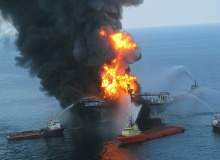
Fatal fires on offshore oil and gas rigs, such as the 2010 Deepwater Horizon disaster, which killed 11 people and resulted in an estimated 4.9 million barrels of oil escaping into the sea, and the 1988 Piper Alpha disaster, which caused 165 deaths, have highlighted the importance of designing and engineering rigs to minimise the devastating effects of fire in a notoriously hazardous environment.
Dr Jurek Czujko, who is CEO of Korean consulting engineering company Nowatec E&C, which specialises in offshore safety design and engineering, says that although techniques and tools in fire and explosion hazard engineering have significantly evolved since the Piper Alpha disaster of more than 20 years ago, untenable time pressures due to the global demand for oil and gas are in danger of making these advancements redundant.
We spoke to Czujko to consider the achievements and further challenges facing offshore fire safety rig designers.
Heidi Vella: What issues do you have to consider when incorporating fire safety into the design of an offshore installation?
Jurek Czujko: Offshore installations are at high risk of accidents, especially fires and explosions. They produce highly-flammable goods, oil and gas, and therefore naturally generate the potential for accidents.
How well do you really know your competitors?
Access the most comprehensive Company Profiles on the market, powered by GlobalData. Save hours of research. Gain competitive edge.
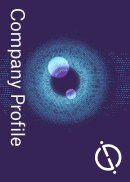
Thank you!
Your download email will arrive shortly
Not ready to buy yet? Download a free sample
We are confident about the unique quality of our Company Profiles. However, we want you to make the most beneficial decision for your business, so we offer a free sample that you can download by submitting the below form
By GlobalDataThe two phenomena, fires and explosions, are interconnected. Explosions are followed by fire, and fire often leads to some explosion. In order to reduce the consequences of such accidents, risk analysis is performed in the design phase of a platform construction.
It identifies how big the hazard is that a gas explosion or fire will occur. If you know what loads you are dealing with you can design for them – if you know how big an elephant is, you can design a car which will transport this elephant, right?
Just as knowing the weight of an elephant will enable you to design a car which will transport the animal, knowing the loads acting on a construction during an accident will make it possible to design an installation resistant enough to withstand these loads.
HV: What is Nowatec currently doing in this field?
JC: What Nowatec does is provide services within safety design to construct operational platforms in a way that will tolerate accidents. One example is an installation that is currently under construction, the Valemon platform. The platform is being built for a Norwegian company and is being constructed right now in South Korea. We have a long list of projects on the Norwegian continental shelf, plus in Vietnam and North Africa.
HV: How do you prepare design differently for long and short fires?
JC: When designing for a fire accident the length of a fire must be taken into account. Offshore installations are steel constructions, which makes them naturally resistant to short fires of [less than] an hour. But when the performed risk analysis documents the danger of a longer fire, like with Deepwater Horizon two years ago, then precautions must be taken to ensure protection of the platform.
Normally it is done by applying passive fire protection, which means using a special material that covers the critical structure areas, protecting steel from heat. There are a number of passive fire protection materials that can be used.
The problem is that applying passive fire protection is very expensive, time consuming and heavy. The enormous weight of a platform is a general construction challenge and all factors adding tonnes to the construction are kept to the minimum.
However, if the risk of long fires exists, there is no choice and the passive fire protection must be applied. The goal is to find the narrow margin of using enough material to protect the structure, but not too much to burden it unnecessarily. The integrity of the structure should be maintained until people are evacuated.
HV: How do designers and engineers design for accidents?
JC: Accidents do take place all the time and we must realise that it is not possible to design a totally accident resistant structure. The strategy called ALARP – as low as reasonably practicable – is applied. It means assuming that accidents will happen and being as well prepared as possible, trying to prevent accidents, and when they do happen, reducing their consequences both to the installation and to the people.
HV: How have fire safety design techniques changed since the Piper Alpha disaster more than 30 years ago?
JC: Since the Piper Alpha disaster it has been recognised that safety design is an obligatory part of the engineering process. The offshore industry is obliged to meet safety demands from various national and international authorities, like the UK Safety, Health and Environment (SHE). Safety must be documented in order for a platform to be able to operate.
In the last 20 years sophisticated tools have been developed for precise calculation of loads that structures are exposed to during accidents. In the case of fire on a platform, these tools can calculate what kind of fire loads and what kind of heat will come on different parts of the platform, and for explosions they can calculate precisely what kind of pressure loads will come on different parts of the platform.
HV: What can we learn from the Deepwater Horizon disaster?
JC: The Deepwater Horizon would not have happened if it wasn’t for human error. But the human error factor is not part of risk analysis. Nowatec’s scope of work includes functional implications of different kinds of failures of process equipment due to design, corrosion, lack of integrity and so on. The consequences of these factors are calculated in risk analysis, but human error factor is outside this scope of work.
HV: What are the biggest challenges facing fire safety design for offshore oil and gas rigs today?
JC: The biggest challenge today is time pressure as the process of offshore installation construction is time consuming, and at the same time the industry is pressed by the growing demand for energy worldwide. New platforms have to be developed in a shorter and shorter time.
Consequently, the engineering time in 2013 and 2012 is probably shorter than half of what it was 20 years ago.
The same platforms are designed in half the time, but on the other hand the requirements for safety today are twice as large as ten years ago. The amount of work needs to be doubled, with double the amount of safety in half the time.
HV: Is safety sometimes compromised because of time?
JC: It is compromised because it is not made a number one issue. There are a huge number of issues to consider during a platform design and under enormous time pressure. Safety aspects are often not a priority and this definitely has to be changed, as neglecting safety is ignorant and sooner or later inevitably leads to disastrous consequences.
HV: What can be done to change this?
JC: It does not help having laws and regulations for safety, as well as advanced tools to calculate safety margins in structure design, if these are not applied. In order to increase safety in the offshore industry, this aspect must be prioritised during the design and construction processes.
Related content
Space safety at sea: Nasa’s training mission for offshore workers
A safety programme developed by Nasa and Petrofac is helping oil and gas workers prepare for potential life-threatening situations.
Offshore security training: shaking up the status quo
In an unpredictable offshore environment, are the current methods of training offshore security personnel in need of a shake-up?