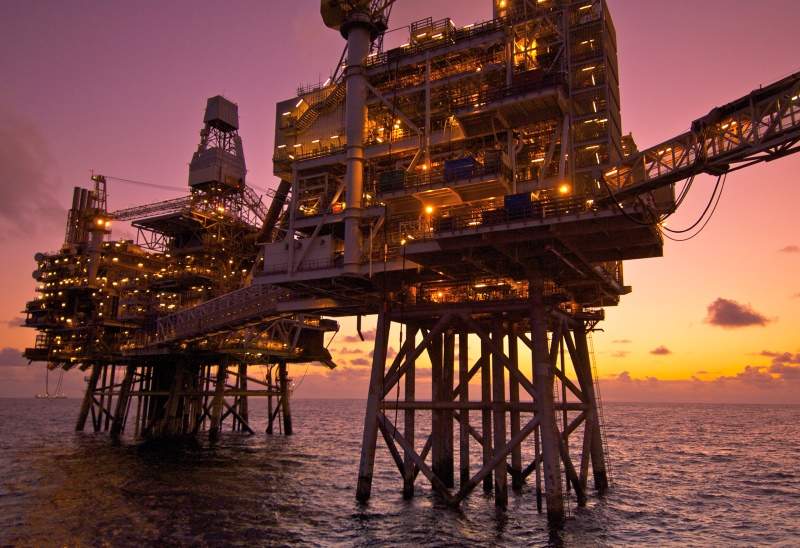
The oil and gas industry’s relentless pursuit of efficiency in the wake of the oil price crash appears to be paying off to some degree in the UK North Sea. There have undoubtedly been casualties of this push – primarily the hundreds of thousands of North Sea offshore workers laid off or dealing with significantly harsher working conditions – but there are clear signals that the pain is starting to pay dividends, from a macroeconomic perspective at least.
Unit operating costs on the UK Continental Shelf (UKCS) have almost halved, from nearly $30 a barrel in 2015 to around $17 today. The region’s steady production decline also shows signs of a gradual reversal, with output falling just 3% last year, compared to 12% in 2014.
Time and money: a focus on project delivery
But the focus isn’t just on streamlined operations and maximising hydrocarbon flow rates. A component of the UK’s general cross-sector objective to maximise economic recovery from the UKCS (MER UK) is improving the efficiency of project delivery.
A report published in March by the Oil & Gas Authority (OGA), which was established as an independent economic regulator in April 2015 in response to the recommendations of the Wood Review, studied 58 major projects undertaken on the UKCS from 2011 to 2016, and found significant room for improvement.
The OGA review team found that since 2011, less than 25% of oil and gas projects in the region were delivered on schedule, with an average delay of ten months. Cost overruns have been rife as well, with projects coming in at 35% over budget on average when compared to field development plan (FDP) estimates. One $500m unnamed project (all data presented in the report is anonymised) trebled its budget and is still incomplete, while nine of the 58 projects overran by more than two years. Capital expenditure, meanwhile, was at a record high during this period, averaging $15.4bn.
The report, entitled ‘Lessons learned from UKCS oil and gas projects 2011-2016’, attributed the main cause of the delays and budget blowouts not to the technical complexity of offshore projects but to flaws in organisation and project management.
“The lessons learned outlined in the report have been derived from extensive engagement with industry, with focus on how major projects are planned and executed, rather than technical scope,” said OGA operations director Gunther Newcombe in March. “One of the key findings was that there was no correlation found between the size and complexity of projects and delay, with the key factors being non-technical in nature.”
Delving into the five key lessons that were presented by the OGA – after analysing the data and conducting ‘lessons learned’ events with 13 operators and three tier one contractors – provides some insight into how oil and gas development projects are planned and executed, and where operators and contractors could improve the way they work. Outside of the specific lessons listed below, the report notes “a common necessity for more clearly defining the project scope prior to project sanction; keeping the project as simple as possible; increasing the accountability of project delivery; and improving the co-operation between companies/stakeholders”.
Organisation: bringing a project team together
Large-scale offshore projects in the oil and gas industry are a complex business, bringing together owners, operators, contractors of many stripes and a long supply chain. The OGA report acknowledges the virtual endless potential for miscommunication between these diverse partners, and notes a trend of growing costs and transitory labour that is more difficult to organise effectively.
“It was clear that there has been a trend toward increasing owner’s team costs over the last 10 years and an increasing reliance on temporary agency staff in both operator and engineering contractor workforce,” the report states.
Organisational strategies that could lead to more efficient project delivery include empowering delivery organisations with the authority they need to do their work properly, maintaining continuity of project teams between projects and early involvement of the supply chain.
“Time spent investing in aligning project team, partners, supply chain and regulators at the beginning is time well spent,” urges the report. “Don’t wait to develop and deepen relationships until after things go wrong.”
Project management
Given that the FDPs of so many UKCS projects have proven to be wildly accurate when it comes to expenditure and schedule estimates, it’s clear that project management – the ability to plan a project’s workload in detail and build a fairly accurate picture of the scope of the work – has been lacking.
“Despite an increase in processes, tools, project controls, supervision and engineering man-hours in oil and gas developments, there has been no visible improvement in the ability to predict outcomes,” says the report.
This lack of predictability may be partly attributed to the unreasonable expectations of some offshore clients and the writing-off of probabilistic planning, which can frustrate contractors. One anonymous participant quoted in the report made this clear: “Time and time again we are faced with clients driving unrealistic deterministic schedules. It has not been unusual for our customers to dismiss probabilistic schedule analysis and one instance of it being referred to as ‘mumbo jumbo’.”
The report states that realistic – “as opposed to aspirational” – schedules should be set at the outset of project planning, and project management expertise should be more proactively valued in the industry. The Engineering Construction Industry Training Board’s Offshore Project Management Steering Group could help point clients in the right direction in this area.
Front-end loading
Front-end loading (FEL) involves the pre-project planning phase, whereby a project is planned in concept, with an emphasis on analysing feasibility and evaluating risk before an investment decision is made. FEL can, the report notes, support the project management process by better predicting costs and providing benchmarking that can feed into a feasibility decision, especially for brownfield projects.
Problems arise when projects fail to plan ahead in enough detail, with the report finding that many schedule-driven projects – particularly those initiated in 2012-13 – kicked off without complete scope and with unclear objectives and priorities, and later paid for it in delays and budget issues.
The review team recommends confirming and tying down a project’s key resources – drilling rigs, long-lead materials, support vessels and the like – at the sanction stage. An unnamed contributor adds that due diligence on key contractors is a must:
“Ensure that there is the right level of due diligence when outsourcing key project management scopes to ensure that the resources provided have the right competencies and that the outsourcing company has robust delivery processes to support the scope – don’t assume.”
Execution: not just about contractors
The OGA recognises that blame for flaws in execution during the development and construction stage tends to fall on contracting and sub-contracting groups, which are primarily responsible for most of the major works. This is wrong, the report says, as failures in execution can be minimised or avoided “if the project is set up properly and all parties are clear on their responsibilities”. Execution flaws, in other words, are as much down to poor prior planning as to errors in the moment.
The report suggests that front-end engineering design (FEED), detailed design and construction are carried out in strict sequence to minimise confusion, and if not, aggressive risk management should be employed and contingencies should be developed based on those assessments.
Other challenges include transition management, with many projects underestimating offshore hook-up and commissioning effort in terms of time and cost. Subsea work programmes have tended to be more predictable, while drilling and facilities, especially floating production storage and offloading, “present a much larger spread of outcomes in projects”.
Winning behaviour
Behavioural factors governing the relationships between operators and contractors can have a significant influence on the success of a project, for better or worse. “Many behaviours continue to contribute to poorer project delivery, inflated budgets and schedule, or projects not even getting sanctioned,” the report warns.
Corporate behavioural issues identified by the report include excessive micro-management, lack of trust between stakeholders and over-optimistic reporting. “Many (but not all) operators issue too many specifications – many of which are not applicable or even contradictory,” says one contributor quoted by the report. “The larger the operator is, the more paper there is.”
Positive behaviours cited include agility and sense of urgency, devolved decision-making, respect and accountability, with smaller teams generally deemed more efficient and cohesive.
“Effective collaborative teams are smaller and, therefore, cheaper, and generally faster when everyone involved is seeking to deliver the end outcome in the minimum possible time,” according to the OGA report.
Lessons learned
Looking at the scope of projects between 2011 and 2016, the report noted that the industry’s ability to deliver projects seems to have improved over time. “Most of the significantly delayed projects were consented between 2011 and 2013,” it states.
The drive for efficiency across oil and gas operations prompted by the sustained oil price decline seems to be having a positive effect on project delivery as well as production efficiency, although the improvements made to project management have been less pronounced.
“There are also encouraging signs that the ability to deliver projects in line with cost and schedule commitments has been improving recently,” said Newcome after the report’s release. “This is aligned to the effort we have seen industry making in the areas of production efficiency and operating costs over the last 18 months.”
The challenge for the industry now will be to carry forward these hard-won lessons in leanness and not forget them if and when the oil price rallies to more profitable levels and the times of plenty return.