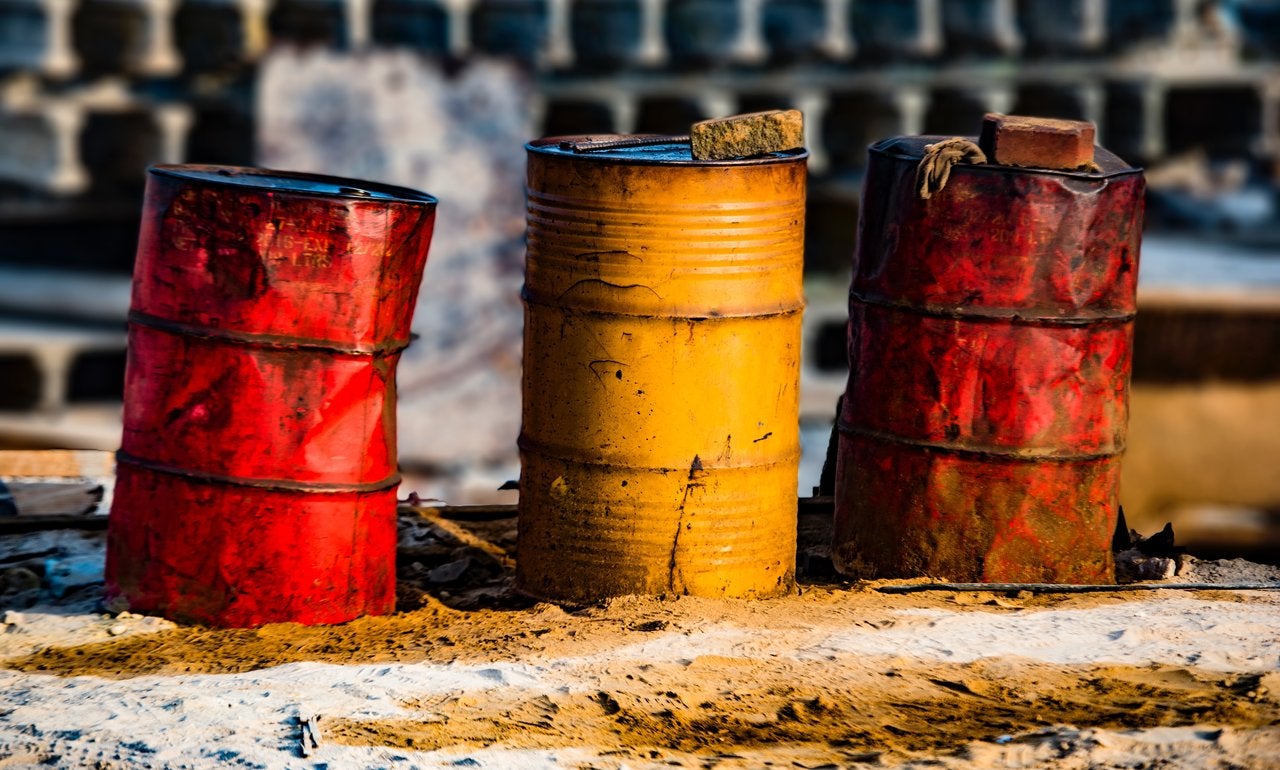
Oilfield reservoir souring is a complex and potentially costly phenomenon, which leads to the production of sour crude. ‘Sour’ refers to oil containing high levels of the impurity hydrogen sulphide (H2S), typically more than 0.5% of the oil’s composition, and the term is interchangeable with sulphide, or ‘bad egg’ gas, so called because it smells of rotten eggs.
The cause of oilfield reservoir souring can be identified in the microbiology of a drilled well downhole. In order to retrieve oil from underground, water (typically seawater) is pumped into the well, which sits beneath the oil. When the oil is pumped out, it is replaced by the water so that the overall reservoir pressure is maintained. However, the seawater contains sulphate and supports a population of sulphate-reducing bacteria, which thrive in an anaerobic environment such as an underground oil well, living off the sulphate and converting it to H2¬S.
“The very bacteria that are in muddy waters like ponds and ditches are the same bacteria that get injected into the oil reservoirs. And these bacteria, known as the sulphate-reducing bacteria, are the ones that generate H2S around the near well bore in oil reservoirs,” says Rawwater managing director and founder Dr Bob Eden.
As well as the increased costs of treating sour oil before it can be turned into things like petrol, H2S is highly corrosive. Sulphide can eat away at the metal parts of an offshore oil platform, damaging the topsides at great cost to the operator.
This is where Rawwater comes in. The company uses its large collection of data to predict the extent to which a company’s oil will sour.
Explaining the chemistry behind Rawwater
While Eden’s own research into oilfield souring began in 1987 at the University of Manchester Institute of Science and Technology (UMIST), Rawwater’s laboratory investigations into oilfield souring started in 2004 with one bioreactor.
“We were looking at the effect of corrosion on feeding the bacteria,” says Eden. “With steel under anaerobic conditions you generate hydrogen from the corrosion process. And so our first bioreactor at Rawwater was looking at anaerobic corrosion, hydrogen production, and the role that corrosion plays in feeding the bacteria around the near well bore.”
The team at Rawwater now have more than 30 pressurised bioreactors in which to simulate the physical, biological and chemical conditions that you find in an oilfield reservoir. The reason that Rawwater uses pressurised bioreactors, as opposed to serum bottles – the traditional method used in the industry – is to get as close to these real-life conditions as possible.
“In bottles, the pressure is very low pressure – atmospheric pressure typically – and what we’ve discovered is that the bacteria, which thrive in our pressurised bioreactors, are a different make up of those that thrive in bottles. So, if you really want to study what is going on inside an oil reservoir, let’s try and get as close as we can to oil reservoir conditions,” explains Eden.
“And that means the right pressure, the right temperature and the right flow rate. If a bioscience company is attempting to control these bacteria in the reservoirs, they ought to be controlling the right bacteria, and not the wrong bacteria.”
The findings are then entered into the computer modelling software Dynamic TVS (Thermal Viability Shell), which uses the data to forecast the propensity of a particular oilfield to turn sour.
“What we have observed is that the oil in our bioreactors supports souring to different degrees,” says Eden. “What we do is we identify from our client’s fields whether we have got oil that is going to turn sour or not turn sour, and it is that information that we plug into the Dynamic TVS to help with forecasting oilfield souring against time.
“So with oil that is going to go very sour over a ten or twenty year period, we will have a souring profile, which could produce H2S in the gas phase of the produced gas in the thousands or even tens of thousands parts per million by volume. Whereas oil that is not going to go sour, you might find over a long period of time very little H2S comes up.”
Three decades of bacteria in a unique biofilm
Rawwater has been sub-culturing bacteria and collecting data since Eden’s work at UMIST, and now has over three decades of bacteria in its consortium, known as biofilm.
“Our biofilm is actually 31 years old. So it is a well-established and actually unique biofilm. Nobody has a biofilm like our biofilm – a strange claim isn’t it?” Eden jokes.
“We have been sub-culturing since 1987 and what we have been doing over these past three decades is adding additional bacteria to that consortium to create a consortium that looks very much like the kind that you would get out of an oil reservoir. So in other words, we will make it biologically realistic, not just the physics but also the biology and the chemistry.”
While getting the conditions 100% identical is practically impossible, Rawwater can get very close to mimicking the conditions you would find in a real oilfield.
“Chances are we would not be able to use their rock because in an oil reservoir the rock is porous,” explains Eden. “Getting hold of rock samples from oil reservoirs is very difficult, so we use sand. We use the oil company’s oil; we use their pressure, and their temperature. But we use our sand and our bacterial population.
Saving oil companies time and money
The data on microbiological souring is useful for oil companies, which may have to spend huge amounts of money on anti-souring plants and chemicals to try and mitigate the damage caused by sulphide.
“The reason why it is important to know it’s not going to go sour is it saves the oil companies from injecting very expensive anti-souring chemicals. So clearly, if we can say ‘this reservoir is not going to go sour’, then oil companies are saving millions of pounds in chemistry.”
In September 2018, Rawwater did exactly that, using its considerable reservoir souring data to help an oilfield operator avoid spending more than $100m on a new anti-souring plant. The client, based in West Africa, conducted a souring forecast with Rawwater and found that its field would not “support significant biological souring as a result of the physics downhole,” according to Matt Streets, senior project officer at Rawwater. “We found that the downhole conditions are too extreme for bacteria to survive and really thrive to generate sulphide.”
The client then asked Rawwater to conduct a laboratory experiment to show that this was in fact the case.
“So we were able to run some pressurised bio-reactors, which confirmed the result of the souring forecast. We had low pressure and low temperature bioreactors; and high pressure and high temperature bioreactors and we were able to confirm that it is really the downhole physical conditions those pressure/temperature conditions, which mitigated sulphide production. And so [with] the combination of our pressurised bioreactors and our forecasting tool, the client felt confident that what they had in place was sufficient,” says Streets.
“Part of the story is that another company was trying to sell them a sulphate removal plant, and what that does is strip out the sulphate in your seawater prior to injection. Obviously, if you take away the sulphate you can’t have sulphate-reduction taking place downhole by the bacteria, and so they would have unnecessarily purchased a $100m unit, which wasn’t actually required for souring control alone.”
Recently, Rawwater commenced a £1m project called the Seriatim Programme, now at Seriatim 5, which will add another 100 years’ worth of data to the already considerable database.
“What that means is whenever we come across anything strange out in the field, chances are we have got something similar that we have researched in the laboratory,” says Eden.
“And we go back through the data in that big database and see how close it is to what’s happening in the field and that gives us the opportunity to make recommendations based upon real findings rather than scientific guesswork.”