
ATEX (ATmosphères EXplosible) is a legislative process that started with the implementation of ATEX 95 in July 2003.
It is a series of European Union legal requirements for manufacturers of equipment that is designed to operate in potentially explosive environments.
The latest part of the legislation, ATEX 137, which was introduced in July 2006, applies to users of equipment, plant operators or any plant operator handling or processing potentially explosive dusts or vapours.
The requirements involve an assessment of all areas of a process plant to determine their classification. In addition, all existing equipment has to be assessed to check if it is suitable, and all new equipment must comply with ATEX 137 standards.
This is especially relevant to the oil and gas industry, which, by its very nature, is exposed to explosive vapours and gases.
HARMONISATION, NOT REVOLUTION
How well do you really know your competitors?
Access the most comprehensive Company Profiles on the market, powered by GlobalData. Save hours of research. Gain competitive edge.
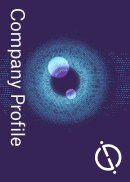
Thank you!
Your download email will arrive shortly
Not ready to buy yet? Download a free sample
We are confident about the unique quality of our Company Profiles. However, we want you to make the most beneficial decision for your business, so we offer a free sample that you can download by submitting the below form
By GlobalDataThe oil and gas industry has not found any problems with implementing the new directive as it already had a very high standard of safety and in general operated in accordance with ATEX. In fact, the new regulations are not very different from the standards in operation before.
ATEX actually represents a harmonisation of standards across the EU so that all countries have identical standards. The UK Health and Safety Executive explains: "The aim of Directive 94/9/EC is to allow the free trade of ATEX equipment and protective systems within the EU by removing the need for separate testing and documentation for each member state."
DEFINING AN EXPLOSIVE AREA
For an area to qualify as a potentially explosive atmosphere it must contain a flammable substance and air, and be under atmospheric conditions. An explosive environment includes anywhere that liquid fuels, flammable gases and explosives are stored or used.
Explosions can also occur under less obvious conditions, such as
where there is a lot of dust or particles suspended in the air.
Most explosions are initiated by a spark and when electronic
equipment is used in a volatile environment the risk of explosion is increased. Switches, circuitry and motors all have the potential to create sparks. Wherever a circuit is broken or is close to being reconnected, electric currents can arc through the air.
Static electricity, which can be built up by walking on a carpet, for example, and then discharged by touching a conductive surface, can cause a spark. Sparks can also occur when metallic surfaces hit each other. All these factors must be taken into consideration during any ATEX audit/risk assessment or when ordering equipment or setting up new facilities.
ATEX covers the full range of electrical and mechanical equipment, including communication radios, electrical motors, industrial-standard computer control systems, diesel engines, valves and mechanical plant.
ATEX is based on the requirements of two European directives. The first, which has been in force since July 2006, is Directive 99/92/EC (also known as ATEX 137 or the ATEX Workplace Directive), setting out the minimum requirements for improving the health and safety protection of workers potentially at risk from explosive atmospheres.
The second, which has been in force since July 2006, is Directive 94/9/EC (also known as ATEX 95 or the ATEX Equipment Directive).
This directive harmonises the laws of different EU member states concerning equipment and protective systems intended for use in potentially explosive atmospheres.
ENSURING EQUIPMENT SAFETY
ATEX 95 defines the health and safety requirements for all mechanical and electrical equipment in hazardous areas. This is mainly for the benefit of manufacturers. These standards were established as categories 1, 2 and 3, with Category 1 being the safest for potentially explosive environments.
The further introduction of ATEX 137 has now established the standards for the end user in order to protect workers, which defines zones relating to the potential for an explosive atmosphere.
Equipment certification must also include a gas grouping (Type I methane to Type II a, b or c), an ignition temperature coding (T1 to T6), a protection concept and an ambient temperature range of operation (usually between -40°C and +50°C).
It is expected that this certification coding will be applied to all equipment intended for use in explosive atmospheres, whether electrical or mechanical, and also to protective systems. Manufacturers, suppliers and importers have a duty to ensure that products meet health and safety requirements and undergo appropriate conformity procedures.
IT EQUIPMENT FOR THE OIL INDUSTRY
Since 1 July 2003, when the first ATEX directive (ATEX 95) came into effect, the control and safety devices for all types of electrical and non-electrical equipment that are used in potentially explosive atmospheres have had to satisfy the requirements.
ATEX 95 was a new-approach directive for CE Marking and replaced three old directives. Deployment of IT technology in locations with explosive atmospheres has been on the increase and there has been a growing need for IT and communications equipment that complies with the ATEX directive.
Several IT companies have launched compliant computing equipment, including Kontron, a market leader in embedded standard and custom computer solutions, and Panasonic, manufacturer of one of the oil and gas industry’s most popular notebooks.
Shortly before ATEX 137 became mandatory, Kontron announced that it had produced the highest class certified computing display for the oil and gas industry for use in hazardous areas, the Triton D1. It carries the Class I, Zone I, Ex d IIB T4 and Class I, Zone l, AEx d IIB T4 certifications in the USA and Canada, and the ATEX II 2 G, EEx d IIB T4 certificate in Europe.
It has a modular construction with a flameproof, all-machined, aluminium enclosure and a 15in screen viewable in sunlight with enhanced infrared touch-screen technology featuring false-trigger intelligence.
Meanwhile, Panasonic’s popular CF-18 Toughbook has been ATEX Directive 94/9/EC compliant since May 2004. As part of the design process, Panasonic commissioned TÜV Rheinland to conduct ATEX directive conformity assessments to assist the development of a notebook PC suitable for Zone 2 (Category 3) explosive atmospheres.
Following a mutually beneficial collaboration, Panasonic was able to produce a laptop meeting the new safety requirements.
Speaking about the exercise, Toshiyuki Takagi, general manager of the technology centre at Panasonic’s IT products division, says: "Through our work with the TÜV Rheinland inspectors, we acquired further know-how on the process of certification."
Inspector Rath of TÜV Rheinland Japan, who guided the evaluation process, adds: "It was an interesting and challenging task to combine all the required expertise of Panasonic and TÜV personnel to satisfy the numerous requirements of the ATEX directive."
EFFECT ON THE INDUSTRY
Terry Robinson, tendering systems team leader for AMOT Controls
(systems division), which designs, fabricates and supplies control systems for hazardous areas, says the new directive has not had a major impact on the industry because it represents a harmonisation of existing standards rather than a whole new system.
He believes that the main misconception about the new directive is that is a new standard. "It is not a standard; it is a group of EU directives to rationalise legislation and increase the harmonisation of equipment sales across the EU so that a UK company, for example, can purchase equipment from Germany, for instance, without worrying about different standards."
He continues: "In general, the new ATEX directives are intended to increase awareness of safety across a wide range of industries so the design of plant and equipment can consider the workers, the environment and the plant itself for use inside explosive atmospheres."
He believes that this has not had a major impact on the oil and gas industry as it was already "very aware of these hazards and has acted accordingly in relation to the ATEX directives."
However, equipment manufacturers have had to make sure that they are ATEX compliant and have the certification to prove it. Robinson says: "There has been a drive for the last three years to bring equipment into line with the ATEX directives."
Although it is only valid in the EU, there have been increasing demands for ATEX products and equipment from oil and gas companies based all over the world, including South Australia, Saudi Arabia and South America, which is an indication of how highly ATEX is regarded.
Robinson explains: "The USA and Canada have a similar system to ATEX but use divisions instead of zones. US companies have now established the use of zones in their coding to be compliant with ATEX and are therefore able to sell products and equipment to EU end users."
He believes that if ATEX has had any discernible effect on manufacturers, it has been a positive one. Sales to the oil and gas industry have been stimulated by the need to replace old equipment that no longer meets the standards.
As with any industrial legislation, implementation is only successful if the industry is properly educated about it. As the oil and gas industry was already well versed in the safety of personnel and equipment, the establishment of ATEX 137 to rationalise standards across the EU is unlikely to present major long-term problems.