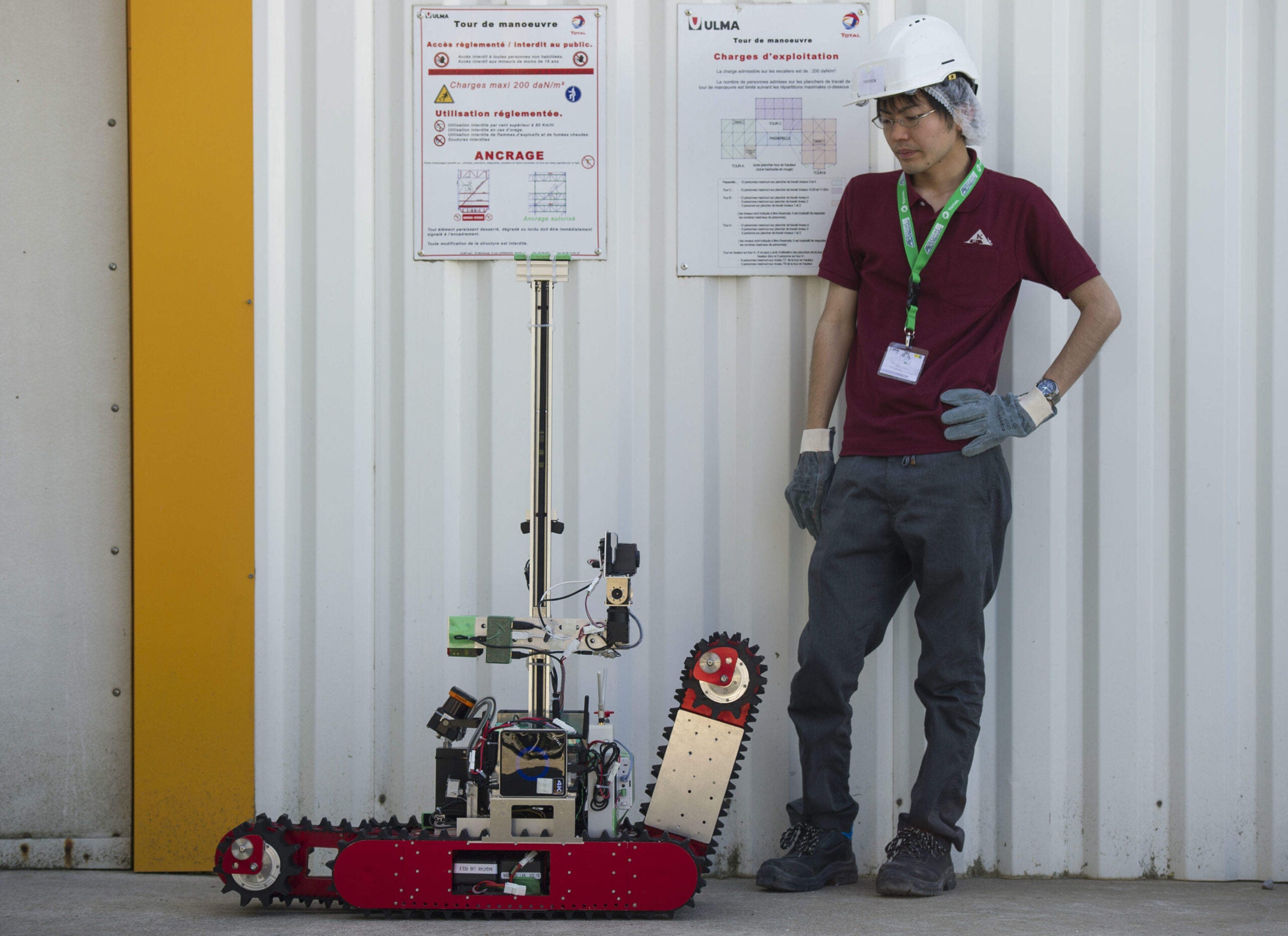
Robots are already used in the air and underwater by oil and gas operators, but soon they could be working on offshore platforms too, if an industry competition set-up by French oil and gas major, Total, designed to foster a new generation of purpose-designed ‘surface robots‘ goes to plan.
Not only does the team behind the challenge hope it will result in machines able to carry out routine inspection tasks on offshore rigs, but the specially designed robots should also be able to intervene in emergency situations and let human personnel know about any operational anomalies, reducing their exposure to challenging environments.
Robots have already made their mark in the oil and gas sector in the form of underwater remotely operated vehicles (ROVs), autonomous underwater vehicles (AUVs) and unmanned aerial vehicles (UAVs). While ROVs can help with everything from drilling to subsea construction, AUVs are designed to make detailed maps of the seafloor before infrastructure construction begins and UAVs can assist operators in surveying rigs, pipelines and other oil and gas infrastructure. But robots may not be limited to airborne and undersea tasks for much longer.
The challenge
Launched in 2013, Total’s ARGOS Challenge is an international robotics competition aiming to develop a new generation of autonomous robots to meet the specific needs of offshore oil and gas platforms. Throughout the challenge, five teams, which were chosen from an original line-up of more than 30, fight it out over three stages, with the level of difficulty increasing as the competition progresses depending on the results of the previous round.
Ultimately, the competition aims to produce a robot capable of carrying out routine inspections tasks autonomously – not only reading and recording the values on the instrumentation, but also knowing whether those values fall within a normal operating range and alerting human operators if they don’t – and intervening in emergency situations. The winning robot will also need to be ATEX certifiable – explosion-proof – so it can work in potentially hazardous environments.
“Operators currently carry out inspection tasks, but we want to strengthen even further the existing high level of their safety, the top priority for Total, and free them up to concentrate on added value tasks,” says Kris Kydd, head of robotics research for Total. “We also want to reduce the exposure of our staff in difficult environments such as harsh weather conditions and remote or isolated sites.”
Advantages of these surface robots would also go beyond improving the safety of human operators. “They will also contribute to optimising operations through greater responsiveness and higher reliability,” Kydd explains. “And finally, we want to boost the efficiency of future projects and increase the feasibility of projects in difficult conditions.”
The competition is being implemented in partnership with the French National Research Agency (ANR) and judged by a dedicated competition jury made up of of four international robotic experts and four Total employees, whose mission is to evaluate the teams during each competition and monitor the progress of the projects over the course of the entire challenge.
Encouraging early results
For Kydd, there were several advantages to introducing surface robots to the industry via the means of a competition. “A challenge instrument allows us to work with the robotics community in a collaborative way while testing different designs within a selective competition,” he explains, adding that it also encourages academics to come together with industrialists, research centres, start-ups and SMEs to meet the oil and gas industry’s specific needs.
“With the three competitions, we can verify the state of development of each robot at staged intervals, and it also allows us to showcase the emerging technology with our operations personnel, creating an internal dynamic at Total.”
So far, only one stage has been completed, in June 2015, with the second two to follow in April and December 2016, but early results have been encouraging. “We had a very intense week of competition and I’ve seen some very interesting results already,” Kydd notes. “I was impressed by the robots’ autonomous behaviour in terms of navigation and detection of a general platform alarm, which is a very important requirement for us. The competition was certainly a success for the state of development of the robots.”
That said though, he does believe the teams still have a lot of work to do, particularly when it comes to making their robot designs ATEX certifiable, a top priority for Total.
“The teams have to demonstrate that their robots can safely operate in potentially hazardous environments,” Kydd stresses.
The April and December 2016 competitions will also introduce a multi-floor setting where the robots will have to climb and descend stairs, adding a higher level of difficulty, and further safety testing will be carried out too, using different realistic operational mission scenarios.
Next steps
After the winner is announced in January 2017, next steps will depend on the state of the winning design, although the overall plan is to enter the industrialisation phase, where the design of the robot will be made more robust and fully ATEX certified. Then, more work will need to be done to bring the robot to the industrial pilot stage, which will take place on one of Total’s actual production facilities.
So ultimately, could we see these multi-functional machines replace human operators altogether? Not in all scenarios, Kydd confirms. “Robots are not meant to replace operators on existing manned platforms; rather, they will hopefully greatly complement each other and improve operator abilities to understand and control the industrial environment in a collaborative manner,” he explains.
Yet in extreme environments, where it is impossible to send human personnel to work and live for extended periods, it could be a different story. “With robust design, robots have the potential to exist and perform in such difficult conditions. To be honest, we do not fully comprehend yet all the opportunities they will offer,” Kydd concludes.