
Enel’s Torrevaldaliga Nord clean coal power plant in Civitavecchia, Rome.
When talking about safety at energy-producing power plants, many think primarily about the safety at nuclear plants – especially after recent painful memories of the Fukushima disaster in March 2011. But when comparing safety and accident statistics of nuclear power plants with coal, oil and gas-fired plants, nuclear wins the safety contest hands down.
Workers at fossil fuel plants are constantly exposed to chemical risks, physical risk and mechanical risk. On top of that, the procurement of the base materials for coal and oil-fired plants has one of the worst safety statistics in the industry, with related pollution and health risks among the deadliest.
Related news
ERG sells 20% stake in Italian refinery to Lukoil
Italy-based refiner ERG has announced it will sell a 20% stake in the ISAB refinery in Sicily to Russian oil company Lukoil in a deal worth €400m.
Guaranteeing a safe and healthy environment for employees and communities close to a facility is therefore one of the biggest challenges in the industry, and is absolutely essential for the successful operation of a fossil fuel plant.
How well do you really know your competitors?
Access the most comprehensive Company Profiles on the market, powered by GlobalData. Save hours of research. Gain competitive edge.
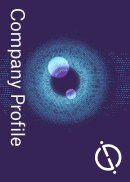
Thank you!
Your download email will arrive shortly
Not ready to buy yet? Download a free sample
We are confident about the unique quality of our Company Profiles. However, we want you to make the most beneficial decision for your business, so we offer a free sample that you can download by submitting the below form
By GlobalDataIn Italy, the country’s main operator of coal-fuelled plants, Enel, is aiming for a ‘zero accident’ environment at its facilities, and is one of the pioneers in the field of operational plant safety. In 2011, the Italian institute for work accidents insurances INAIL / ISPESL voted the company’s methodology of health and safety risks assessments as the sector’s best practice.
Here, the company’s head of safety Alda Paola Baldi gives some insights into the secrets of the health and safety practices at Italy’s largest electric utility company.
Elisabeth Fischer: How does Enel predict and evaluate risks at its fossil fuel plants?
Alda Paola Baldi: Workers at coal power plants are exposed to the same risks as workers at any other thermoelectric plant. We’re talking about chemical risks, physical risks, such as burns, vibrations and explosions, as well as mechanical risks.
Protecting our employees’ physical and psychological integrity is a top priority for us. It’s a core value of the group’s own way of doing business and leads all our processes. We conduct a continuous, suitable and systematic analysis of the occupational health and safety risks for workers associated with working processes at every Enel plant, and assess every material and organisational item which may affect the level of risk at work.
EF: What are the best techniques to prevent accidents and minimise risks at power plants?
APB: Protecting health and safety is not just fulfilling legal obligations, but it’s more a moral responsibility towards those who work with us and for us. We pursue the challenging goal of working in an environment with zero accidents, based on a prevention-focused approach, the promotion of a safety culture through intensive training and awareness-raising, the establishment of common standards throughout the group and the implementation of technological and structural interventions.
Among the fundamental principles of our health and safety policy are realising a continuous analysis of risks to health and safety of workers associated with working processes, the adoption of a system to eliminate all risks at source and the adoption of best technologies, combined with monitoring and updating work methods to continually improve safety and health standards at our plants.
We also provide equipment and tools that comply with health and safety requirements and organise and design workplaces according to ergonomic principles. We promote information and training initiatives in order to spread and consolidate a culture of health and safety and recognise the key role of each worker, by active participation and promotion of safety skill improvement initiatives. Enel, as a group, also commits to promote constant attention to health and safety among contractors and suppliers by trying to involve them in the improvement of our safety standards.
EF: What active detection technologies are in place at Enel’s coal plants?
It is a high-efficiency coal plant, consisting of three 660MW units for an overall power capacity of 1,980MW.
APB: All our coal power plants are equipped with the best technologies, and closed vacuum conveyors, safe coal transportation belts and sealed coal stockyards are only one aspect to safety. Our best example is the Torrevaldaliga Nord clean coal power plant in Civitavecchia, Rome. It is a high-efficiency coal plant, consisting of three 660MW units for an overall power capacity of 1,980MW.
What makes it so unique are the solutions developed for the coal cycle. In fact, the coal never sees the daylight, because all the phases of handling and storing the mineral, from unloading the ship to the combustion chamber, take place in absolute safety inside completely closed, depressurised and automated structures, reducing the possibility of dispersing particulates into the atmosphere.
The coal is directly removed from the holds by continuous-bucket unloaders and the transfer takes place through closed vacuum conveyors, which prevent the dust from leaking out. The coal bunker is covered by a tubular aluminium and steel structure, the coal dome, a technology used by only few plants in the world.
EF: How else do to guarantee safety for those living in close proximity to the plants?
APB: Sustainability is a key feature of our culture. We’re strongly committed to minimise the impact of our power plants on the surrounding environment. As already mentioned, all the phases of handling and storing the coal are completely safe. The plants are also equipped with flue gas treatment systems, such as desulphurisation systems (DeSox), denitrification systems (DeNox) and particulates abatement systems.
We also constantly research techniques and processes that could improve energy efficiency by preventing the production of source emissions, and we cooperate with medical authorities to implement air quality campaigns and occupational epidemiologic studies to assess the impacts on health and safety of the population living near the plants.
We’re also developing joint initiatives with environmental groups, consumer organisations, local communities and institutions. The results of these contacts with stakeholders are agreements and partnerships for joint environmental, cultural, recreational and citizen awareness projects for sustainable development.
EF: How important is health and safety training of plant employees?
APB: Our commitment to instruct, inform and train our employees on safety is very strong and safety has to be a key feature of the know-how of every employee throughout their overall work experience with Enel.
We pay particular attention to the training of newly-hired employees by technical training to improve key skills by means of practical, on-the-job activities.
But obviously our employees also get continuous training throughout their entire working life within the group. We provide tailored training and information on the proper use of equipment, the safest work practices and specific risks encountered while performing different kinds of jobs.
We’ve also created a ‘Functional Academy of Safety’ to have a training system in place for employees specifically working on safety issues. Recently, we’ve also started an initiative on training and raising awareness on safe driving. We organised driving courses aimed at both preventing and managing driving emergencies, as well as an online course on safe driving, addressing all our employees.
EF: How do you get your employees to play a more proactive role in regards to reporting safety issues?
APB: The road to a sustainable safety culture requires the transformation from the reactive to the proactive approach. Each employee must play a proactive role and be a ‘leader for safety’ in order to achieve and maintain high health and safety standards.
Related feature
Sinking ship: Oil’s fateful future
Now the global population has passed seven billion, how will our oil stocks hold up?
They have to take care of their own health and safety, as well as of other people involved who could be injured or damaged by the actions or omissions.
In the last few years, we’ve implemented several campaigns and initiatives to implement a systematic process for ‘near-miss’ communication and management. We’ve put a lot of effort into informing our employees and contractors about near-misses and why it is important to overcome the reluctance to report such events. Everyone knows that no punishment or penalties will be applied, because we can learn from our mistakes according to the principles of the ‘no-blame culture’.
Every near-miss highlights an unexpected event that causes an exposure to the risk and needs a timely action in order to avoid its recurrence. We have to understand the dynamic of each near-miss and especially their root causes, and also have to define the best countermeasures in order to eliminate the identified critical situations. By reducing the number of events that only by chance didn’t cause negative consequences, it’s possible to significantly reduce the occurrence of accidents.
EF: What have you learned from previous accidents?
APB: We’re confident that we can learn from our errors. That’s why each accident is investigated in order to identify the possible causes and to prevent its reoccurrence. In addition, events are also classified on the basis of a series of standardised causes such as behaviour, facilities, organisation and other factors for the purpose of pinpointing areas that need stronger corrective action.
With reference to coal-fuelled plants at the group level, we established the ‘coal community’ in order to share experiences and best practices, also concerning safety matters.
Furthermore, we’re currently implementing a root cause methodology for accident analysis, which makes systematic and uniform the process of investigating the causes of each accident, setting targeted actions to resolve the identified problems. The main results of the accident analysis are distributed within the group, in order to share the lessons learnt from the accident and avoid re-occurrence of these kinds of accidents in all divisions.
Related content
Eni starts slurry technology project at Italian refinery
Eni has started works for the industrial application of the Eni Slurry Technology at its refining plant of Sannazzaro de’ Burgondi, near Pavia, Italy.
Buried in the oil sands: the value of Alberta bitumen
Canada is facing major opposition as it moves to export more of its tar sands oil.