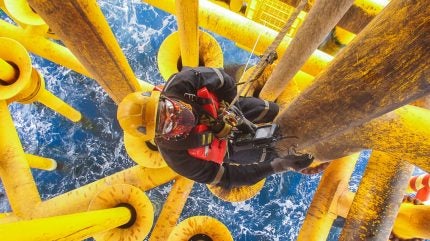
From wind turbines receiving cargo by drone to unmanned drilling rigs producing oil, offshore operations are being automated.
For geotechnical exploration vessels, retrofitting automation solutions one at a time can help companies enhance safety and stay competitive, says Laurie Thornton, director of specialist offshore engineering firm, MintMech.
In marine construction, developments require various foundations and preparation of the seabed, depending on what’s down there. Whether building a bridge, installing a wind turbine or deploying a mooring station for an offshore platform, success depends on a good understanding of the seabed.
The geotechnical exploration phase of a project is crucial to gaining this understanding.
Accurate and efficient site investigation (SI) is crucial to avoid overlooking potential issues in the seabed’s composition because undetected problems can significantly escalate project costs. In extreme cases – when a project is already well underway – the ramifications of unexpected issues can be two or three times the planned total project cost.
Alternatively, an under-specified or poorly executed site investigation could misrepresent the site’s stratigraphy. If the seabed is competent, but incorrectly reported to be weathered or otherwise fractured, developers might over-engineer the foundations. Over-specifying solutions leads to more money and time spent and lower margins, so designers need to know exactly what’s down there.
Quality at the core
Core samples are the foundation of a site investigation. Better cores lead to a deeper understanding of the seabed, and with better understanding comes reduced project risk. Achieving this quality depends heavily on the drilling process, with several key factors that drilling teams must constantly manage to obtain reliable core samples. For example, contending with heave from swell.
Automating to mitigate against these factors can free up labour and greatly improve both quality and consistency of cores. Cores may represent the only physical deliverable or product from a site investigation. They may be stored, referenced and retested for decades, so the industry’s focus on true representation of the stratigraphy cannot be undervalued.
While various technologies have significantly improved the ability to manage heave motion, it remains a critical consideration in offshore operations.
Traditional passive heave compensation (PHC) systems use a pneumatic spring to stabilise the drill string but require a reaction force from the seabed – weight on bit – to properly counteract vessel motion. When the seabed geology is soft or the drill bit is not touching the seabed, this reaction force is lost, causing the PHC to stop compensating for vessel motion.
AWOB and WOBs
By retrofitting automated active heave compensation (AHA/AHC) systems, whereby the drill position is no longer dependent on the seabed reaction force, the drill bit position can be controlled, regardless of the ground conditions improving both quality and consistency of cores.
Similarly, the ability to maintain the drill bit position when the drill bit is not touching the seabed improves borehole stability during downhole tool changeovers.
Minimising heave motion is important because the vertical motion increases the risk of inconsistent weight on bit (WOB) – a critical variable while drilling. If WOB is too high, the driller risks damaging the bit, deforming the drill string or crushing the formation and reducing core quality, especially when working with soft or fractured geologies.
Excessive WOB can also stress drilling equipment, leading to higher maintenance costs and operational inefficiencies.
Conversely, If WOB is too low, penetration rate will drop, the bit might bounce and hole cleaning might be impacted as smaller cuttings are not flushed out. WOB is traditionally reported via a weight gauge on the driller’s console, but ensuring accuracy requires non-stop monitoring, which is labour intensive.
An automated weight on bit (AWOB) system immediately removes this variability. The driller uses their field experience to determine the appropriate WOB for the situation, then sets the AWOB to a specific target value which it will not exceed, 2.1 tonnes for example.
An AWOB system not only frees up the driller’s attention for other dynamic variables, but also improves the consistency of the core by maintaining constant WOB throughout its length.
Tool handling
Traditionally, tooling is brought up to the rooster box and manually moved to drill centre by a crew member “manriding” in the rooster box.
Doing so is potentially dangerous because of the stored energy in such platforms – even a near miss forces operations to stop while the issue is investigated.
Using an automated tool handler arm to manoeuvre tooling from the deck to above drill centre for deployment eliminates the risk of human error and injury, ensuring operations run safely and smoothly.

The handler can even be remotely controlled from a sealed cabin on deck, further protecting the operator from the elements. Some retrofittable remote tool handlers can simply be installed with brackets and bolts, rather than welded, negating the extra cost, risk and licensing requirements of hot work.
This also reduces time in port between swings, as no third-party contractors are necessary, and the operation doesn’t impact normal mobilisation.
Tripping pipe
The roughneck is an iconic symbol of the oil drilling industry. Viral videos showing roughnecks throwing manual tongs to manually trip sections of drill pipe show how risky the job is, and their signature full-brim hardhats show that hazards can come from any direction.
Automating drill pipe tripping would eliminate risks to crew, as well as extending the potential duration of operation.
For example, the power swivel or spinner assembly can screw or unscrew the pipe, then an automated iron roughneck can torque the joint. This keeps crew out of the line of fire, reducing the risks of injury and downtime.
The automated process is also more repeatable, and torque values can be relied upon. It may be slightly slower, but depths tend to be shallower than the deep- and ultra deep-water of oil and gas projects, so fewer joints are required. However, the risk and consequences of a dropped pipe can be just as damaging, making the reliability and safety of the system critical.

The cultural shift witnessed over the last few decades has resulted in technical performance and productivity no longer being the primary focus of clients and contractors alike, instead safety culture, statistics and mitigations are the leading key performance indicators (KPIs) across industry.
Clearly demonstrating continued reduction of risk to life and project cost has become a primary driver for developers considering contractors.
Oil money
In oil and gas, automation is well established. The world’s first fully automated oil and gas platform, Oseberg H, was launched in Norway in 2018. Oseberg H is controlled entirely remotely and has no crew quarters, not even a toilet. The project cost about £600 million and will produce up to 110 million barrels of oil at around $20 per barrel for the next two or three decades.
But budgets are smaller in renewables. Global capital expenditure on offshore wind, for instance, is estimated to be ten times lower than on oil and gas – roughly $50 billion compared to $500 billion. Where budgets are tighter, gradual retrofitting is likely a more viable method for creating fit-for-purpose geotechnical exploration vessels.
The industry needs a safe, reliable and agile geotech fleet if it is to meet the UK Government’s ambitious target of achieving 55GW of wind power generation by 2030.
Updating legacy equipment by automating processes one at a time not only helps firms comply with today’s increasingly stringent health and safety regulations, but also increases production capability by boosting the quality of their core samples, expanding their operational periods and making their tenders more competitive.
As power electronics, control systems and computer intelligence become cheaper, automation becomes more cost-effective and accessible. And 2023 saw the first unmanned HVDC platform at Dogger Bank, and we will likely continue to see automation adopted into the industry, not only for safety and cost but also for operational efficiency.
Who knows, in a few years offshore marine drilling teams might be able to work from home.