
There is a global trend emerging among petroleum companies in that they are integrating their upstream and downstream businesses to add value to their hydrocarbons, a move which was unheard of in the 1970s and 80s.
Indeed, the chemicals sector, which was once disconnected from the oil industry, is now seen as a vital player in enhancing oil recovery, at a time when the Organisation of Petroleum Exporting Countries expects demand from developing countries to increase global production to 107 million barrels a day by 2030.
When an oil field reaches the end of its normal life, as much as two-thirds of oil is often left in the ground because it is deemed two expensive or too difficult to retrieve after primary and secondary recovery has declined.
It is estimated that by recovering just 1% of this forgotten oil throughout the world, the equivalent of 20 to 30 billion barrels of oil would be available. What’s more, the Society of Petroleum Engineers believes that 150 billion barrels of the black stuff is accessible through chemical formulas made up of surfactants, which are able to lower the surface tension of oil.
Chemically enhanced oil recovery (cEOR) methods are growing in popularity, but how do these processes compare to more common tertiary techniques, such as gas injection, and how do they work to retrieve the maximum amount of oil from a well?
EOR techniques
Once primary recovery methods – using natural pressure and pressure maintenance – and secondary recovery techniques – using water displacement – have been applied, tertiary recovery or EOR is relied upon to encourage the flow of trapped oil inside the rock. This can be achieved through the injection of gas, steam and chemicals.
How well do you really know your competitors?
Access the most comprehensive Company Profiles on the market, powered by GlobalData. Save hours of research. Gain competitive edge.
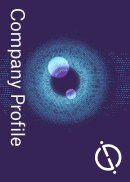
Thank you!
Your download email will arrive shortly
Not ready to buy yet? Download a free sample
We are confident about the unique quality of our Company Profiles. However, we want you to make the most beneficial decision for your business, so we offer a free sample that you can download by submitting the below form
By GlobalDataEnergy giant Shell was one of the pioneers in injecting naturally produced CO2 to boost oil recovery from the Permian Basin in Texas, the US, in the 1970s. Robert Moene, technical programme manager for cEOR at Shell Global Solutions explains how this method works: "Injecting gases that can dissolve in oil into a reservoir creates a mixture that flows more easily through the reservoir to production wells.
"We plan to use contaminated natural gas produced with oil in a project at Harweel in Oman. Here, a gas rich in hydrogen sulphide will be re-injected into the reservoir to force out more oil. Using this approach we hope to recover up to 50% of the oil, compared to 10% using conventional production methods."
The thermal EOR method incorporates steam which, when injected, heats the oil in a reservoir, thinning it and making it easier to produce. It also pushes the oil to wells where it can be better drawn to the surface.
In chemical EOR, the oil reservoir is flooded with a mixture of water and a small percentage of surfactants and polymers to enable oil droplets, which are trapped in pores to move and be collected. The oil and water mixture is then pumped out of the ground and separated.
Increasing value of cEOR
In the past, cEOR focused on micellar flooding with 2-12% surfactant, which cost around $20 to $75 for each barrel injected, Kon Wyatt, vice president of engineering at Surtek, told the American Oil and Gas Reporter.
New surfactant formulations, however, are made up of 0.3-1% of surfactant(s) and can range between $10 to $15 a barrel of incremental oil.
No wonder companies like Shell Chemicals and Oil Chem Technologies are attracting more and more customers eager to find out information about their EOR product lines.
The reason for this drop in price comes down to the fact that chemical companies know how to vary their molecular structures to work as efficiently, if not more efficiently, than before.
Moene said: "Shell’s ENORDET surfactants have been developed specifically for enhanced oil recovery and can be selected and matched to meet the specific reservoir conditions – including its temperature, water salinity and hardness, and the crude oil type.
"We have also been seeking to develop the most effective formulations, surfactants and accompanying surfactant manufacturing processes with the aim of improving efficiency, and above all, to reduce costs for the customers."
Proven capability
Shell Chemicals has proved the performance of its ENORDET surfactants in years of extensive laboratory testing.
During a lab tour in Amsterdam in October 2011, the company demonstrated to reporters how its formula was able to flush out oil trapped inside a thin sheet of glass, which was heated to mimic temperatures found in an underground reservoir and coated in a fog-free film.
The whole EOR process was then scanned onto a computer so Shell could understand the behaviour and characteristics of the surfactant molecules when reacting with oil.
Shell’s ENORDET surfactants are typically made up of anionic surfactants, which overcome natural capillary forces by reducing interfacial tension, and a polymer (0.1-0.3 concentration) to increase water viscosity in order to improve sweep and mobility control.
Alkali – typically sodium bicarbonate – is often added to the mix to help increase efficiency.
The firm has a number of surfactant molecules, including alcohol alkoxy sulfates and internal olefin sulphonates. The former is restricted to reservoirs with temperatures below 60°C, while sulfonates can operate in temperatures up to 140°C.
In the final stage of lab-testing, core flow analysis was carried out to evaluate the performance of EOR suractants in conditions that are as close as possible to a real reservoir. The tests were carried out with baseline sandstone samples and rock cores taken from oilfield drilling rigs.
Core samples were cleaned and saturated with oil taken from the reservoir and flooded with water containing surfactant.
By 2009, Shell Chemicals was at the stage of conducting single well tests and, following successful trials, it is now developing projects for large-scale multiwell pilots in the Middle East, Russia and Asia.
Moene said: "The single well tests were all successful in proving that ENORDET surfactants were able to mobilise the remaining oil in the reservoirs that were being targeted. We found we have proven capability to produce ENORDET surfactants on a commercial scale, including the capability to transport these new molecules according to relevant HSSE requirements.
"Additionally, our quality control methods have been proven to be successful. Shell Chemicals’ proprietary manufacturing processes provide a solid base for the reliable, large volume manufacture of ENORDET products."