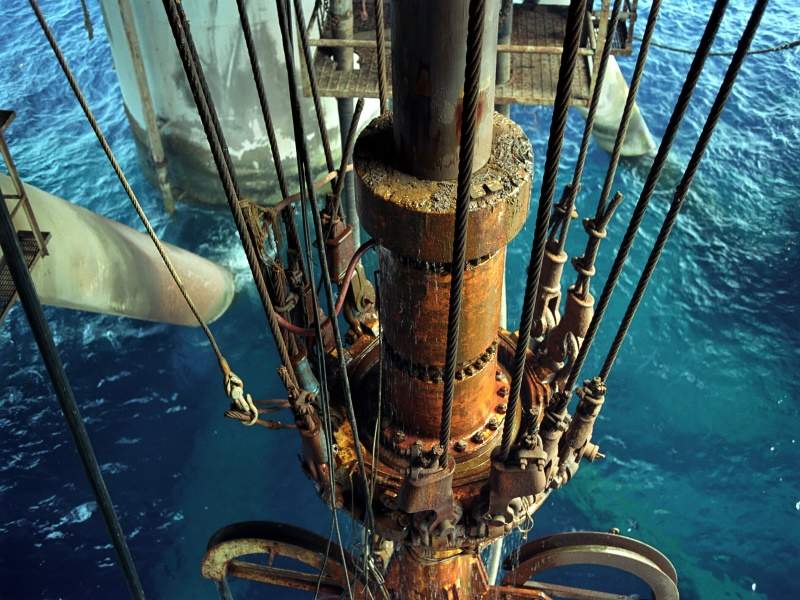
During the downturn, automation became a key theme in the offshore oil industry as companies looked to cut costs and reduce headcounts. As the price finally recovers will the industry start investing in tech again and if so, what will the next generation of rigs look like? Patrick Kingsland investigates.
It was, most oil executives agree, the worst downturn in a generation. From a high of $115 per barrel in August 2014, prices collapsed to below $30 dollars per barrel in the early months of 2016. In countries like Venezuela – whose entire export economy is dependent on oil – the effects are still being felt.
For the oil industry, one of the natural responses was to decrease supposedly “bloated” head-counts and replace jobs with automation., Automation was rarely considered a priority during the previous oil boom, with most companies too busy extracting resources to care. When the prices fell, those priorities changed.
“The technology had been underway for multiple years but the downturn accelerated it,” says James West, senior managing director at Evercore ISI.
A tentative recovery
While a tentative price recovery is now underway, few think the trend towards automated machinery is likely to be reversed. A recent study conducted by Kimberlite Oilfield Research found that 41% of the wells drilled in the next five years will make use of automated drilling technologies.
Part of the reason, says West, is that the price recovery is far from complete, leaving the case for automation intact. “While the land industry in North America has come back with a recovery in shale, offshore is still languishing and day rates are barely above break even levels,” he says. “While we see some improvement going into 2018 I don’t expect us to see a full price recovery until late 2019 and 2020.”
A bigger reason is that the benefits of automation have become more established as oil and gas operators increasingly deploy the technology.
“I think companies are starting to see the benefits of automation from a safety point of view and from an ageing-workforce point of view,” says Mitch Pryor, co-founder of the Drilling and Rig Automation Group at the University of Texas at Austin. “Particularly with some of the more experienced rig-drillers that need retaining, automating certain tasks will make their jobs more doable.”
For Pryor, there is also the issue of peak consumption – the increasingly popular hypothesis that consumption of oil and gas will at some point stop rising.
“If that does happen I think oil companies will start to recognise that to be competitive going forward they need to capable of withstanding volatile oil prices,” Pryor says. “One way to maybe do that is to introduce more automation. This is motivating companies to study it a little more enthusiastically than they had in the past.”
Stalled progression
Of course, automation is not entirely new in the drilling industry. “A lot of the first stuff to be automated was the speed controls associated with managing the RPM and the weight on bit,” says Pryor. “After that it went more into automation of some of the safety equipment, and the detection of kicks and individual devices like iron roughnecks and pipe handling systems.”
Still, there is a sense that automated drilling technology hasn’t progressed quite as far as one might have expected, with full-automation still some way off.
One of the main challenges, analysts say, is lack of integration. “There are some examples of heavy automation in some parts of the operation like pipe handling, MPD, and other areas but none of these systems were integrated with each other,” says DNV GL Oil and Gas principal researcher Tore Kuhlne.
According to Pryor this is down to the way the industry is structured. “People build rigs and iron roughnecks and different companies buy different components,” he says. “There are a few companies that are big enough to look at the problem as a whole but a lot of the innovation is set across a diverse number of organisations around the globe.”
As the industry pulls out of the worst downturn in a generation, the space for offshore drilling investments also remains limited. “With the equipment suppliers we’ve seen a lot of R&D capital spent on automation, probably in the 5% of revenue range,” says West. “But I think the offshore drilling contractors are pretty capital-starved. They are just trying to find work right now.”
Space for investment could change over time, however. “I think once we get to a recovery and they start to generate cash again, we should start to see CAPEX budgets raised in order to further the automation drive,” West says.
Nor do companies need to invest in totally new rigs to embrace elements of automation.
“One of the debates we see is whether you should put automation on existing rigs or simply automate rigs [from scratch],” Pryor says. “Ideally you would do the latter but the turn-over of rigs is so slow that the former might be the more feasible way of actually getting things automated.”
New technologies are on the horizon
Perhaps most importantly, Pryor notes a change in attitude among the industry over the past few years. “When we first took our ideas to companies the early feedback we got was ‘why would we fully automate – we don’t even trust the data that our sensors are giving us’. The companies are now saying the data we are getting from our sensors is something we can trust and use to make decisions possibly without a driller in the loop.”
This increasing appetite means new developments are on the horizon, Pryor adds. “We’re seeing supervisor control for tripping that allows for the integration of the pipe handling systems and iron roughnecks in a way that humans don’t need to be in the loop at all,” he says. “We’re also looking at actual robotics on rigs: mobile manipulators that handle fire suppression equipment, that can turn valves related to managed pressure drilling and can turn on switches for high-voltage power.”
For the time being, the offshore industry will likely lag behind its onshore counterparts. “On an onshore rig we have drilled wells from remote locations that were fully automated with very few people at the actual rig sites,” says West. “Because of the challenges and concerns about safety offshore it is a little bit behind.” But as short-term and long-term market conditions evolve, this is likely to change. After all, as West says, “most of the jobs that are on a rig can be fully automated”.