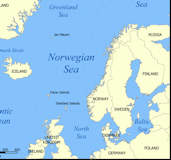
World Expro: What challenges do the inspection, maintenance and repair of Statoil’s subsea pipelines present in the North and Norwegian Seas?
Åse Margrethe Odland: Statoil operates and has the technical responsibility for about 10,000km of subsea pipelines on the Norwegian Continental Shelf. Diameters range from 4in to 44in, lengths vary from a few hundred metres up to 1,200km and water depths from sea level to 700m. The products they carry include unprocessed hydrocarbons directly from the wells, dry gas (sales gas), produced water for injection, condensate, heavy oil, multiphase, CO2 and chemicals.
Repairing subsea pipelines might be challenging, but Statoil has built up an extensive contingency preparedness for such pipelines. Different methods are developed depending on water depths and pipeline dimension. For repairs beyond diving depth, remote-operated equipment is used.
Statoil uses a risk-based approach for design, and a combination of risk and condition-based approach for inspection and maintenance.
This requires a thorough knowledge of the various threats and failure mechanisms, and their development. They vary along the pipeline route as well as during the pipeline lifetime. The threats might vary in range, they may come from third-party activities such as trawling, internal threats like corrosion, or even from the people or organisation that are taking care of the integrity of the pipelines.
Another challenge with respect to control of technical integrity is changing design premises. To ensure that the risk is within acceptable limitations, we have to regularly check the premises. We have, for instance, recognised that trawler boards have increased in size, dimension and weight. And in a few cases intervention work has been needed to take account for the increased impact loads.
Weather may also be a challenge, both for inspection activities and for the pipelines itself. Therefore, most of the external inspections by ROV are taking place during summer season. However, weather can change the pipeline condition over the year, for example, from winter season to summer season. Hence, inspection in such seasonally sensitive areas should be performed at the same time of year. Otherwise it is hard to identify if potential changes in condition are due to seasonal variations or other reasons.
How well do you really know your competitors?
Access the most comprehensive Company Profiles on the market, powered by GlobalData. Save hours of research. Gain competitive edge.
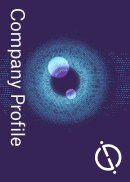
Thank you!
Your download email will arrive shortly
Not ready to buy yet? Download a free sample
We are confident about the unique quality of our Company Profiles. However, we want you to make the most beneficial decision for your business, so we offer a free sample that you can download by submitting the below form
By GlobalDataIs it possible to maintain all of Statoil’s pipeline assets using a single holistic inspection regime, or does each pipeline require unique maintenance practices?
In general, each type of pipeline requires a unique approach with respect to inspection, maintenance and repair. Issues that might influence the strategy and approach are diameter, buried or exposed pipelines, product, water depth, soil condition and third-party activities.
The smallest pipelines are to a large extent buried for protection against third-party impact (mainly trawling) and lateral and/or upheaval buckling. External inspections are performed to verify that these pipelines remain buried. Internal inspection is used to verify potential corrosion, internal and external.
The latter is very rarely seen on subsea pipelines, due to the use of sacrificial anodes and the fact that seawater has excellent electrical conductivity. Most of these pipelines are made of carbon steel.
The larger pipelines are mainly lying exposed on the seabed. Hence they are more vulnerable to third-party impacts such as trawling and anchor drops. Free spans might also be a risk for some of these pipelines. Inspections are performed by visual or acoustic techniques, or a combination of these.
Tool-platforms might be ROVs, towed ‘fish’ or ships. In the shallow and sandy areas in the southern part of the North Sea the visibility can be a challenge; thus sonar is often a preferred technique there.
All the big pipelines are made of carbon steel and protected against external corrosion by sacrificial anodes, a system that is working well. The most important method for internal condition control is product monitoring in each end. Results from this monitoring tell us whether corrosion might be an issue or not, and when an internal inspection is due.
How has technology made the job of pipeline inspection easier?
Both inspection methods and tools have developed over the years. This is also the case for methods and tools for evaluation and visualisation of inspection results. Today, inspection results are digitalised and hence more available. We are able to better predict timing and identify the most critical sections. This has helped us to do more cost-efficient inspections with better quality.
Statoil believes that technology can improve its performance and is therefore constantly looking to improve certain areas. The company is at the forefront of developing new inspection methods and tools together with our suppliers, research institutes and other pipeline operators.
One example is the first multi-diameter inspection tool, the In-line XHR MFL pig, which is based on magnetic flux leakage. XHR means it has extra high resolution capability (and can detect and size smaller defects than lower quality tools), and it is able to inspect heavy wall pipelines. The tool can cover all pipeline diameters between 28in and 42in in the same run.
As assets reach the end of their original design life, how does this affect the frequency and type of inspections carried out?
In general, the inspection frequencies decrease when you come closer to the end of the lifetime. If there are well-documented verifications of the failure mechanism – for example, corrosion rate – you don’t need to do more frequent inspections than earlier. And the better the inspection tools are, the longer interval you can accept. In other words, more uncertainty in inspection results requires more frequent inspections. Statoil always aims for high-quality inspection tools to reduce the uncertainty to a minimum.
How does the inspection, maintenance and repair of Statoil’s pipelines fit in with the organisation’s asset integrity management system as a whole?
Statoil uses a risk and condition-based approach for its inspection, maintenance and repair. Both the integrity management system and the organisation has been developed and built to suit this approach. Work methods and governing documents also reflect this.