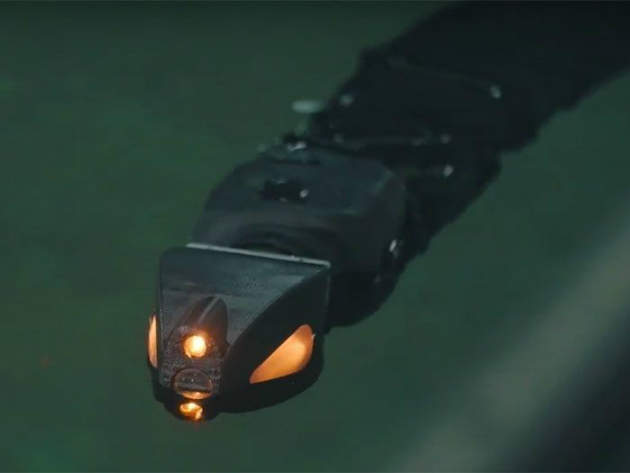
Arne Kjørsvik is the CEO of Eelume, a developer of autonomous intervention vehicles (AIVs) based in Trondheim, Norway. A specialist in control systems for the offshore industry as well as marketing, sales and system development, Kjørsvik was previously employed in various roles at Marine Cybernetics (a part of DNV GL), MARINTEK, Kongsberg Defence & Aerospace and Novotek.
Julian Turner: Can you describe the concept behind the Eelume robotic sea snake?
Arne Kjørsvik: The research project began in 2002 here at the Norwegian University of Science and Technology (NTNU) in Trondheim with the idea to create a robot that could mimic the movements of a snake.
Norwegian oil company Statoil and professors at the University recognised the potential to operate the snake in water – snakes are great swimmers, after all − and therefore its potential applications in the offshore industry, the concept being that if you could design a robot that resembles an eel or a snake it could be manoeuvred around subsea structures to conduct inspections and operate valves.
We launched Eelume in June 2015 and have a development project in collaboration with Statoil and Kongsberg Maritime to demonstrate the ability and commercial viability of the robot snake solution.
JT: How does the technology differ from the plethora of other autonomous underwater vehicles and remotely operated vehicles (ROV) available to the offshore industry?
AK: The beauty of the technology is its multi-functionality. The Eelume sea snake demonstrates the same capabilities as the cruising marine robots developed by Kongsberg in that it can operate as a slender, torpedo-shaped underwater vehicle that swims in a straight line – effectively a cruising AUV.
However, its other function is that it has an extremely flexible arm that can go in and under subsea structures to manipulate valves and perform a range of offshore operations inside, say, a subsea template.
So, one major difference between the Eelume vehicle and its potential rivals is that it has two major capabilities built into the same unit. First, there’s the AUV mode where the robot travels in a straight line between different objects to perform underwater surveys, and second its ability to perform manipulation and inspection tasks similar to those carried out by a regular inspection ROV.
The other advantage is that this unit will be subsea resident, installed close to the template or other installation, without the need for a surface support vessel. The plan is to have an offshore docking station that supports the robot with power and communication, which means it doesn’t have to be installed on a drilling vessel itself.
JT: Subsea costs have tripled since 2005. How can the sea snake save offshore operators money?
AK: The potential cost saving for offshore companies is significant because the sea snake may reduce the need for surface vessels, reducing the fuel base during costly and time-consuming inspection, maintenance and repair tasks. The resident solution will not only help customers improve their maintenance performance, but also accelerate production by reducing the number of vessel days.
Existing subsea infrastructure is ageing, increasing the demand for maintenance. At the same time, new offshore installations are more complex due to greater depth and more challenging reservoirs.
Most of the oil majors now have programmes or projects that require resident subsea technology, meaning they are either converting traditional ROVs into resident technologies or they are looking into alternative technologies such as ours. In addition to cost savings, getting rid of the surface unit also extends the operational duty cycle because you are not as vulnerable to weather and sea state.
JT: Which technical innovations are incorporated into the Eelume sea snake?
AK: The robot has a modular-based design based on flexible joints that recreate the unit’s snake-like behaviour as well as rigged sections or modules that contain electronics sensors and battery packs.
It has a very flexible design, meaning it can be put together in different configurations depending on the mission objective. The eel-like motions are created by thruster units; for example, two forward units mounted on the hull plus vertical and horizontal thrusters so the robot can move sideways, and up and down.
This gives the sea snake extremely flexible manoeuvrability that mimics actual snake behaviour. It can turn easily and change shape in order to enter condensed, restricted areas. We can also modify the robot by adding different types of sensors and integrate other functionalities into the system.
JT: How will the technology specifically be used by offshore oil and gas companies?
AK: In offshore fields, inspection projects are very important and the sea snake can perform many complex tasks such as moving in between different installations to monitor pipes for leaks. Because it is autonomous, clients can record and compare data from project to project to identify changes.
Also, if operators discover a problem on the seabed, they can use the robot’s valve-operating tool to close the necessary valves from onshore without any surface vessel, which is a major cost saving.
The robot also has other potential applications beyond offshore and is designed for any industry that requires subsea inspection or related manual capabilities to be carried out around the clock; for example, the Eelume may also be of significant benefit to the aquaculture, fisheries or defence industries.
JT: When will the Eelume robotic sea snake be ready for full commercial deployment?
AK: In December 2016 Eelume tested the robot at a depth of 150m and the next step is to build and develop a new version that can operate valves and carry out inspection tasks and new routes at 500m. We also plan to improve the vehicle’s automation to further increase its manoeuvrability.
Another major development task for the coming year is to work on the human/machine interface so that operators can learn how to move the snake easily. Once that has been completed, we will develop a battery package fitted into the unit so we can operate the solution without any cable. Also, at present, there is a temporary umbilical between the vehicle and the docking station, but we plan to remove that.