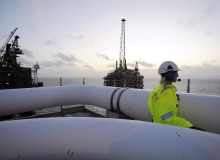
Major accidents and oil spills such as Deepwater Horizon, the Mumbai High North and Piper Alpha catapulted health and safety issues into the spotlight of policy-makers, oil and gas companies and their operators and employees.
But while efforts to reduce the likelihood of incidents have traditionally concentrated on technology and operations, prevention measures today also recognise human factors as major contributors to operational safety and the optimisation of system performance offshore.
A January 2012 survey of offshore safety professionals, conducted by Oil & Gas iQ, reported that 48.6% see human factors as the biggest challenge offshore has to face today and in future. This is compared to 10.8% who see problems with technology and equipment as the key issue. Perhaps not surprisingly, nearly 75% believe that since Deepwater Horizon there is more pressure being placed on industry by regulators to improve health and safety.
However, the true role of human factors in the prevention of accidents is still very underrated by the industry, believes PTP-Global director Tim Southam, a UK-based human factor and safety consultancy.
Speaking about the subject before the Arena International Oil and Gas Technology Forum (OGTF) on 18-20 April 2012 in Aberdeen, he explained what more should have been learned from previous lessons.
Elisabeth Fischer: Would you agree human factors are the biggest challenge the offshore industry is facing today?
Tim Southam: The recognition of human factors in the oil and gas industry is not widespread and below the standard of sectors like the nuclear sector and railways. Human factors have a very wide scope in major hazard work that runs through the safety management system, the organisation for safety and the culture of a site.
How well do you really know your competitors?
Access the most comprehensive Company Profiles on the market, powered by GlobalData. Save hours of research. Gain competitive edge.
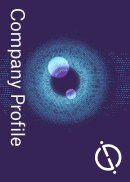
Thank you!
Your download email will arrive shortly
Not ready to buy yet? Download a free sample
We are confident about the unique quality of our Company Profiles. However, we want you to make the most beneficial decision for your business, so we offer a free sample that you can download by submitting the below form
By GlobalDataStudies have shown that up to 90% of accidents are attributable to some degree to human failures. The failure of people at many levels within an organisation can contribute to a major disaster, even though it was not the sole cause but one of a number of causes, including technical and organisational failures. The prevention of major accidents depends to a large degree upon human reliability at all sites, no matter how automated.
Human factors are often seen as a rather nebulous concept. The topics range from broad, high-level issues such as staff competence, to those covering specific subjects like fatigue risks and alarm handling. Many of these subjects will be part of the organisation’s activities but are not recognised under the human factors umbrella. Therefore, when questioned on what human factors are, many people in an organisation struggle to understand what the term means.
EF: How has the role of HF changed in light of events such as Deepwater Horizon?
TS: Many disasters over the last 20 to 30 years have highlighted major issues and deficiencies in the way organisations manage risks and hazards. There are people in the oil industry now that don’t remember Piper Alpha in 1988. As an industry, the oil and gas sector is generally behind others in embracing change and integrating human factors. Probably the worst part was to read through the Deepwater Horizon literature, and repeatedly see mistakes that we hoped had been addressed in the recommendations from earlier incidents.
Regulations and statutory instruments that are not clear as to what is required, and a regulator that is undermanned to enable inspections to push organisations in the right direction, don’t help the situation. The HSE has specialist human factors inspectors who understand what is needed, but there are only 24 hours in a day and there are not enough of them. For me as a contractor, it is difficult to persuade senior management that money needs to be spent to ensure more efficient and safer operations through mitigation of human errors and mistakes. We continue to label human error as a bad thing, but fail to rectify the situation and pigeon-hole the subject.
To avoid being overwhelmed with new regulation, the industry needs to be sure of the highest integrity, not just asset integrity but also human integrity, deep and wide across all operations. We should acknowledge the deep water and high pressure nature of the Macondo operation, but in fact the problems were in many ways predictable and certainly not the result of some ‘unknown unknown’.
EF: What can be learned from earlier accidents?
TS: For me there are a few simple things that we should bear in mind that could help us take a big step forward.
First of all, the technical near misses are easy to learn because they can be scientifically analysed. It is not so easy to learn from the behavioural near misses but we have to get better at routinely doing that analysis as there will almost always be a human element.
In a global industry with horrendous potential for getting things wrong, is it too much to expect that operators will adopt best practice wherever they operate? Most operators are driven by the organisational drivers and respond to their perceptions of those forces. Accountability for safety and integrity cannot be contracted out. Managers have to be really clear about who is responsible for what, especially in a changing or emergency situation.
In my experience emergency and crisis training for managers and crews developed well after Piper Alpha, but when the squeeze comes on costs often the first thing to suffer is training. We also should be extremely careful of late changes of plan. Rushed, last minute and bad decisions made in the middle of the night are all too familiar to most of us. Another question is if we’re complacent about our safety performance and culture. Deepwater Horizon held an onboard ceremony on the day of the incident. Such celebrations are lagging indicators. We should take more notice of things we are doing, leading towards genuine improvements.
EF: What are the biggest HF threats to safe offshore operations?
TS: We already have regulations for safety case and COMAH, standards, audit reports, academic papers and the like. The legislation is not aligned and often written by different parts of the HSE organisation. The loss of a prescriptive approach to safety cases and COMAH safety reports, consistency of these reports between assets and sites is poor despite best efforts by the regulator.
Many organisations do not integrate human factors at the design phase due to lack of training and understanding by senior engineers and managers. There is a reluctance to spend ‘Capex’ money when you can put the expense onto ‘Opex’ – politics plays too much part in decisions as to where to spend the money. Thus, plant and equipment gets into service which often does not include human factors.
Human factors and ergonomics best practice is not integral within the safety management systems in many organisations, and predictive human error analysis is not used during the procedure writing process to minimise the opportunity for human failure and mitigate for many human issues. Furthermore, human error analysis in accident or incident investigations does not go deep enough into errors to seek a resolution of issues. Performance influencing factors often lay dormant in the organisation without being resolved.
EF: What human error reduction strategies can diminish these threats?
TS: We need to identify what is predictable, manageable and preventable and set goals, accept how we, as management, can influence the outcome and reinforce the behaviours, plus have everyone understand the reasons why mistakes occur and apply lessons learned. Particularly helpful here is to understand the principles of human performance, which include that humans are fallible and that even the best people make mistakes.
EF: What more is to be done in the future?
TS: In my experience of some fifteen years of running my business, the focus has always been on the frontline worker that has the problems. However, following the investigation of major incidents, it has become increasingly clear that the role of management and organisational factors must be considered, rather than placing responsibility solely with the operator.
That said, audits rarely consider issues such as the quality of management decision making or the allocation of resources. Furthermore, ‘safety culture’ is seen as being something which operators have and it has been found, following the investigation of major accidents, that management have not acknowledged that the development and maintenance of a safe culture lie within the bounds of their responsibility.
Andrew Hopkins wrote in Lessons from Longford that if culture, understood as a mindset, is to be the key to preventing major accidents; it is management culture rather than the culture of the workforce in general which is most relevant. What’s needed is a management mindset that identifies and controls every major hazard and a management commitment to make available whatever resources are necessary to ensure the workplace is safe.
Arena International’s Oil and Gas Technology Forum (OGTF) is taking place from 18-20 April 2012 in Aberdeen, UK.