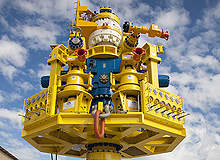
The months following Deepwater Horizon’s explosion and oil spill on the Macondo Prospect in the Gulf of Mexico were long ones for environmentalists, the US Government and the offshore industry alike. The fact that repeated attempts to cap the wellhead were unsuccessful made the three-month ordeal all the more tortuous.
In the wake of the spill, the industry and the wider world has switched on to the possibility of a similar disaster occurring again. Particularly given the increasing depths at which deepwater platforms are now operating, the logistics behind capping a leaking well are mind-boggling.
As a result, a number of emergency well capping devices are concurrently in development or under construction now. Some are intended and tailored for use in particular offshore regions, while others are being offered to oil companies as a kind of global insurance policy against any future disasters.
In Houston, the Marine Well Containment Company (MWCC), a non-profit organisation formed after the Deepwater Horizon disaster and dedicated to improving spill response in the Gulf of Mexico, has developed a containment system for use in the Gulf in the event of an emergency. The current system is an interim version of the company’s final expanded well capping device, but can still contain up to 60,000 barrels per day (bpd) of oil with the ability to withstand 15,000 pounds per square inch (psi) of pressure. The expanded version in development will be able to contain up to 100,000 bpd of oil.
MWCC announced earlier this month that its interim system had been cleared for containment operations in water depths of up to 10,000ft, a significant increase on its previous 8,000ft threshold and a clear sign of the need for modern well capping devices to be deployable in even the most challenging conditions.
“This increase in our capability demonstrates our commitment to providing a comprehensive deepwater well containment system for the US Gulf of Mexico,” said MWCC CEO Marty Massey. “Our goal is to continually advance deepwater well containment technology to keep pace with our member companies’ needs.”
Case study: the UK’s tailored well capping device
The UK Continental Shelf (UKCS) has an excellent safety record in its several decades of offshore oil and gas operations, and the industry wants to keep it that way. “There has not been a single blow-out in this country in over 20 years of UK offshore operations and we must ensure that it remains this way,” said UK industry body Oil & Gas UK’s Malcolm Webb in March this year.
Part of this commitment is a new well capping device for the region, conceived and developed by the Oil Spill Prevention and Response Advisory Group (OSPRAG) in conjunction with BP and engineering firm JP Kenny, and owned by Oil Spill Response. Having been quickly designed and commissioned, the device is currently being built by Cameron Ltd in Leeds, with factory acceptance testing due in July. We talked to Oil & Gas UK supply chain director Brian Kinkead, who was chair and lead of the OSPRAG technical review group that developed the device, about its design and how it is tailored for the UKCS.
Chris Lo: What was thinking behind the commissioning of the new well capping device?
Brian Kinkead: After Macondo, when we formed OSPRAG, one of the things that DECC [Department of Environment and Climate Change] pointed out to us was that we didn’t have any contingency in terms of a capping device. We were obviously watching what was happening over at Macondo. So DECC asked us to consider whether we should have our own capping device, and what should that look like. So we put together a small team, probably about six or seven of us, and we looked at what was happening, we looked at our own unique conditions in the North Sea, and then developed a conceptual design. After that we went into detailed design and on into procurement.
The capping device we’ve got is very different in concept to what you’ll see in the Gulf of Mexico with Marine Well Containment, with Wild Well Control, and with all the other organisations around the world who are very much focussed on just putting out a big BOP [blow out preventer]. The BOPs that they’re using, which are obviously perfectly adequate, come in at around the hundred-ton mark. What we wanted to do was come up with a device that would allow us the maximum range of deployability from vessels or rigs. So we went down the route of coming up with a gate valve device, and that weighs 38t, and that allows us to deploy it on wires over the side of a vessel, or through the moon pool on a vessel, depending on which vessel is there. And it also gives us access to a wider range of rigs, because that’s about the crane limit on some of the other rigs that could also deploy it.
CL: What were the other main priorities for the device’s design?
BK: Linked to size and weight is the question of whether we could actually deploy it over a flowing well. We were concerned, the lighter we got this, could we actually put it over a well flowing at 75,000 barrels a day, west of Shetland? So we’ve done an awful lot of modelling. The modelling was initially done by two companies to make sure we were on track and coming up with similar answers, and then we proceeded with one company to finalise the work. What that proved was that we could deploy the cap over a plume of oil flowing at 75,000 barrels of oil per day. That helped us understand what weight we could bring the device down to, as well as what the sizing of the valves would be, because the valve sizing was important in terms of weight.
CL: Did any experience from well capping operations at Deepwater Horizon feed into the design?
BK: The project manager from BP who is working with Cameron on the build of the equipment was actually one of the key figures who was involved in the capping and containment of Macondo for BP. The best way to transfer learning is through people, and we had one of the key individuals on Macondo come across and he’s actually leading the design and build phase of this capping device.
CL: Will the device be deployable in the often harsh conditions of the North Sea?
BK: Yes, it will be. At the time of our report many vessels in the UKCS were around that could deploy the device in a varying range of sea-states; we had about 14 vessels identified that could have run it. That gave us a high degree of confidence that in the event of such an incident that we wouldn’t be waiting for a vessel. The time it would take us to deploy the cap and have it ready to mobilise on to a boat would be the critical path, as opposed to finding a boat.