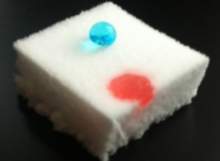
While the Deepwater Horizon disaster of April 2010 was a stark reminder of the inherent dangers of offshore drilling, it had the positive effect of refocusing attention on the development of new oil spill recovery technologies. Curiously, Hollywood actor Kevin Costner was one of those to benefit.
Looking for new ways to separate oil from water, in 1995 he bought Ocean Therapy Solutions – a company that built centrifugal oil-water separators – from the US government for US$24m. After years of struggling to sell to a disinterested oil industry, Ocean Therapy Solutions suddenly found itself tasked with fulfilling an order for 32 units from BP.
The spirit of innovation has continued to thrive in the years since, a fact to which the five examples below will attest.
Empa’s modified nanocellulose sponge
Swiss materials research institute EMPA has developed a new form of sponge that could have a big role to play in oil spill recovery. Designed by the organisation’s wood research arm, the sponge is made from chemically modified nanocellulose – a substance that occurs naturally in wood, straw and other such materials – and doesn’t sink in water, making it easy to recover.
The nanocellulose is extracted from these sustainable, recyclable materials, mixed with water and then pressed through a series of narrow nozzles at high pressure. The water is then replaced with air through a process of freeze-drying. This forms a sponge-like material but one that absorbs water as well as oil causing it to sink, making recovery difficult. To prevent the sponge from sinking, researchers mixed in an alkoxysilane molecule before the freeze-drying process, ensuring that the sponge fuses only with oil.
Oil spills in the Baltic Sea have continued to drop off in recent years.
In laboratory tests the sponge absorbed up to 50 times its own weight in mineral oil or engine oil and kept its shape well enough that it could be easily removed from the water by pincers.
MIT’s smart coating
The major difficulty of oil spill cleanup, as Kevin Costner realised, is separating the thick emulsion of water and oil. Researchers at the Massachusetts Institute of Technology (MIT) have developed a simple yet seemingly effective solution to this problem.
Professor Kripa Varanasi, graduate student Brian Solomon and postdoctoral fellow M. Nasim Hyder have developed a membrane made up of two layers of pore structures to help filter out unwanted materials – a very thin layer of nanopores and a thicker layer of micropores. Materials with different wetting properties can be used so their pores either attract oil and repel water or vice versa.
The difficulty was maximising oil throughput while ensuring the pores were small enough to block out unwanted substances. In the past this required the separation layer to be very thin or the pressure gradient to be increased, which had the effect of tearing the membrane.
To get around this the team created large holes on one side of the membrane that penetrate most, but not all of the way through the material, while on the other layer there are nanoscale holes. This way the surface with the larger holes provides structural support and strong throughput while the thinner layer ensures thorough separation. A range of different lab tests showed effective separation of more than 99.9%.
Gas-eating bacteria
Researchers at the University of East Anglia, UK have published a paper in the journal Nature suggesting that bacteria could be the key to dealing with the natural gas leakages that result from an oil spill.
The study shows that Methylocella silvestris, a strain of bacteria found in peat and different varieties of soil around the world, can grow on the methane and propane found in natural gas. While it has long been known that some bacteria could do this, this research is important because it shows that this strain alone can do the job. Lead researcher, Professor Colin Murrell, said of the findings,
"We have shown that one microbe can grow on both methane and propane at a similar rate. This is because it contains two fascinating enzyme systems which it uses to harness both gases at once. This is very important for environments exposed to natural gas, either naturally or through human activity. These microbes may play an important role in mitigating the effects of methane and other gases before they have a chance to escape into the atmosphere."
More experiments with wood in Wisconsin
Following a similar path to those at the Empa Academy, scientists in Wisconsin in the USA have developed a new sponge that has proved an affective absorbent of oil. Aerogel, as it has been christened, is also composed of cellulose nanofibres derived from wood products – especially useful in a part of America with a strong paper and pulp industry.
To prevent the material from absorbing water, the researchers mixed the cellulose nanofibres with polyvinyl alcohol – common in cardboard production and products such as contact lens solution – before treating the mixture with a water-repellent coating. As expected, the sponge began to absorb only oil.
The breakthrough was brought about through collaboration between the biotechnology laboratory the Wisconsin Institute of Discovery and the US Department of Agriculture’s Forest Products laboratory. The research team are now seeking funding from the petroleum or paper industries to help scale up the technology.
Oleophobic-hydrophilic coatings
In the same vein as the work being carried out across the Atlantic in Massachusetts, scientists in the UK led by JPS Badyal from Durham University have been working on oleophobic-hydrophilic coatings that let through water and repel oil. Seeing that the coatings currently on the market take several minutes to work, are complicated to make or inefficient, the team set out to make improvements.
The new product is very simple but a notable upgrade on what came before. The team developed an oleophobic-hydrophilic coating that could be applied to a piece of standard metal mesh, the kind that is used for screen doors. When placed in an emulsion of oil and water, the water dripped back into the container while the oil sat on top of the mesh in an instantaneous process of separation.