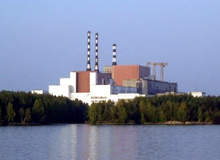
Despite new finds and continued exploration, the pressure to exploit existing resources to the full remains strong, and that inevitably leaves many companies looking to upgrade their offshore assets. Achieving it, however, presents the industry with a difficult balancing act to perform in matching the commercial pre-requisites of efficacy and economics with the demands of increasingly stringent health and safety legislation and environmental regulations.
The situation in the North Sea is a prime example. With many of its fields now in their mature phase, decommissioning would ordinarily be fast approaching for a large number of the ageing rigs.
The cost of dealing with 450 of these fields by 2030 has been estimated at between £15bn and £20bn by Royal Bank of Scotland oil and gas banker William Stevens – but that was back in 2008. Two years on and it is not just the economic climate that has changed; for offshore UK at least, the fiscal landscape has also moved.
While UK Chancellor of the Exchequer Alistair Darling’s December 2009 pre-budget report may not have signalled the tectonic shift that some had hoped for, relaxing the field allowances criteria could, “support the recovery of up to 300 million additional barrels of oil and gas from the North Sea”.
Meet the challenge
Not everyone is convinced that moves purely centred on the ultra-high pressure, high-temperature field allowance will be enough.
“It was a start, but Darling could have been bolder,” says industry consultant Richard Lightman. “How about some serious tax breaks to push things along or some sort of real incentive for more investment in existing fields? That would have helped. As it is, operators are left trying to squeeze out every last drop and doing that cost-effectively – and safely – is going to be a big challenge.”
For rigs that are 25 or 30 years old, that challenge comes with the added dimension of the changing conditions and physical parameters concomitant with such an operational lifetime.
As well as the self-evident needs of the likes of new-entrant companies such as CNR, Talisman and TAQA, which are engaged in attempting to extend field life and tie back new reserves, these demands drive different requirements. Upgrading may be the logical move, but it is not necessarily a straightforward one.
Health and safety
An eternal industry concern is health and safety, so it is scarcely surprising that it should feature prominently in North Sea upgrades. Statoil’s ongoing project on Snorre is an example. As Torstein Hole, the company’s senior vice president, Operations West in Exploration and Production Norway, explains, “the total capital expenditure for Snorre in 2009 and 2010 amounts to NKr5bn ($845m), of which health, safety and environmental measures account for over 50%”.
Replacing the current fire and gas alarm system alone calls for NKr450m ($76m) of capital expenditure. Scheduled for completion in 2012, it is to be a comprehensive overhaul that will see the main contractors Apply Sørco revamp the system while the platform remains in full operation with the existing warning installation staying functional throughout.
During the course of the work some 2,000 new detectors will substitute the existing 1,700, while 36km of cabling will be replaced and an additional 11km laid, significantly improving coverage.
“This will make the platform’s warning system more robust and will represent a big safety improvement,” says Hole.
The price-tag may be high, but then so are the benefits. Statoil has been active on the Norwegian continental shelf over recent years, carrying out extensive upgrades and modifications to its installations – and Snorre has the largest remaining reserves of all the company’s fields there. The lure, as Hole makes clear, lies in “increased production and an extended lifetime up until 2040”.
Technology’s new frontiers
The inexorable rise of upgrading is not solely restricted to the North Sea. Momentum is gathering across the industry. Last year, for example, Keppel’s BrasFELS yard in Angra dos Reis completed upgrades work on the semi-submersibles Noble Paul Wolff and Noble Dave Beard and secured $304m contracts for the drillships Noble Leo Segerius and Noble Roger Eason.
At the same time, Aker Floating Production’s tanker-to-FPSO upgrade conversions continue unabated, preparing for their rising future use predicted by CEO Arne Hygen Tørnkvist.
Developments in subsea technologies also promise much, for example, in the deepwater upgrade project in the Lobito Tomboco field, offshore Angola, GE Oil and Gas used the latest VetcoGray choke-interface technology to retrofit existing subsea trees – establishing a world-first for the application of any retrofit technology to deepwater scale-squeeze. Having been extended to 1,850ft already, plans are afoot to go further, looking to bring the accompanying benefits of increased productivity down to 3,500ft for similar applications in the region.
It seems that Lightman’s talk of squeezing out every drop is beginning to look achievable, especially given the progress on what he calls the new frontiers of innovation designed to help elucidate the geology and enable ever-more elusive reserves to be reached.
Subsea, ultrasonic inspection, 3D imaging and 4D seismic technologies are already established in this respect and more developments will follow in the wider arena, but in the long-run Lightman believes that “it will be how you go about harnessing them that will be key”.