The UAE’s Emirates National Oil Company used 3D printing to model its planned facilities accurate to 1mm.
Enoc 3D printing
Two primary reasons were behind Enoc’s decision to commission Dubai-based Generation 3D to create a 6-metre architectural hybrid model for its current and future refinery facilities.
First, Enoc management wanted a physical representation of their ambitious expansion plan. Second, the model showcased the final outcome of the entire 900 square-metre site to the Enoc board, partners and customers at the Water, Energy, Technology & Environment Exhibition (Wetex) 2017 held in Dubai, and is now on display at Enoc’s company headquarters.
The challenge
For Generation 3D, the challenge began with a highly technical reverse engineering plan to rework data gathered from the existing site, to create fully 3D manufacturable files. This data was collected using the 3D laser scanning or light detection and ranging (Lidar) technology. This process alone took two months.
Following this, designers at Generation 3D began reverse engineering the Enoc oil refinery site using specialist computer-aided design (CAD) software and techniques. This was carried out in synchronisation with the site scanning team and the 3D printing to minimise lead time and drive efficiency.
Simultaneously, Enoc’s building contractor sent its proposed plans for the future development to Generation 3D in AutoCAD format. Generation 3D’s designers harmonised multiple CAD platforms such as 3DS Max, Magics, Bentley MicroStation and Pixologic ZBrush to improve file management. The team then painstakingly converted all the construction plans into 3D printable files, a process that requires time and skill.
How well do you really know your competitors?
Access the most comprehensive Company Profiles on the market, powered by GlobalData. Save hours of research. Gain competitive edge.
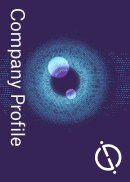
Thank you!
Your download email will arrive shortly
Not ready to buy yet? Download a free sample
We are confident about the unique quality of our Company Profiles. However, we want you to make the most beneficial decision for your business, so we offer a free sample that you can download by submitting the below form
By GlobalDataOver the course of the project, Enoc’s engineers were regularly invited to analyse the work in progress, discuss updates and provide feedback to ensure complete transparency. Once approved, the 3D designs were exported to Generation 3D’s in-house 3D print-room to be manufactured overnight.
The technology
The designers at Generation 3D used selective laser sintering 3D-printing technology for this project. This was due to the durability of the nylon material used, the high accuracy and tolerance threshold (accurate to 50 microns) and flexible printing methods.
The designs were organised into batches and 3D-printed alongside the manual fabrication of the model base and podium. This combination of manual and digital manufacturing helped streamline the project and greatly reduced lead-time.
Updates and flexibility
The design of the model allows for sections to be easily altered and updated zone by zone, should there be any revisions in the site plan.
Max Reynard is a director at Generation 3D.
MEED
This article is sourced from Offshore Technology sister publication www.meed.com, a leading source of high-value business intelligence and economic analysis about the Middle East and North Africa. To access more MEED content register for the 30-day Free Guest User Programme. https://www.meed.com/registration/
Related Company Profiles
Offshore Technology Corp
ENOC LLC
Emirates National Oil Co Ltd