
The oil and gas industry has grown accustomed to the use of systems controlled remotely by expert operators. But now projects that are underfoot could turn remotely operated vessels (ROVs) into highly specialised robotic systems.
The industry is now to decide whether the use of robotics in subsea environments is inevitable and, if so, how much it will cost.
Robots have clear advantages in some applications and safety is often a big factor in favouring their use in hazardous environments.
“They take away the dull, dirty and tiring work,” says Erik Kyrkjebø, research scientist at SINTEF Applied Cybernetics. “I am optimistic about the place of robotics in the oil and gas industries. There are so many tasks robots could do easily, far beyond inspection and maintenance. Now the challenge is to get oil and gas companies to use robots.”
SINTEF is working with Norwegian energy producer StatoilHydro on a new concept for a remotely operated offshore platform. The robotic lab facility in Trondheim is now developing intelligent and reliable robotic and instrumentation systems that will enable onshore operators to monitor and control all of the platform’s processes.
“Our project is about reducing the cost and time for a new platform. There would be no sleeping quarters and no security equipment for personnel, for instance, so it would take away some of the small costs. Our motivation is to keep capital investment and operating costs down,” explains Kyrkjebø.
How well do you really know your competitors?
Access the most comprehensive Company Profiles on the market, powered by GlobalData. Save hours of research. Gain competitive edge.
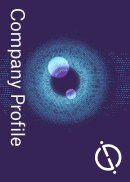
Thank you!
Your download email will arrive shortly
Not ready to buy yet? Download a free sample
We are confident about the unique quality of our Company Profiles. However, we want you to make the most beneficial decision for your business, so we offer a free sample that you can download by submitting the below form
By GlobalDataLarge modular process sections would form an unmanned area of the platform, where robotic manipulators and a large gantry crane would move the sections.
“We’re not looking at robotics in terms of the rigs that we have. We won’t install robots to replace humans out there, we are looking at the concept for our ROVs. Subsea formations are relatively expensive, time consuming and less effective in terms of recovery. We wanted to challenge the way robots are used by having them under the sea, not floating on the surface,” says Anders Røyrøy, production facilities researcher at the Bergen Research Centre of StatoilHydro. The centre is currently working on long-term research with SINTEF, and on short-term development of offshore applications with ABB Robotics.
Investing for the long term
While StatoilHydro’s work shows that the oil and gas sector is waking up to the potential for robotics to improve offshore operations, the industry as a whole seems happy to view it as a long-term trend that will have a gradual rather than a sudden effect.
“I’m not sure how eager oil and gas companies are to introduce robotic technology,” says Kyrkjebø. “They will take some warming up to the concept. They need to see that robots are safe and will take away the tasks that humans would rather not do.”
Similar systems are nevertheless already at work in remote, hazardous environments.
“We don’t call it robotics, but in a lot of operations where we use pipes for drilling we use manipulators that could be called robots,” observes Røyrøy.
In some areas the shift towards more widespread use of robotics has already begun and is taking place in less dramatic ways. In underwater installations operators are familiar with remotely controlled systems in production facilities, or with ROVs.
There are, however, different modes of control, so a step up in skills will be needed to get the most out of robotic systems.
Automatic control is simple and once the robot is programmed it will perform repetitive tasks efficiently. Kyrkjebø believes systems for this control mode are well advanced. A higher level of control enables a robot to to perform an action, such as closing a valve or changing a battery in a wireless sensor, based on current sensor information. Here, more work is needed to ensure the control systems give enough feedback, especially in terms of visual
information.
The final mode puts operators in direct control of a robotic system, probably using a joystick, so force feedback information is important. There are many parallels with telesurgery, where detailed feedback on sound, visuals, touch, temperature and other parameters is crucial if the robot is to act as the operator’s extended arm.
“ROV operators are highly trained and experienced. Now they need to let more actions be done automatically by robots. Instead of controlling them directly they could simply choose an operation from a menu. The operator should be an oil and gas expert, not a robotics expert,” says Kyrkjebø.
The battle for hearts and minds
One challenge that robotics companies face in selling to the oil and gas industry is the capability of the technology, but the proven resilience and performance standard allays many concerns in this regard. Cost, however, could be a more difficult hurdle to overcome. After all, the demands of the oil and gas industry are different from those in sectors where large numbers of identical robots have been successfully deployed.
“There must be a business case for investing in robots. The robotics industry would not be working with us if they did not see the oil and gas sector as a market, but it is not like making cars or any other kind of serial production. Our industry needs very specialised robots, which raises the question of price,” says Røyrøy.
“We are looking at whether we can find a more generic layer of work for robots to do, but we must also work on how we can access the areas in which robots will work. By 2015, we will have the ability to have a robot working offshore. But this won’t happen until we have changed our installations, which means they are likely to be on new platforms only,” he adds.
If cost and capability concerns can successfully be overcome, the future of robotics in oil and gas production will then depend on how fast the industry can make a cultural shift.
“Robots are aiding humans, not replacing them. People are needed for spontaneous decisions and actions,” says Kyrkjebø. “The automotive sector is used to robots and happy with what they do. People’s jobs don’t go away, they change. They become more about using know-how.”
He adds: “In the oil and gas sector, we need to ease in robotics, using them onshore first and in simple operations. We can develop through that and move into the offshore production process, where we can show workers that robots are a help. They take the heavy weight but people are in control.”
Robots clearly have a role to play. And although they may initially play the part of janitor, they have good prospects for promotion.
“We foresee that robots will do inspection and maintenance work but there is a trade-off between installing a robot and how robust that robot is in terms of its own maintenance needs. If robots can take away dangerous work in a specific application then we would look at a case study. We need to do more work with our research centre and with robot vendors, but I am optimistic about the future of robotics in this industry,” add Røyrøy.
Much depends on the willingness of producers to invest in long-term development but subsea operations are set to have a growing robotic element in the years ahead. How scalable their use is, however, comes down to how well they can prove the viability of their existence.