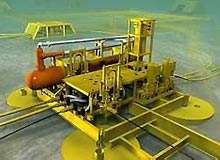
When Aker Solutions’s senior vice president of trees, processing and boosting Svenn Ivar Fure announced in May that his company was to increase production of its RapidSolution well set programme, it highlighted in microcosm the phenomena gripping the subsea industry right now: growth.
“We passed this year’s ambitions for sales of RapidSolution trees as early as April,” Fure said. Since we so far have managed to sell the well sets in progress before touching our six-month delivery objective, we have decided to expand the programme both in size and product offering.”
Aker Solutions is not alone. In the UK, one of the world’s leading subsea sectors, revenue grew by almost 30% to £4.3bn in 2007. Overall, the market forecast expenditure for the subsea industry is set to rise from a total of $18.6bn in the period 1999–2003 to $68bn between 2006-10.
So what’s driving the growth? What benefits does subsea production bring? And how long can the growth continue?
WHY NOW?
Subsea technology has been around since the 1960s but it has only really taken off as a viable form of oil production over the last few years.
“All the pieces of the puzzle have fallen into place over the last few years,” says Will Rowley, director of analytical services at Infield Systems. “Technology has developed and become cheaper which, coinciding as it has with a need to go into deeper waters for oil, has contributed to the phenomenal growth in subsea production.”
SUBSEA DEMAND
When they announced their first-quarter results in April 2005 Siem Offshore, who three months later became Subsea 7, cited ‘robust oil and natural gas prices’ as one of the key drivers behind global subsea expenditure. Oil has since rocketed to a record $135 a barrel, reflecting the fact that it is becoming increasingly difficult to source. The solution? Subsea.
“There is no more easy oil,” Shell Europe’s vice chairman of exploration Paul Botts told delegates at Subsea 08 in February. “And the subsea industry is critical to unlocking more oil to meet world supply.”
ISSUES OF SUPPLY
Technical barriers, the high cost of building and installing the right systems and difficulties with integrating them into existing infrastructure on the sea floor held subsea production back for years. However, the demand for more oil driven by high commodity prices, rising water production from mature fields and increasing surface facility costs have combined with advances in technology to push oil extraction onto the seabed.
Now, companies like Aker Kvaerner, Baker Hughes, FMC Technologies, Petrobras and ABB are producing equipment that allows oil companies to carry out subsea separation and boosting without such high risk and cost implications.
“The limited access to oil in places like the Middle East has forced companies to look further a field,” says Simon Wardell, director of the global energy markets group at Global Insight.
“As they have moved into deeper waters and less hospitable conditions to look for oil, suppliers have been given the incentive to produce the equipment to meet those needs. It’s a virtuous circle.”
ECONOMIC BENEFITS
Not only does subsea equipment compare favourably with surface facilities in terms of initial outlay, it also offers potential economic benefits once in operation. The separating and pressure boosting technology of subsea production allows users to dramatically reduce expenditure on offshore platforms and, it is anticipated, may one day remove the need for offshore platforms entirely.
“It is possible,” says Simon Wardell. “There’s definitely a move away from these heavy, costly structures stuck out in the middle of the sea. I doubt if its something we’ll see in the immediate future but things are certainly going in that direction.”
PRODUCTIVITY BENEFITS
Statoil Hydro and FMC Technologies have developed an oil recovery project at Tordis Field that will showcase full subsea production for the first time. By moving operations to the sea floor, Statoil expects Tordis’s recovery factor to increase from 49% to 55%, adding 15-17 years onto the life of the field and enabling the company to extract an extra 35 million barrels of oil.
“By using this technology, you can exploit an oilfield much deeper – so, for instance, you can recover 5% to 10% more from the original reserves, an enormous advantage,” says Toine Hendriks, senior process engineer at CDS Engineering, who led the project to build the subsea separator used at Tordis.
“It is also expected that this technology will facilitate new oil field developments in deeper and more remote areas, an advantage for the future as most of the easy accessible oil has already been produced.”
ENVIRONMENTAL BENEFITS
In June 2007 the separator used at Tordis scooped a EUREKA award for its outstanding environmental benefits. The separator ensures that residual oil droplets are discharged into separate subsea wells instead of the sea. If adopted across the industry, this kind of technology can make sure subsea continues to contribute towards a greener oil output.
“As far as I am aware discharges from subsea production are negligible,” says Will Rowley. “It’s a safe technology and in addition, it reduces the amount of infrastructure you need, so it has a knock-on effect to the environment there too.”
CHALLENGES
Traditionally, oil companies have been reluctant to adopt subsea technology driven by fears over costs and operational robustness, namely: if machinery goes wrong so far underwater how much will it cost to fix? How long will it take? And how much will it cost in lost revenue from downtime?
Suppliers have worked hard to overcome these challenges, none more so than DES operations, who developed the multiple application reinjection system (MARS). Now owned by Cameron, MARS acts as a universal interface allowing subsea production equipment to be installed without field shutdown. It is currently being used by Shell in the North Sea, BP King in the Gulf of Mexico and Total in West Africa.
“Flexible plug-and-play subsea processing has long been the Holy Grail of the oil and gas industry,” says DES managing director Ian Donald. “With MARS, operators now have a simple, low-risk, low-cost method of achieving this.”
OFFSHORE OUTLOOK
With commodity prices showing no signs of abating, subsea’s ability to increase the life of existing wells and the potential to help exploit other reserves such as lower tertiary trends, the outlook for the industry is very strong. Infield Energy Analysts predicts a 65% increase in spending on the global subsea market between 2008 and 2012, with $106bn being spent in that time. They also predict a 60% growth in the number of wells, from 1,467 in the period 2003-07 to 2,408 between 2008-12.
“Spending will go up because companies are investing more offshore and the costs are higher, so they take up a larger part of the budget,” says Simon Wardell. “The competition between IOCs and NOCs is fierce where it is open. But it is not open in many places, which is forcing the IOCs to look for new drilling sources in less hospitable places.
“Because of this, the future looks good for subsea. It’s hard to see IOCs not investing further. More money will bring further developments which will generate experience and lower costs, which will provide more incentive to use subsea methods in the future.”