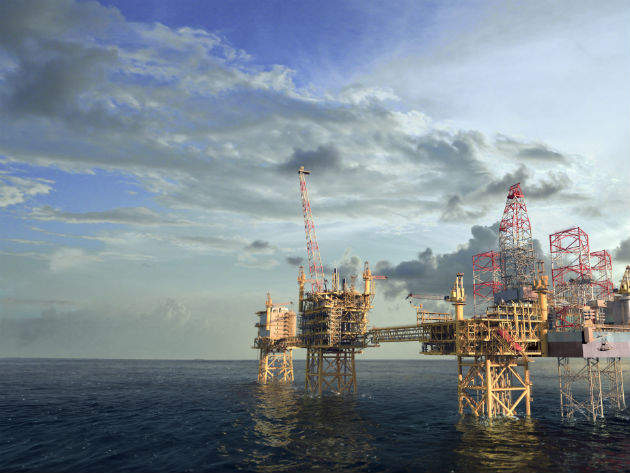
The sustained dip in oil prices is creating an interesting push-pull dynamic when it comes to the big data trend that has been gaining traction in the oil and gas industry. On one hand, with profit margins shrinking and production efficiency at the forefront of operators’ minds, for many fields the current climate isn’t conducive to investing in smart digital technologies and data analytics.
On the other, the benefits introduced by digital technologies – from remote communication to better predictive maintenance – could have a significant bearing on the cost-effectiveness and lifecycle duration of projects, and it is becoming clear that in the future, the most efficient fields will be those equipped with data-driven tools to maximise production while minimising downtime and maintaining rigorous safety standards.
Given the longer periods of time that they will be able to make use of digital advances, new projects are usually the best candidates for these sorts of technology investments. Maersk Oil is taking the digital plunge with the $4.5bn Culzean gas condensate field in the North Sea, which it is developing with its partners JX Nippon and BP (Britoil).
Culzean, which is expected to start production in 2019, is being designed as a digitised flagship, and as part of this effort, Maersk has been testing the use of augmented reality (AR), which allows offshore platform workers to receive real-time information on equipment via tablets or Google Glass-type devices, while onshore support staff will be able to provide guidance on repairs and maintenance based on live video feeds from the site.
Maersk Oil’s head of corporate technology and projects Troels Albrechtsen elaborates on the potential of augmented reality as a powerful component of next-generation digital systems in the offshore oil and gas sector.
Chris Lo: The oil and gas industry is known to have a relatively conservative mind-set when it comes to adopting new technologies – do you think the industry as a whole has been slow to investigate the potential of AR?
Troels Albrechtsen: I don’t think so. There’s a lot of risk in an industry like ours. You just don’t have the option of things breaking down and failing, so it needs to be really proven when you’re sending things 250km out to sea. You have very little chance to do things twice because of the loss introduced if you are having downtime on your production facility. It has to work, and has to be reliable. I think that’s the underlying conservatism that the industry is seeing.
So I think it’s all about planning, and if you look at the way we’re trying to deal with this is, we see the opportunity for things like augmented reality, in particular, coming when we have a new project where we can get it right from the start, and introduce it into the design. We can design, we can plan, we can implement. We can also train our people in ways of working that are commensurate with the technology that we deploy.
So the management of change brings much less risk, because we can plan and train for it. Whereas when you do it on an existing facility, it’s a little harder. What we envisage here is by experimenting and getting this done and get the experience on the Culzean field, we can take that experience and re-engineer it into our existing asset base, on that basis. So for us it’s a great opportunity.
CL: When did Maersk Oil start looking into possible AR applications for offshore oil and gas facilities?
TA: Well, we’ve looked at AR for quite a while. You probably know that in the onshore space it’s been looked at, for instance looking at simulation model output, so basically walking in augmented reality through models – in some of the centres, that’s being done. But in terms of bringing it offshore, as a company we have really waited to have the right project to do the test on. Culzean came our way, and it’s the type of project where we can afford it and which can benefit from it. We’ve looked at it for several years, trying to find the right opportunity to move forward.
We have three key objectives we are trying to achieve with this. We want to create inherently safer installations and operations. And this will do that for us; it’s a really strong driver here. The second is that it will, at the same time, create efficiencies that are really important for us to be able to afford to produce these fields for longer, and sustain production way into the future.
The third is a little bit less tangible but not less important in my world, and that’s to prepare for a long future where the people we will have working for us, for them Pokémon Go will be a natural part of life – the next generation will be so used to having information and experts available at their fingertips. Being able to supply them in the offshore environment with exactly that is part of what will make us successful. It’s also about bridging what we typically call the big generation shift, or the big crew change that will happen. We can’t expect to have people with 30 years’ experience everywhere – they will retire, and we need to compensate for that. I think this enables us to do that very carefully.
CL: How will the Culzean project incorporate AR into its operations?
TA: We’re planning on having that installed with tags around the platform, and fully wired with fibre optic cables, so we’re a fully digitised platform, and prepared for the growth in the digital space. That will mean that the frontline worker, with that infrastructure, could come up to a piece of equipment and immediately have available to him all the [data] and drawings that are relevant to that specific piece of equipment. He’ll know how it should operate; he will have the operating records for that piece of equipment available to him just by being where he is on the site.
And then, if he sees a problem or an anomaly, he’ll be able to call up a support facility onshore with experts. They can be in his ear, seeing the video stream of what he sees live, and provide him with live feedback on how he can best tackle that issue. And if that is not enough, they can call up an industry expert sitting in Houston or elsewhere, who can come in with minutes’ notice and take part in managing that situation or that inspection.
CL: Of the ways in which AR data can be displayed, which devices have you found to have the most potential in the offshore environment?
TA: The issue is around field-proofing, and of course it has to work every time and it has to be explosion-proof so it doesn’t interfere with our operations. I think the tablet devices are the ones that, at this point in time, have the least risk associated with them. We know that they work. Personally, I think we’ve only seen the beginning and there will be an evolution, and we need to make sure we’re ready to also do the Google Glass type of approach. But of course there are practical issues with those – battery life and so on.
CL: What effects could this integration of remote monitoring and AR equipment have on offshore maintenance and production efficiency?
TA: I think we should be really careful not to promise the world with this technology on its own. That is not what it does. But what it will do is make it easier to detect errors earlier. It will be easier to get the right types of interventions done, because you can bring experts into the field much more easily than otherwise. So I think the quality of maintenance will be higher by facilitating it this way.
CL: Can the potential efficiency gains brought by AR offset the cost of implementation in a low oil price environment?
TA: For new projects, I think this will be there. For retrofitting into existing installations, what’s the remaining lifetime of the facility? I think that’s going to be the thing that decides whether we can make those investments. If you can make good use of this over a five or ten-year period, then it makes a lot of sense to do, because if you think about the number of helicopter trips you could save from people going into the offshore environment, that is a tangible piece of cast-saving you can bank. But of course you need some time to be able to do that. So in that way, the cost of oil and gas has a pretty direct impact, because that impacts the timing of cessation of production for many of our fields.
CL: Looking further into the future, what are the more radical and complex applications of AR that the industry could be using in the decades to come?
TA: Oh, you’re asking me to look around corners! I don’t know, but there’s one particular area I would like to mention. For training of staff, instead of sending them for training on the facilities themselves, you train them with AR equipment using models of the plants that you want them to operate. They can do that on their own or as part of teams. That will, again, increase safety and efficiency. That’s just one.
It’s impossible to say where the technology can go. For us, we’re looking towards enabling our platforms to make sure we can capture the waves of technology development. That’s the important part for us. We can’t even imagine what’s going to happen – I think it’s going to be beyond our wildest dreams.