogradnefteproekt earlier this year reported a 30% reduction in annual operational costs of a construction project for seven offshore platforms located at the Vladimir Filanovsky field in the Caspian Sea thanks to use of 3D modelling techniques and asset management software through offshore design and technology company Bentley.
The accuracy of 3D modelled construction documents resulted in lower contractor rework fees and more accurate material use forecasting. As asset management software was integrated into the design phase, intelligent data can be used to schedule maintenance, repair and problem solving activities, resulting in much greater operational efficiency. Accurate data also means lower risk of human error, including industrial accidents and potential fatal loss of personnel.
How well do you really know your competitors?
Access the most comprehensive Company Profiles on the market, powered by GlobalData. Save hours of research. Gain competitive edge.
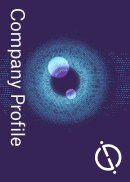
Thank you!
Your download email will arrive shortly
Not ready to buy yet? Download a free sample
We are confident about the unique quality of our Company Profiles. However, we want you to make the most beneficial decision for your business, so we offer a free sample that you can download by submitting the below form
By GlobalDataAn electric advancement in sensor systems
Digital modelling isn’t just useful for new-build offshore projects, though. In 2016, technological consultant FORCE Technology Norway claimed to have saved 65% – approximately NOK70,000,000 ($8,279,299) – of the original estimate on an offshore facility jacket using a combination of computerised modelling and data obtained using innovative survey software.
Cathodic protection (CP) systems protect metal structures from underwater corrosion through a process that allows them to act as an electrical cathode, and their use is regular practice within offshore facility maintenance, including for the steel frame – or jacket – supporting the deck and topsides of the platform. FORCE Technology developed a Field Gradient Sensor (FiGS) tool that precisely measures electric currents in seawater, resulting in data that can be used to accurately retrofit CP technology on jacket structures, and to predict the performance of the jacket in the future, allowing for accurate forecasting of when maintenance or replacement needs to be carried out. FiGS can also be used on other subsea assets, such as pipelines.
Getting physical with production buoys
Physical technological solutions tend to have a more tangible effect on life extension than digitalised solutions, requiring heavier investment into palpable assets. These technologies can increase efficiency levels phenomenally, yet the high-price barrier to entry can be off-putting for all but the largest offshore operators.
In August, a collaborative study funded by several international oil and gas companies – namely the UK Oil & Gas Technology Centre, Total E&P UK, Lloyd’s Register, Ampelmann, BW Offshore, Siemens, Premier Oil and Wärtsilä – was launched to determine whether reusable production buoy technology developed by Crondall Energy could be utilised by North Sea oil and gas reservoirs.
Floating production, storage and offloading (FPSO) units are utilised within offshore oil and gas to avoid having to install a pipeline to export oil. The idea behind the study is that a similar concept in the form of a production buoy could be used to unlock smaller oil and gas reservoirs within the North Sea, thereby improving the efficiency and potential of these marginal offshore facilities, making them more viable for long-term production.
Crondall Energy managing director Duncan Peace said: “New process and automation technology is playing a critical role in reducing the size and cost of offshore facilities and reducing the offshore man-hours required for their operation and maintenance.
“What makes our concept unique is the integration of these process and automation technologies with Crondall’s patented floating production concept, to deliver a material reduction in both the size of facilities and the level of manning. Together these innovations offer the opportunity to deliver a step change in lifecycle economics.”
Robots and drones: rise of the machines
The nature and size of offshore facilities means that many activities, such as maintenance and operation of equipment in hard-to-reach areas, are often hazardous tasks, with a potential threat to human life and very high inefficiency levels. This is why oil companies such as BP are looking into the use of robotic or drone technology to perform such tasks.
BP currently uses a magnetic robotic system fitted with a camera for inspection of its Thunder Horse platform in the Gulf of Mexico, as well as drone support to increase the detail with which inspection is carried out. According to BP, the technology reduced the need for manned inspections of equipment by up to 50%. The cost of such systems means that only the largest offshore operators can afford to invest in robotic and drone technologies, but as the technology continues to drop in price, flying drone fleets assessing offshore facilities could soon become the norm.
Both Statoil and Total E&P have expressed interest in robotic technologies; in 2017, Statoil established an unmanned site at its Oseberg H platform, while Total is looking into unmanned inspection systems for its Alwyn platform.