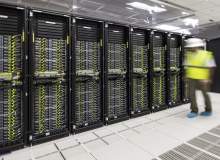
There is little doubt that the digital oilfield (DOF) represents the future of the offshore oil and gas industry. Given the industry’s development of complex deepwater projects in increasingly isolated locations, the benefits of data-enhanced techniques like remote monitoring and predictive maintenance have become abundantly clear. A deeply depressed oil price has moved digital technologies further up the agenda for many companies looking to deploy connected systems in their quest for lower production costs.
The digital oil field is no cure-all, however. The technology is an important aspect of the DOF concept, but the ability for a company to adapt its staff and processes to truly take advantage of these data-driven systems is just as vital, if not more so.
This was the point being made by Tony Edwards, a 20-year offshore veteran who now heads-up digital energy consultancy StepChange Global, at a conference session of the recent ITF Technical Showcase.
"If you don’t change the way you work, you gain very little," Edwards said.
Offshore Technology caught up with Edwards to discuss in more detail the operational changes required to make a success of DOF, and to gain his insights into the opportunities and challenges facing companies as the industry continues the slow march into its digital future.
Chris Lo: Do you think that, in the DOF sector, there’s too much focus on the technical aspects, as opposed to organisational change and human factors?
Tony Edwards: Yes I do, in short. In some respects, digital oil field is an unfortunate name in that it implies data and information technologies, when this is really about changing the way you work such that it’s aligned with the fact that you’ve got real-time data and information and can work faster and with higher quality.
If you walk into an office that does this well, what do you see? What you see is people working in a nearer real-time way utilising data and information. So instead of things happening today and you call a meeting for tomorrow and you do something about it the next day and you might have a fix next week, you can actually respond to that issue or opportunity for production improvement within hours. But you need to organise to do this. That means aligning your people, processes and organisation so that you actually capture value from having the data and information.
CL: How well would you say offshore oil and gas companies have done to get the most out of DOF over the last decade?
TE: I think there are some excellent examples of what can be done and people implementing this well. And of course, there’s a series of companies that started between 2003 and 2005 and have been doing it for more than ten years now, but there are some companies that are only just kicking off.
I think overall, the picture is pretty mixed, if I’m honest. I think there are some companies that have done this well, some companies that started off well and almost slid backwards, and some that haven’t even started yet. As an industry, I think it’s pretty patchy. There are some pretty good examples – the one standout example that everybody quotes is ConocoPhillips Ekofisk in Norway. BP did the Advanced Collaborative Environments and the Field of the Future programme in Aberdeen and other locations around the world. Others such as Shell, Statoil and Saudi Aramco have had success with this approach.
Overall I think that has been reasonably successful but there is still more value to be gained. To an extent, we’ve fallen a little into the trap of more data means more work, which means more people, rather than more data and information means more efficient work and more efficient people. At $110 a barrel, it’s just been too easy to recruit a few more people to look at this data.
CL: What are the most common errors that restrict companies trying to derive benefits from data and digital tech?
TE: The number one is if you think of this as an IT or technology project, you probably seal your own fate as you will not tackle the change issues sufficiently well. That’s partly because you’ve got to enrol the people on the operational assets – the reservoir engineers, the petroleum engineers, the operations and facilities guys – into changing what they do. A key success factor is working with the right people in the organisation. Typically, we work with operations VPs and asset and operations managers, those sorts of people. When we do that it works well.
The guys who do this really well don’t think of it as a project, they think of it as continuous improvement, so they don’t stop. As soon as you think about this as a project and stop, the tendency is that it can fade away. People change out, people move on, and it’s not embedded and sustainable.
Another key factor is leadership. All of the most successful implementations have local and global leadership that understand the concepts and opportunities opened up by digital oilfield and actively lead the change in the way of working.
CL: You’ve noted before that a lack of trust between onshore and offshore staff is surprisingly common in the industry – given the importance of remote operations to the DOF proposition, could you elaborate on this issue?
TE: Well, I think that’s absolutely the case. I sat on a platform in the mid-90s and we were a standalone organisation; if anything happened we had to look after ourselves. So we weren’t used to having support, or support was intermittent. And frankly, on a day-to-day basis, who on the beach knew what was going on? The answer was nobody, really. So what we’re trying to do with collaborative environments is to have situational awareness, which means the guys on the beach actually know what’s going on in any one day, so you can then build teams between onshore and offshore that are connected in real-time, working together as one team regardless of the location.
If you don’t have a trusting relationship between onshore and offshore, then decisions or opportunities identified in the office aren’t acted upon. The opportunity to analyse the situation to identify opportunities is now much greater than it was. But that can’t really be done by the guys in hard-hats offshore. So if somebody else is doing it, then where are they doing it and how are they connected to the people offshore so any opportunities actually get acted on?
CL: Are there other sectors or industries integrating the same kinds of networked technologies that the offshore industry could learn from?
TE: There are two or three sectors that we look at. One is the defence sector. Actually the whole concept of situational awareness came out of friendly fire issues during the first Gulf War. So guys on the ground calling in air strikes and they were getting hit themselves instead of something 500 yards away. So a lot of this theory about doing things fast, synchronised over multiple locations and going through multiple organisations – that comes out of a lot of the defence thinking.
The other area that is interesting for major projects is the physical systems integration idea that comes out of the aerospace industry. So somebody makes the wings, somebody makes the fuselage and then it all gets integrated. It’s not just that everybody makes everything anymore.
CL: Do you think the offshore workforce needs to change from a heavy engineering focus to more software and IT skills?
TE: In terms of skill set, I think there’s a lot of talk about the digital engineer. The Society of Petroleum Engineers has come up with this concept of a digital petroleum engineer. It’s a hybrid discipline that sits across the two and I think something like that does need to emerge. But my personal view is that digital engineering, if you want to call it that, will be more like project engineering. I think it will become one of those core skills that when graduates go into BP or Shell in the future, they’ll not only do the module on petroleum engineering, they’ll also do the module on data engineering. I think it will be one of those disciplines where everybody’s got to have an awareness of it, whether you’re facilities, ops, projects, production, drilling, whatever. Everybody will have to be able to do some.
CL: If the challenges of implementing the digital oil field are properly addressed, do you think it could be the key to running efficient operations that remain viable in a low oil price environment?
TE: Oh yeah, absolutely. If you look at the current environment, especially somewhere like the North Sea but other areas as well, just doing the same old model with the same old relationships and driving costs down by 15-20% doing the same amount of work, I just don’t believe is going to do it. We’ve fundamentally got to become more efficient and I think because of that, the relationship between suppliers and operators has to change.
There are already some moves in this area. Statoil has been doing some really interesting work; service companies are normally selling an engineer by the day, but Statoil has started paying for the quality of the data it receives. So it’s a different contractual model.
I feel now that we’re in a place where most companies have got some digital information, they’re not using it and now we need to do the organisational realignment to make the most of what we’ve got. That’s not easy, but you’ve probably already spent 80% of the money by buying all the fancy data. So you might have spent 80% of the cost and got 20% of the value, and now you’ve got to spend the other 20% on the soft stuff to get the other 80% of the value. But the other 20% is a lot of effort, because it’s change.